Способы прямого восстановления железа, характеристика продукции и сырья
Под процессами прямого восстановления железа понимают такие процессы, которые дают возможность получать непосредственно из руды металлическое железо, минуя доменную печь. Способы прямого получения железа позволяют вести процесс не расходуя металлургический кокс, заменяя его другими видами топлива.
Известно, что использование железа прямого восстановления при выплавке стали (в основном, в электродуговых печах) позволяет производить наиболее высококачественный, экономически выгодный (с относительно низкой энергоемкостью) и экологически чистый металл без примесей серы и фосфора, пригодный для удовлетворения самых высоких требований таких отраслей-потребителей, как машиностроение (авиа-, судостроение и т. д.). В настоящее время предложено более 20 различных способов прямого получения железа.
Железо прямого восстановления (или губчатое железо) в основном производят в виде металлизированных окатышей: холодных СDRI (Сool Direct Reduced Iron) или горячих HDRI (Hot Direct Reduced Iron), а также горячебрикетированного железа НBI (Hot Briquetted Iron).
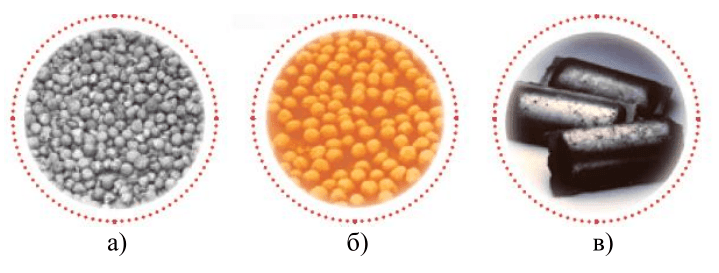
Окатыши СDRI (рис. 38 а) получают в основном в шахтных печах с охлаждением в нижней части печи до 50º С, после чего отравляются на склад, а затем загружаются в электропечь.
Окатыши HDRI (рис. 38 б) выгружаются из установки прямого восстановления в горячем состоянии и загружаются в расположенную рядом электропечь при температуре 600º С и выше.
Горячебрикетированное железо НBI (рис. 38 в) получается путем прессования брикетов размерами 30×50×110 мм в формы в виде подушек из металлизированного продукта, который выгружается из печи при температуре около 700º С.
Наибольшее распространение получили технологии компании Midrex (США). Процесс протекает в шахтной печи, в верхнюю часть которой подаются окатыши или кусковая руда. Установки Midrex действуют на многих предприятиях крупнейшей металлургической компании ArcelorMittal, расположенных в Германии, Канаде, Мексике, Тринидаде и Тобаго и ЮАР.
Второй по распространенности технологией прямого восстановления железа является HYL/Energiron. Процесс HYL был разработан мексиканской компанией Tenova для прямого восстановления железной руды (кусковой или окатышей) в металлическое железо с помощью восстановительного газа в реакторе с подвижным слоем.
Менее известна технология Finmet, которая позволяет использовать железорудную мелочь без предварительного окускования в процессе газового восстановления в кипящем (псевдосжиженном) слое. По этой технологии пока действует только одно предприятие – Orinoco Iron в Венесуэле.
Для получения железа прямого восстановления также применяется целый ряд угольных технологий – SL/RN, Jindal, DRC, SIIL, Tisco, Codir и др. В основном все они действуют на базе печей с вращающимся подом с использованием угля или пылеугольной смеси.
Такие предприятия работают в Индии, а также в ЮАР, Китае, Перу и в некоторых других странах. Хотя экологичность таких производств и качество получаемого металла существенно ниже, чем у «газовых» предприятий, однако они дешевле, что и обеспечивает им значительную долю в структуре мирового производства DRI.
Существуют также жидкофазные способы прямого восстановления и альтернативные доменной печи установки для получения чугуна.

Структура производства железа прямого восстановления в мире в последние годы приведена на рис. 39.
Производство железа в шахтных печах (технология Midrex)
В шахтных печах получают губчатое железо газообразными восстановителями в толстом слое железосодержащих окатышей. Схема производства различных видов железа прямого восстановления с использованием шахтной печи приведена на рис. 40.
