Доменное производство
Доменные печи являются основным агрегатом для переработки железной руды, хотя количество разнообразных агрегатов для прямого восстановления железа постоянно растет. В доменной печи из руды, которую подвергают окускованию (агломерация или производство окатышей), производят жидкий чугун и побочный продукт – шлак.
Схема доменного процесса дана на рис. 5. Упрощенно технологию доменной плавки можно описать следующим образом. Шихта, в составе которой присутствует железорудная часть (окатыши, агломерат), кокс, известняк и флюсы, загружается по скиповому подъемнику (в современных печах по ленточному транспортеру) и через засыпной аппарат сверху подается в шахту печи.
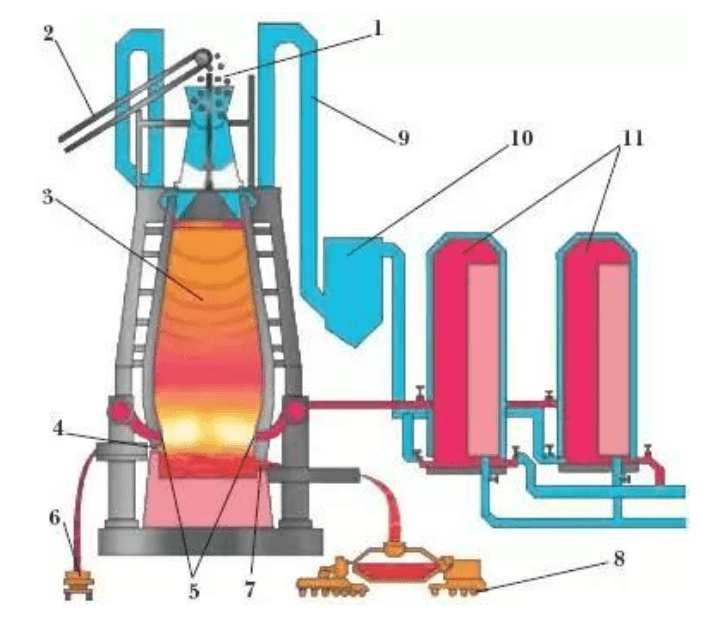
В нижнюю часть печи (горн) через фурмы подают подогретый воздух для горения и заменители кокса. Возле фурм происходит горение кокса с выделением угарного газа – СО, который поднимаясь вверх по столбу шихты восстанавливает оксиды железа, содержащиеся в рудной части. По мере опускания шихты вниз происходит ее нагрев и расплавление. Жидкий чугун сливается через чугунную летку в чугуновоз и направляется в сталеплавильный цех.
Как уже отмечалось в предыдущей статье, доменное производство занимает первое место по энергозатратам среди других металлургических производств. В себестоимости чугуна около 50% всех затрат приходится на стоимость энергоносителей, превалирующую часть которых составляет кокс. Вследствие чего, основным энергосберегающим мероприятием при производстве чугуна является снижение расхода кокса.
Снизить расход кокса можно как за счет различных технологических мероприятий непосредственно направленных на снижение расхода, так и за счет замены кокса на другие виды топлива, в частности природный газ. Однако в связи с резко возросшей стоимостью природного газа большинство металлургических предприятий Украины сократили или полностью вывели его из состава дутья, что в итоге способствовало существенному (на 20…30%) росту удельного расхода кокса.
Основные пути снижения расхода кокса следующие:
- повышение качественных характеристик кокса: повышение прочности, снижение количества мелочи, влажности, золы и содержания серы и щелочных соединений, что обеспечит более ровный ход печи и повышение эффективности процесса;
- повышение содержания железа в шихте на 1% дает экономию кокса до 1,5%, этого можно добиться за счет более глубокого обогащения руды;
- применение заменителей кокса: пылеугольное топливо (ПУТ), природный газ, мазут, восстановительные газы CO и H2 , древесный уголь. Добавление в шихту продуктов пиролиза древесины или антрацита. Эти мероприятия позволяют снизить расход дорогостоящего кокса. Расход ПУТ в мире составляет 250..280 кг/т, на Донецком металлургическом заводе – 125 кг/т, природный газ 50…100 м 3 /т, мазут 40…60 кг/т;
- обеспечение постоянства свойств шихты (усреднение);
- улучшение конструкции засыпных агрегатов, применение бесконусных засыпных устройств (рис. 6), оптимизация порядка подачи материалов в печь, повышение давления на колошнике;
- повышение температуры воздуха для дутья до 1250…1400 °С, а природного газа до 600 °С;
- сокращение выхода шлака до 250…300 кг/т чугуна;
- увеличение объема доменных печей;
- увеличение длительности кампаний доменной печи;
- применение разнообразных средств автоматизации и контроля.
