Темпы увеличения производства металлических порошков во многом определяются использованием дешевых и простых методов их получения. Существуют различные способы получения порошков цветных металлов (табл. 1.1).
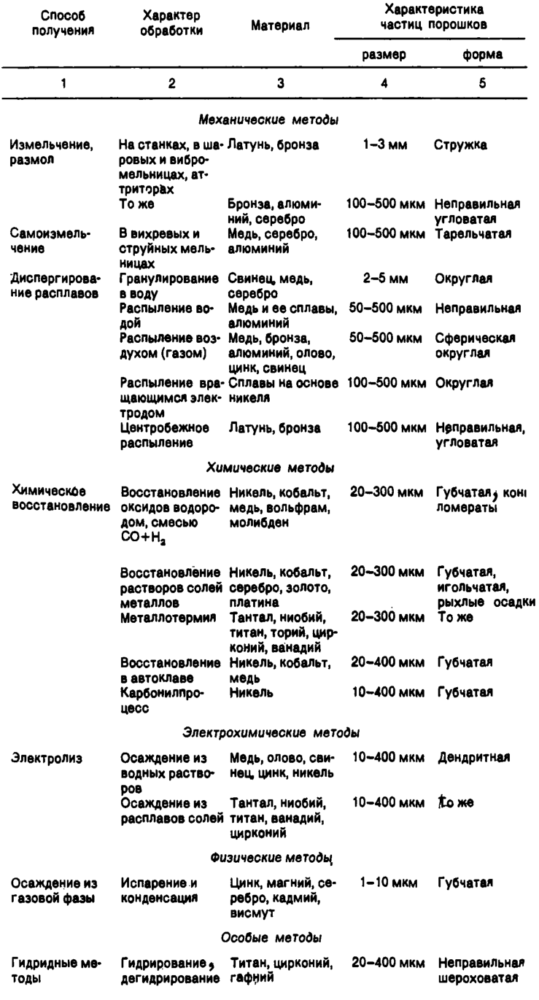
Наиболее широко внедрены в промышленность методы распыления и электролиза, поскольку именно эти методы используют для крупнотоннажного производства порошков меди и ее сплавов, алюминия, цинка, свинца и олова.
По масштабам использования в мировом производстве второе место (после железа) занимают порошки меди и ее сплавов, из которых изготовляют детали электротехнического, антифрикционного, конструкционного назначения, изделия для других специальных целей. Часть этих порошков производят электролизом растворов и распылением расплавов, часть – гидрометаллургическими методами и восстановлением оксидов газами. Традиционный метод – электролиз – обеспечивает получение дендритных порошков высокой чистоты с низкой насыпной массой. Широкий спектр свойств порошков меди (табл. 1.2) позволяет применять ее в различных отраслях техники.
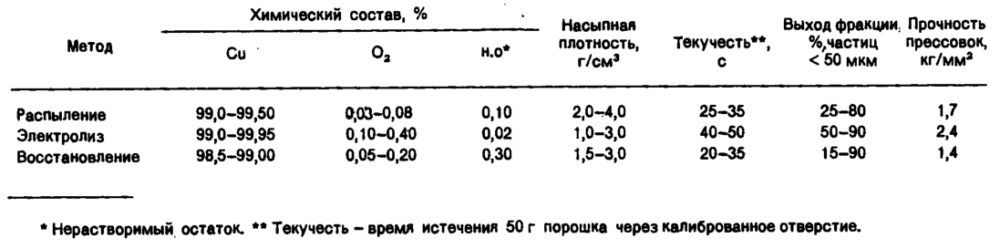
По данным фирмы “Дейви Лэви” (Англия), распыление расплавов меди водой является наиболее дешевым методом и обеспечивает высокое качество порошка. Распылением расплавов меди и бронзы воздухом получают сферические порошки, используемые для производства проницаемых материалов, фильтров. Метод распыления является единственно возможным для производства порошков сплавов на основе меди. Алюминиевые порошки по масштабам производства следуют непосредственно за порошками меди.
Промышленностью выпускается более 20 наименований порошковой продукции: алюминиевые порошки, пудры и пасты, гранулы из алюминиевого порошка (табл. 1.3). Распылением производят порошки и гранулы, остальную продукцию – механическим измельчением.
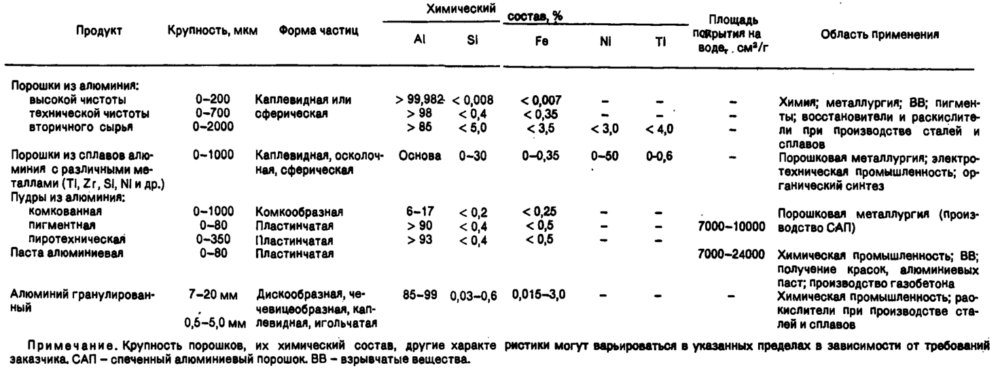
Для алюминиевых порошков характерны хорошая формуемость и спекаемость, высокая прочность получаемых изделий, их хорошая коррозионная стойкость.