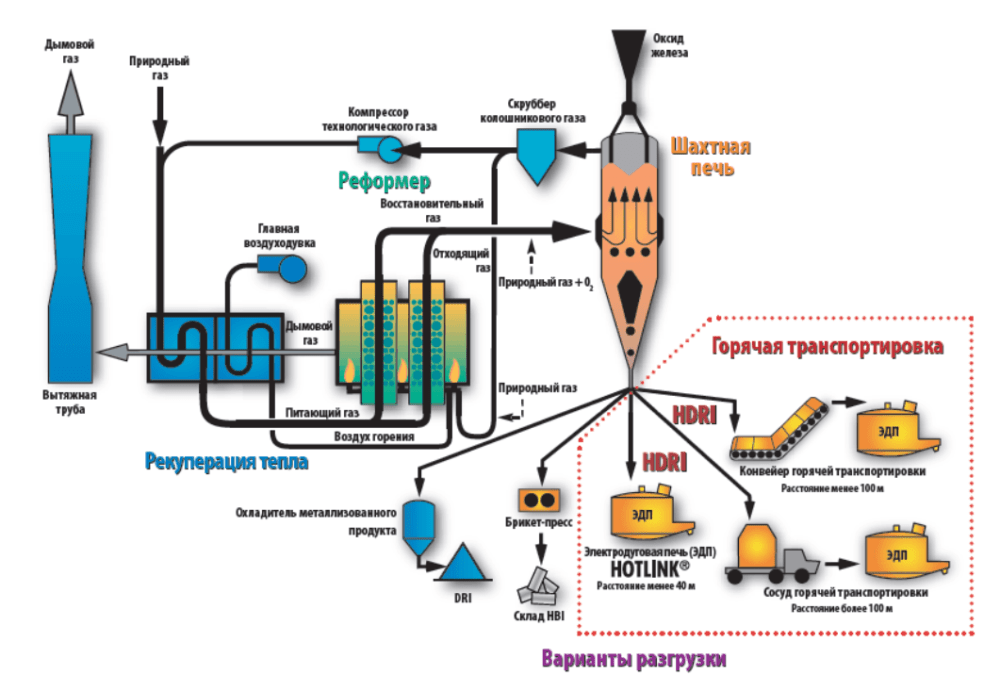
Процесс производства железа осуществляют в противотоке железорудных материалов, загружаемых в агрегат сверху, и нагретых восстановительных газов, подаваемых снизу. Работа агрегата в противотоке дает возможность достигать высокой производительности при хорошем использовании газа.
В качестве восстановителей применяют конвертированный природный газ, состоящий в основном из водорода (H2) и оксида углерода (CO). Восстановительный газ получают в кислородном реакторе (реформере), путем неполного сжигания природного газа в кислороде. Полученный газ, содержащий 29% CO, 55% H2 и 13% окислителей (H2O и CO2) освобождают частично от окислителей, затем нагревают, до температуры 1100…1150 °С и через фурмы подают в печь.
Добытую руду обогащают и получают окатыши. Окатыши из бункера загружают в шахтную печь, работающую по принципу противотока. Для восстановления железа из окатышей в среднюю часть печи по трубопроводу подают конвертированный природный газ. В восстановительной зоне печи создается температура 1000…1100 °C, при которой H2 и CO восстанавливают железную руду в окатышах до твёрдого губчатого железа. Содержание железа в окатышах достигает 90…95%. Для охлаждения железных окатышей, снизу печи в зону охлаждения печи подают воздух. Охлаждённые окатыши выдаются на конвейер и поступают на выплавку стали в электропечах. Если производятся горячие окатыши или горячебрикетированное железо, то охлаждение восстановленного железа в нижней зоне печи не производится.
Производство железа в периодически действующих ретортах (технология HYL/Energiron)
Еще одним способом производства железа прямого восстановления является процесс в периодически действующих ретортах, используемых в качестве агрегатов восстановления. На установке таких реторт четыре (рис. 41). Емкость каждой реторты 100…150 т.