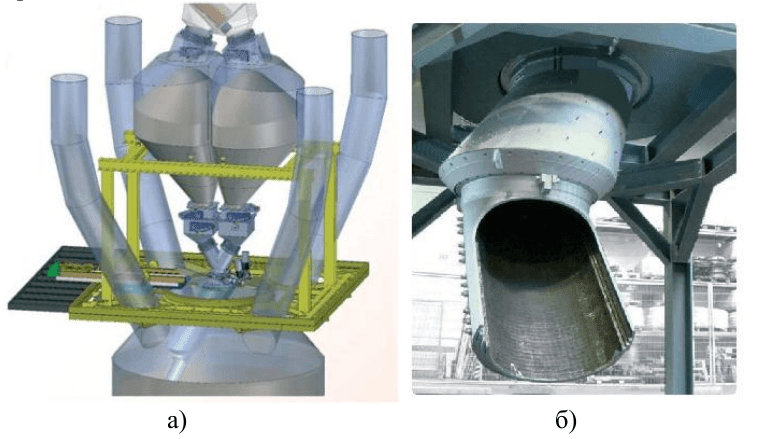
Также в доменном производстве в качестве горючего и ВЭР избыточного давления используется доменный газ, тепло воды из системы охлаждения, тепло шлака и т.д.
Сталеплавильное производство
В настоящее время для выплавки стали в массовом производстве используют различные типы печей, которые представлены на рис. 7. При анализе эффективности методов по энергосбережению в сталеплавильном производстве следует учитывать, что энергоемкость выплавки стали – это сумма затрат энергии как непосредственно в самом сталеплавильном производстве, так и на всех предшествующих передела.
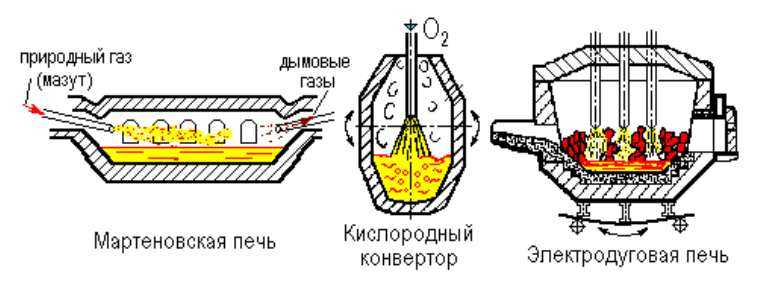
Поэтому повышение доли металлолома в шихте резко снижает расход первичной энергии на выплавку стали. Так как затраты энергии на сбор, подготовку и транспортировку 1 тонны
металлолома в среднем 4 раза ниже чем на выплавку 1 тонны чугуна.
Сопоставление некоторых способов выплавки стали по расходу энергии приведено на рис.8.