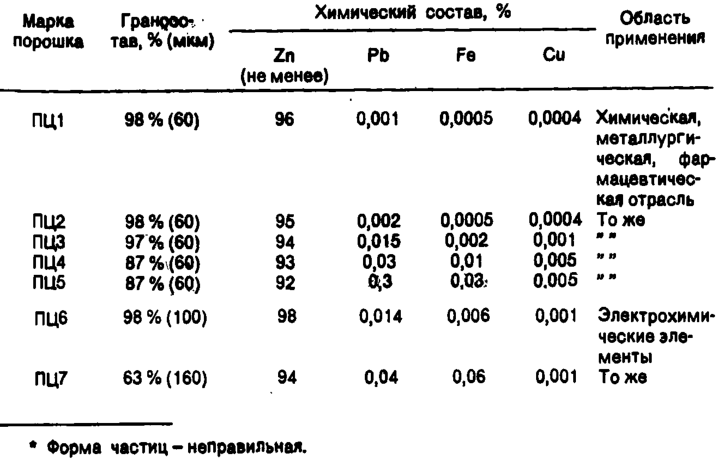
По объемам выпуска далее следуют порошки цинка, олова и свинца, которые также изготовляют методами распыления. Во всех случаях для производства этих порошков применяют распыление расплава воздухом. Для олова – нагретым до температуры 300-325 °С, для расплавов цинка и свинца – холодным. Основные характеристики порошков приведены в табл. 1.4-1.6.
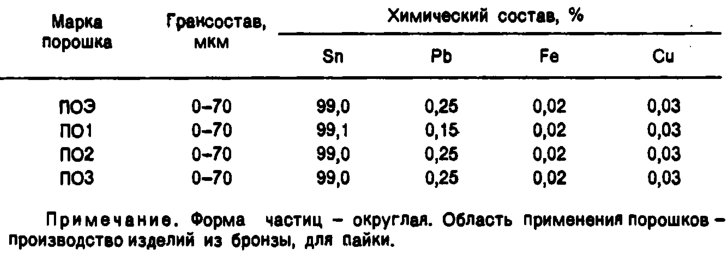
Разработаны новые способы получения порошков цветных металлов: осаждение из газовой фазы, распыление оплавляемого электрода, распыление с применением ультразвука. Значительное внимание уделяется методам очистки порошков от кислорода и углерода, управлению формой частиц, их размерами.
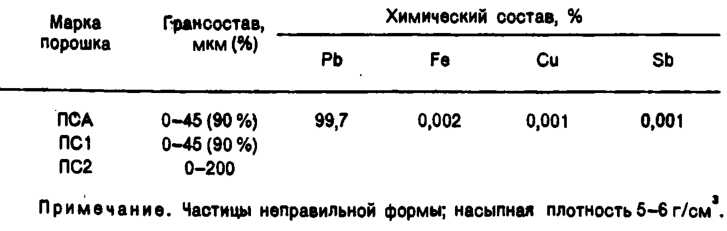
Общие сведения о свойствах порошков, методы их контроля
Порошки – это совокупность находящихся в контакте твердых тел с малыми размерами. Диапазон размеров частиц порошков условно делится на шесть классов:
- атомный класс менее 10-3 мкм;
- ультрадисперсные порошок 10-3 — 10-1 мкм;
- тонкодисперсные порошки 10-1 — 10 мкм;
- среднедисперсные порошки 10 — 102 мкм;
- технические порошки 102 — 5·102 мкм;
- грубодисперсные порошки 5·102 — 103 мкм.
Свыше 1000 мкм — гранулы. Наиболее существенным отличием порошков от компактных материалов является наличие у порошков избыточной поверхностной энергии, что является следствием развитой поверхности порошковых систем.
Удельная поверхность порошка связана с диаметром сферических частиц следующим выражением
S = 10 -4/γkd,
где S – удельная поверхность, м2/г; γк – плотность компактного материала, г/см3; d – диаметр частиц, см.
Избыточная поверхностная энергия в этом случае равна ΔG:
ΔG = Sσт,
где σт – поверхностная энергия твердого тела.
Для порошковых систем важное значение имеет капиллярное (лапласово) давление (р2), возникающее на поверхностях, обладающих кривизной:
где r1 и r2 – главные радиусы кривизны. Приняв для шарообразных частиц р2 = 2σт/r и σт= 2 Дж/м2, получим, соответственно, для радиусов 102; 10°; 10-2 мкм значения лапласовых давлений, равные 4·10-2; 4; 4·102 МПа, т.е. уже в случае ультрадисперсных порошков лапласово давление достаточно велико, что сказывается на условиях обработки таких порошков.