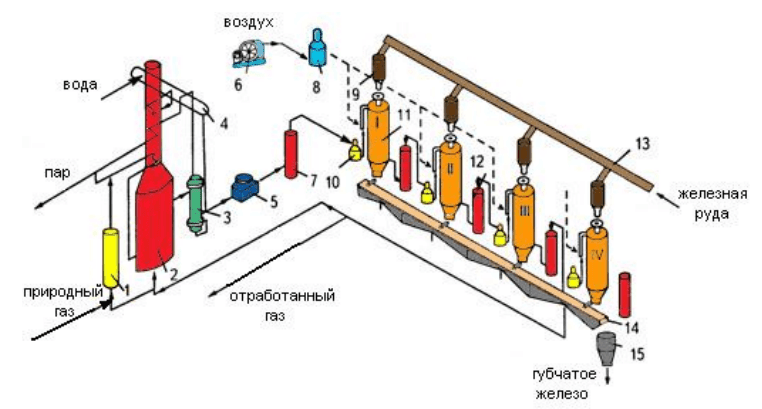
барабан для производства пара; 5 – воздушный охладитель; 6 – воздуходувка; 7 – скруббер; 8 – воздухонагреватель; 9 – загрузочный бункер; 10 – нагреватель газа; 11 – реторты (I – IV); 12 – скруббер; 13 – конвейер подачи руды; 14 – конвейер уборки губчатого железа; 15 – сборный бункер губчатого железа
Реторты переставляются с одной позиции на другую, что обуславливает циклический характер процесса, состоящего из последовательных операций загрузки, нагрева и восстановления шихты, охлаждения и выгрузки губчатого железа. Реторты загружают и подают газ сверху. В качестве сырья используют чистые руды, содержащие не менее 60 % железа, крупностью 12…50 мм.
Восстановление ведется в неподвижном слое кусковой руды или окатышей при избыточном давлении 0,35…0,4 МПа и температуре 870…1040 °С. Нагрев руды и компенсация тепловых потерь процесса осуществляют за счет физического тепла восстановительного газа, который нагревают до 980…1240 ºС. При выдержке 4…6 часов средняя степень металлизации железа составляет 85 %. Выгрузку губчатого железа производят снизу с помощью специальных скребков. Губчатое железо поступает на конвейер транспортирующий губку в сталеплавильное отделение. На рис. 42 показана схема стационарной реторты со съемной крышкой и откидным днищем.
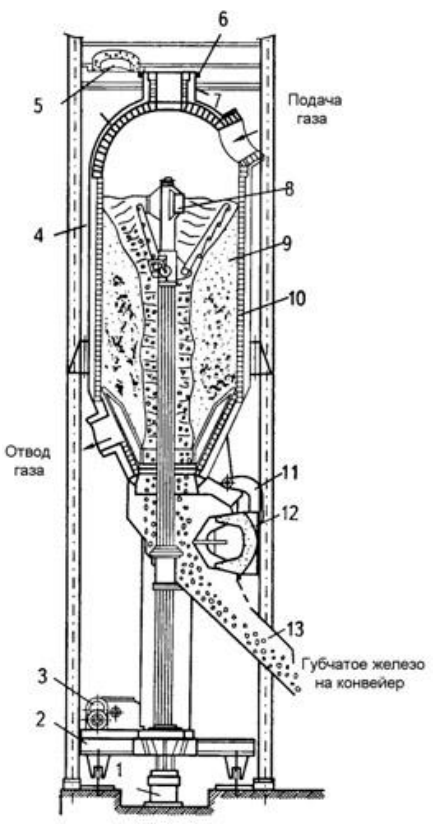
горловина; 7 – площадка для обслуживания; 8 – резец с рычагом
для удаления губчатого железа; 9 – губчатое железо; 10 – футеровка; 11 – механизм управления откидным днищем; 12 – откидное днище; 13 – разгрузочный желоб
В каждой из четырех реторт протекают различные процессы. В одной реторте происходит предварительный нагрев и восстановление шихты газом, выходящим из других реторт. В двух ретортах происходит довосстановление железа подогретым газом, получаемым в конверсионной установке. В четвертой происходит науглероживание губчатого железа. Готовое железо поступает на конвейер, а в освобожденную реторту загружают исходную шихту.
К недостаткам метода относят:
- периодичность процесса;
- неравномерность металлизации по высоте;
- низкая степень металлизации в сравнении с процессами, осуществляемыми в шахтных печах.
Производство железа на движущейся колосниковой решетке
Процесс получения железа на движущейся колосниковой решетке (рис. 43) несколько напоминает работу агломерационной машины. В этом случае конвертируемый газ проходит сверху вниз через слой шихты.
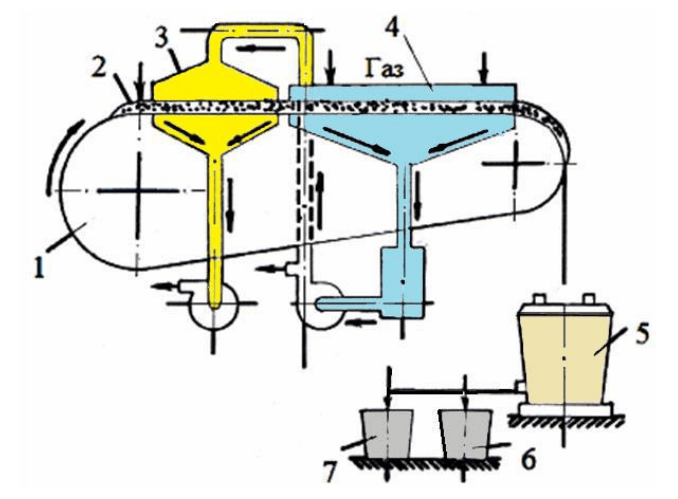
Существует разновидность процесса получения железа на движущейся колосниковой решетке, когда вместо конвертированного газа используют твердый восстановитель (каменный уголь, кокс и т.д.).