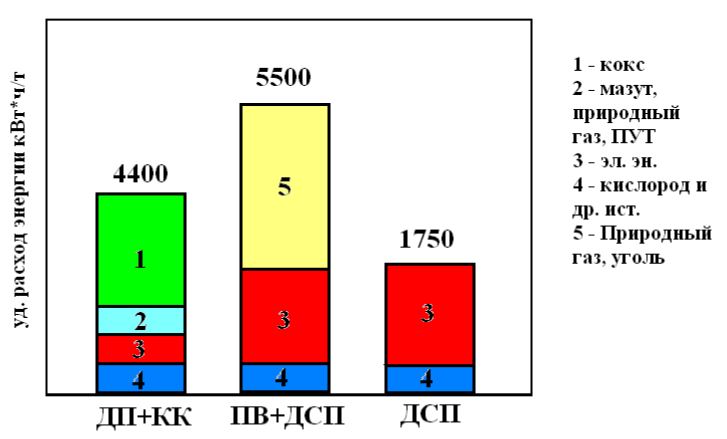
Данный анализ позволяет сделать вывод о том, что наименее энергозатратным является процесс получения стали в дуговой сталеплавильной печи (ДСП), в то время как схема «прямое восстановление железа (ПВ) + ДСП» наиболее энергозатратна за счет использования большого количества природного газа в данном процессе. Схема получения чугуна в доменной печи (ДП) с последующей переработкой его в сталь в кислородном конвертере (КК) занимает промежуточное положение.
В целом, основными направлениями снижения энергоемкости сталеплавильного производства являются:
- установление оптимальной структуры сталеплавильного производства (сокращение мартеновского производства и т.д.);
- максимальное использование всего ежегодно образующегося на предприятии металлолома;
- сокращение расхода наиболее энергоемких материалов для выплавки стали (чугуна, ферросплавов и т. д.);
- совершенствование технологии и конструкции механизмов и устройств сталеплавильных агрегатов;
- повышение температуры исходных материалов для плавки (чугуна, лома и т.д.);
- увеличение объемов внепечной обработки стали;
- утилизация физического и химического тепла отходящих газов, тепла шлака, охлаждающей воды и металла;
- расширение объемов непрерывной разливки стали;
- выбор оптимальных с точки зрения энергозатрат схем расположения цехов по выплавке чугуна, стали и производству проката.
Поскольку мартеновские печи практически полностью выведены из эксплуатации, рассмотрим пути снижения затрат только в кислородно-конвертерном и электросталеплавильном
производстве.
Снижение затрат энергии в кислородно-конвертерном процессе
Основным сырьем для кислородного конвертера является жидкий чугун (доля в составе шихты – 70…80 %) и стальной лом. После загрузки конвертера производится продувка ванны жидкого металла чистым кислородом под высоким давлением. Продувка может быть верхней (через погружную фурму (рис. 7), нижней (через донные фурмы) и комбинированной (и снизу и сверху, при этом снизу может вдуваться только инертный газ). Во время продувки кислород окисляет углерод и кремний, содержащиеся в расплавленном металле с выделением большого количества тепла, которое расплавляет металлический лом. Однако этого количества тепла недостаточно для расплавления большего количества металлолома, чем 20…25 %.
Конвертерный процесс сам по себе наименее энергоемок по сравнению с другими сталеплавильными процессами, однако использование большого количества чугуна для плавки обуславливает большую энергоемкость конвертерной стали.
Наиболее значимыми путями снижение затрат энергии в кислородно-конвертерном процессе являются:
- повышение температуры чугуна заливаемого в конвертер, что позволяет добавить большее количество металлолома к шихте;
- увеличение доли металлолома и его предварительный подогрев отходящими газами;
- подача дополнительных энергоносителей в конвертер (измельченный уголь, природный газ);
- совершенствование технологии, в частности переход на комбинированную продувку, которая позволяет существенно уменьшить потери железа в шлаки пыль;
- проведение десульфурации, десиликонизации и дефосфорации чугуна в отдельных агрегатах или в желобе для выпуска чугуна (а не в конвертере и доменной печи);
- бесшлаковый выпуск стали с установкой затворов на корпус кислородного конвертера, которые перекрывает выпускной канал конвертера в момент появления частиц шлака в потоке выпускаемого металла. Возможно применение также газодинамической отсечки шлака. Появление шлака в этом случае контролируется инфракрасными или электромагнитными датчиками;
- применение более прочных огнеупоров, что обеспечивает большую стойкость кладки и соответственно увеличение производительности;
- применение технологии раздува шлака, согласно которой после выпуска стали, через фурму вдувают азот под большим давлением и он разбрызгивает шлак по футеровке конвертера, что повышает ее стойкость;
- использование системы лазерного сканирования состояния футеровки конвертера, что позволяет производить ее оперативный ремонт, тем самым увеличивая ее стойкость.
