Планирование конвертерного производства предполагает установление массы садки и определение количества шихтовых материалов на плавку, расчеты времени действия конвертеров в планируемом периоде, их производительности, построение производственной программы.
Массу садки устанавливают, исходя из объема конвертера, фактической емкости и кратности ее массе отливаемых слитков. Так, при объемах конвертеров 90 и 170 м3 фактическая их емкость (по шихте) составит соответственно 130 и 250 т.
Расходные коэффициенты, а в дальнейшем и потребность в материалах на плавку устанавливают на основании расчета баланса металла плавки. В таблице 1 приведен примерный баланс выплавки кипящего металла в конвертере номинальной емкостью 130 т.
Важную роль в планировании экстенсивного использования конвертеров играет обоснованное определение продолжительности времени их действия в плановом периоде. Наличие двусторонних технологических и организационных связей с доменным и прокатными цехами обусловливает непрерывный режим работы конвертерных цехов с периодическими последовательными остановками конвертеров на текущие и капитальные ремонты.
Планирование сроков и продолжительности проведения капитальных ремонтов должно быть увязано с графиком работы потребляющих конвертерную сталь прокатных цехов.
Таблица 1. Баланс металла плавки
В соответствии с временным положением о ТОиР конвертеры с кислородным дутьем емкостью 100—250 т на протяжении года останавливаются на текущий ремонт через каждые 20 сут на 96 ч (четверо суток). Капитальный ремонт осуществляется один раз в два года, его общая продолжительность 288 часов (12сут).
За единицу времени работы конвертера приняты номинальные сутки. Номинальное время работы конвертеров в планируемом периоде определяют вычитанием из календарного времени продолжительности капитального
и плановых текущих ремонтов. Фактическое время работы рассчитывают путем вычитания из номинального времени продолжительности текущих простоев. Последние включают время ремонтов каминов, кессонов, механического и электрического оборудования, на смену кислородоподводящих фурм, простои по различным технологическим и техническим причинам. Общая продолжительность текущих простоев составляет 6—8 % от номинального времени. В зависимости от конкретных условий того или иного цеха и организации процесса каждый конвертер может еще находиться в резерве (5—6 % от номинального времени). Величина текущих простоев на ремонтах и резерв устанавливаются на основе отчетных данных о простоях и их причинах, принятой системе организации работы конвертеров, стойкости их футеровки. Если, например, на время ремонта конвертер заменяется резервным, то текущий простой конвертера на ремонте футеровки не планируется, а учитывается только время, затрачиваемое на замену конвертеров (обычно 2 часа ).
Величину текущих простоев, связанных с заменой конвертеров, можно рассчитать по формуле:
где d— длительность замены конвертера, мин; t — продолжительность плавки, мин; S — стойкость футеровки, плавки.
Если допустить, что (d= 120 мин, t = 40 мин, S = 500 плавок), то текущие простои на замене конвертера составляет 0,3 % от номинального времени.
Изыскание резервов увеличения продолжительности времени действия конвертеров должно быть направлено на повышение стойкости футеровки, обеспечивающее уменьшение числа текущих ремонтов, сокращение продолжительности ремонтов вследствие рациональной организации и механизации работ, сведение к минимуму простоев по причинам организационно-технических неполадок, ликвидацию межплавочных (так называемых скрытых) простоев.
Весьма важным направлением повышения степени экстенсивности использования конвертеров является увеличение стойкости их футеровки. Последняя зависит от многих технико-технологических факторов: качества огнеупоров, химического состава чугуна, режима и качества дутья, качества ремонтов и др.
Наряду с перечисленными серьезное влияние оказывают и такие организационно-технические факторы, как продолжительность перерывов между продувками, количество продувок, длительность межплавочных и внутриплавочных простоев.
Одним из наиболее эффективных методов повышения стойкости футеровки является так называемое циклонно-факельное торкретирование. Этот процесс принципиально нового типа, не имеющий аналогов за рубежом, представляет собой покрытие с помощью специальной установки футеровки конвертера огнеупорным порошком, нагретым в факеле высокой тепловой мощности при температуре 1700—1900°С.
Циклонно-факельное торкретирование обеспечивает повышение стойкости футеровки на 200 и более плавок за кампанию.
Для определения количественного влияния указанных факторов на стойкость футеровки применяют методы математической статистики — корреляционный и регрессионный анализ.
Выплавку стали рассчитывают по каждому конвертеру. Важнейшими результатами расчета являются годовая (квартальная) выплавка стали, суточная производительность, съем стали с 1 т номинальной емкости конвертера в номинальные сутки.
На основе квартальной программы составляются месячные оперативные планы производства, которые затем детализируют в виде недельных и суточно-сменных планов-графиков работы каждого конвертера. В планах-графиках с учетом заказанных марок стали и сроков выполнения и устанавливаются конкретные производственные задания по всем сталеплавильным агрегатам и цеху в целом.
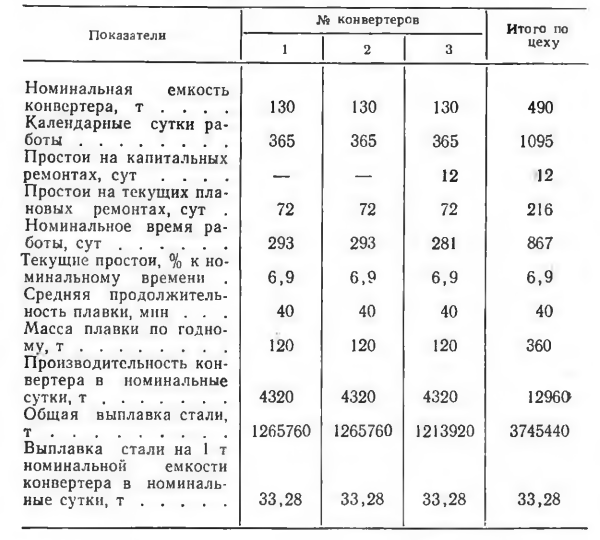
Примерный расчет выплавки стали на год по кислородно-конвертерному цеху представлен в таблице 2.