В этом случае сырые окатыши в головной части установки сушат рециркулируемыми газами, после чего окатыши поступают в зону обжига, где в результате просасывания горячих газов происходит нагрев и восстановление оксидов железа. Основным преимуществом этого процесса является возможность подавать в установку для восстановления неупрочненные обжигом окатыши. Недостатком этого процесса является загрязнение губчатого железа пустой породой, серой и фосфором твердого топлива.
Производство железа во вращающихся трубчатых печах
Другой разновидностью процесса с использованием твердого восстановителя является способ получения железа во вращающихся трубчатых печах (рис. 44).
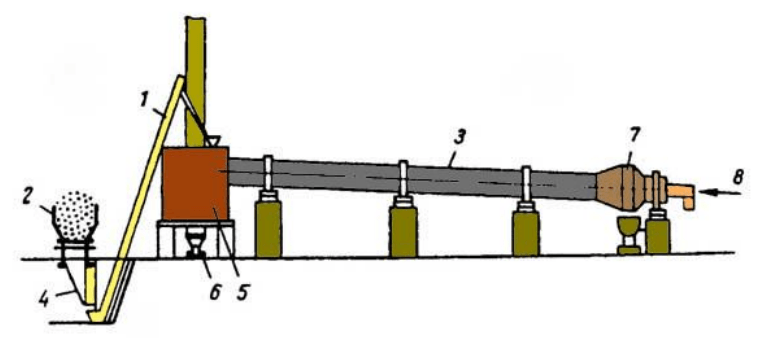
По этому способу во вращающуюся трубчатую печь, установленную под небольшим углом к горизонту, загружается шихта, состоящая из руды, твердого топлива и доломита или известняка. Доломит и известняк используются для десульфурации. Печь отапливается газообразным или жидким топливом при помощи горелок, установленных на разгрузочном конце печи.
По мере продвижения шихты от загрузочного конца печи к разгрузочному, навстречу газообразным продуктам горения, происходит восстановление оксидов железа. Восстановление протекает в основном через газовую фазу при участии твердого углерода. На разгрузочном конце печи восстановленный материал для предупреждения окисления охлаждается в специальном вращающемся охладителе и после дробления и последующего магнитного обогащения используется в сталеплавильном производстве.
Производство железа в реакторах кипящего слоя
В основу этого способа положен эффект так называемого кипящего слоя, при котором создаются условия для хорошего контакта мелких железорудных материалов с газообразным восстановителем.
Сущность явления кипящего слоя заключается в следующем. Если через слой зернистого материала пропускать восходящий поток газа, то при небольших скоростях газа твердые частицы будут оставаться неподвижными. Слой будет выполнять роль фильтрующего пористого элемента.
Для создания кипящего слоя под горизонтальную решетку реактора, на которую загружают исходный железорудный материал, подается горячий восстановительный газ с определенной скоростью.
Чтобы предотвратить спекание восстановленного железа процесс ведется при низкой температуре (около 500 °С). Железо полученное при этой температуре, характеризуется повышенной пирофорностью (самовозгораемостью на воздухе). Для предотвращения пирофорности полученное железо нагревают до 820…880 °С с последующим охлаждением в восстановительной или нейтральной атмосфере.
Агрегаты FASTMET и ITmk3
В данных агрегатах осуществляется получение железа из руды и некосующегося угля. В агрегатах FASTMET также могут утилизироваться побочные продукты (пыли и шламы), содержащие железо, которые образуются на заводах с полным металлургическим циклом. Развитие этой технологии привело к созданию в 1996 г. процесса ITmk3 производства «передельного чугуна высшего качества» из окатышей или брикетов, схема процессов приведена на рис. 45.