Снижение затрат энергии в электросталеплавильном производстве
В настоящее время для выплавки стали применяют в основном дуговые сталеплавильные печи, питаемые переменным или постоянным током. В ДСП переменного тока (рис. 7) установлено три графитовых электрода (по одному на фазу), а в ДСП постоянного тока – два: один верхний графитовый и один донный – медный. Достоинством дуговых электропечей является то, что в них выплавляют основную часть высококачественных легированных и высоколегированных сталей, которые затруднительно, либо невозможно выплавлять в конвертерах и мартеновских печах.
Принцип работы дуговой электропечи основан на создании электрической дуги, которая имеет температуру 5000…6000 К, между графитовыми электродами и металлоломом (рис. 6). Благодаря возможности быстро нагреть металл, можно вводить большие количества легирующих добавок и иметь в печи восстановительную атмосферу и безокислительные шлаки, что обеспечивает малый угар вводимых в печь легирующих элементов.
Кроме того, имеется возможность более полно, чем в других печах, раскислять металл, получая его с более низким содержанием оксидных неметаллических включений, а также получать сталь с более низким содержанием серы в связи с ее хорошим удалением в безокислительный шлак. Также есть возможность плавно и точно регулировать температуру металла. Однако следует отметить, что в настоящее время большинство вышеуказанных операций производится в установках внепечной обработки стали. А основной функцией электросталеплавильной печи является фактически только расплавление металла.
Основными путями снижения затрат энергии в электросталеплавильном производстве являются:
- сокращение длительности плавки путем повышения удельной мощности трансформатора;
- уменьшение продолжительности заправки, доводки с выносом операций легирования, раскисления, модифицирования и десульфурации в агрегаты внепечной обработки;
- предварительный подогрев шихты и использование ВЭР (тепло отходящих газов, охлаждающей воды, и жидких шлаков). В частности, подогрев лома отходящими газами позволяет экономить до 40% электроэнергии;
- продувка металла инертными газами через донные фурмы и использование устройств электромагнитного перемешивания позволяет сократить цикл плавки;
- увеличение высоты стенок печи позволяет производить однократную загрузку шихты только одной бадьей с металлоломом;
- использование дополнительно природного газа, сжигаемого в газокислородных горелках, позволяет снизить общий расход энергии до 10%.
Непрерывная разливка стали
Непрерывная разливка стали сама по себе является эффективным мероприятием по снижению затрат в металлургическом производстве. За счет использования машин непрерывного литья заготовок (МНЛЗ) из производственной цепочки исключается обжимной передел, что позволяет существенно снизить потребление энергоресурсов для производства готового проката.
В МНЛЗ расплавленный металл из сталеразливочного ковша, установленного на поворотном стенде, через промежуточный ковш заливается в медный, охлаждаемый водой кристаллизатор, в котором начинает формироваться твердая оболочка (корочка) непрерывнолитого слитка.
Из кристаллизатора слиток непрерывно вытягивается тянущими роликами и попадает в зону вторичного охлаждения, где он со всех сторон охлаждается водой из форсунок. Далее следует зона охлаждения на воздухе, в которой слиток окончательно затвердевает, после чего он режется на мерные длины с помощью газовых резаков. Схема МНЛЗ радиального типа и ее внешний вид приведены на рис. 8. Также МНЛЗ бывают вертикальные, вертикальные с изгибом слитка на 90°, криволинейные, горизонтальные, валковые, ленточные и т.д.
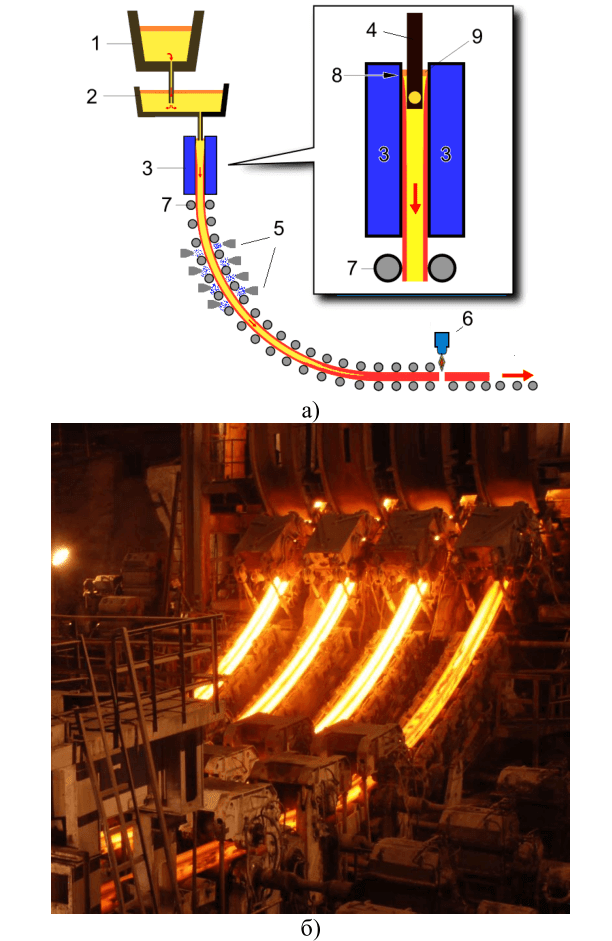
В настоящее время на МНЛЗ разливают непрерывнолитые блюмы, слябы и заготовки. При этом наибольшим энергосберегающим потенциалом являются установки, способные отливать непрерывнолитой слиток сечением, близким по форме и размерам к готовому изделию (прокату), что существенно сокращает цикл производства, потребление энергоресурсов и обеспечивает более приятные деформационные условия. К таким машинам относятся тонкослябовые агрегаты, агрегаты валковой разливки-прокатки и установки литья заготовки типа «собачья кость», которые используются для последующей прокатки в балки или рельсы. В настоящее время также активно проводятся исследования по производству квадратной заготовки со скругленными углами радиусом 15…30 мм вместо 3…8 мм (как принято сейчас). Это позволяет обеспечить более благоприятные условия деформации в прокатном стане (например отсутствие брака по «закату») и имеет определенные технологические преимущества в самом процессе разливки.
Также существенно позволяет экономить энергоресурсы объединение МНЛЗ с прокатным станом в единый литейно-прокатный агрегат (ЛПА). Что позволяет вести прокатку без отдельного нагрева заготовок.
В случае же использования отдельно стоящей МНЛЗ без применения технологий транзитной прокатки или горячего посада, практически все тепло кристаллизующегося металла теряется. Потери тепла на МНЛЗ составляют: в окружающую среду 5 %, на систему охлаждения кристаллизатора 5%, с водой и паром системы вторичного охлаждения – 40%, остальное тепло 50% содержится в твердом непрерывнолитом слитке.
Комплекс мероприятий по утилизации и сбережения тепла на МНЛЗ включает:
- комбинированное двухконтурное охлаждение кристаллизаторов водой с утилизацией тепла;
- применение системы водовоздушного вторичного охлаждения слитка с пароотводом и утилизацией тепла в пароотводящем тракте;
- установка термосберегающих и теплоутилизирующих экранов в линии МНЛЗ;
- использование тепла заготовки для последующей транзитной прокатки или горячего посада, а также создание литейно-прокатных агрегатов;
- применение нанопорошковых модификаторов (Y2O3, TiN, TiCN и др.), которые вводятся в виде проволоки или ленты в промковш или кристаллизатор и создают дополнительные центры кристаллизации чем обеспечивают получение лучшей макро и микроструктуры, измельчение неметаллических включений и повышение механических свойств металла;
- в настоящее время также активно изучается возможность плазменного подогрева металла в промежуточном ковше, что позволит снизить температуру перегрева металла на 20°С, и уменьшить структурную и химическую неоднородность.
Источник: Скляр В. О. Инновационные и ресурсосберегающие технологии в металлургии. Учебное пособие. – Донецк.: ДонНТУ, 2014. – 224 с.