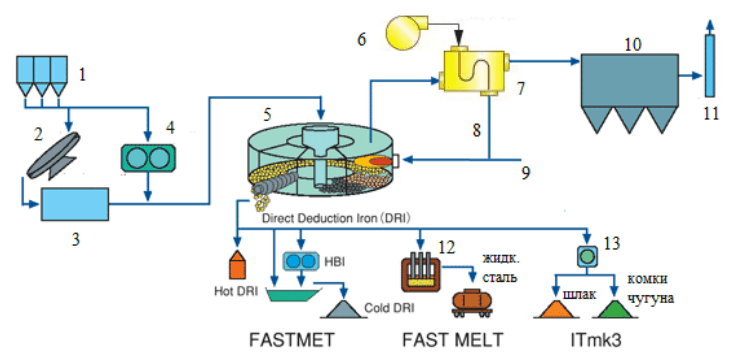
сушка; 4 – брикетирование; 5 – печь с вращающимся подом; 6 – компрессор; 7 – регенератор; 8 – воздух для горелки; 9 – топливо для горелки; 10 – газоочистка; 11 – дымовая труба; 12 – электросталеплавильная печь; 13 – сепаратор
Технология получения железа следующая. Из мелкой железной руды после ее смешивания с углем получают гранулы, которые высушивают и загружают в печь с вращающимся подом. Процесс по существу выполняется на большом поворотном столе, который вращается в пределах тороидального огражденного пространства.
Гранулы из шихты загружаются на вращающийся под печи одним или двумя слоями и во время вращения нагреваются горелками, расположенными над слоем, где также происходит дожигание оксида углерода и летучих угля, выделяющихся при нагреве и восстановлении оксидов. Один оборот вращающейся печи осуществляется за 10 мин.
В случае процесса FASTMET продукцией является губчатое железо, FASTMELT – жидкая сталь, а в процессе ITmk3 данные комки плавятся в последней зоне этого пода, тем самым получая гранулы чугуна и шлак. Конечным этапом является разделение чугунных комков и шлака.
Химико-термический способ получения железа
Данный метод применяется для получения очень чистого железа из труднообогатимого рудного сырья, содержащего большое количество вредных примесей. Он может быть использован также для получения легированной железной губки из комплексных руд.
Схема технологического процесса получения железа по этому методу включает следующие операции (рис. 46).
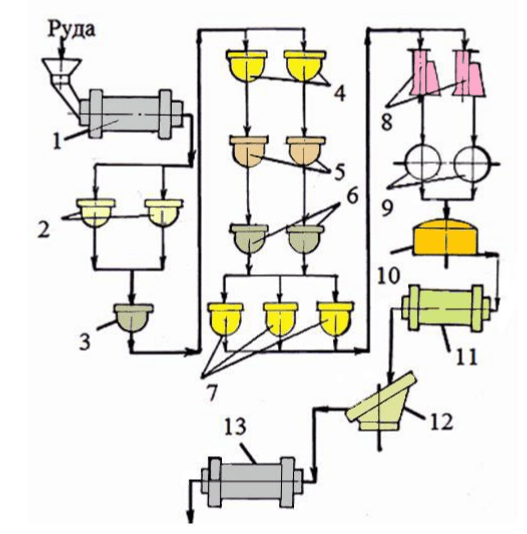
Усредненная на рудном дворе руда поступает в дробильное отделение, а затем в печь обжига. Для ускорения процесса обжиг руды проводится с использованием твердого восстановителя. Для этого приёмные бункеры мельниц оборудуются дозаторами для приготовления шихты, состоящей из руды и твердого восстановителя.
Подготовленная шихта поставляется в печь для восстановительного обжига. Обжиг проводится при температуре 900…1000 °С. После обжига руда поступает в реакторы растворения руды, заполненные соляной кислотой. Начальная стадия растворения происходит очень бурно и сопровождается выделением водорода. По мере снижения концентрации кислоты и сокращения поверхности твердой фазы скорость реакции растворения падает. Для ускорения процесса на конечном этапе реакционный объём подогревается паром с температурой 80…90 °С, подаваемом в паровые рубашки реакторов.
Выделяющийся при растворении водород после очистки направляется в печь восстановления хлоридов, где используется как газообразный восстановитель. Пары соляной кислоты, сконденсировавшиеся в процессе растворения, поступают в систему сбора кислоты, откуда направляются в реактор растворения.
Полученная в результате растворения пульпа подаётся в фильтры для отделения раствора от нерастворимого остатка. Отфильтрованный раствор поступает в выпарные аппараты, где проводится выпаривание до насыщения по хлористому железу. Далее раствор направляется в кристаллизаторы, из которых смесь кристаллов и раствора подается на центрифуги. Из центрифуг кристаллы направляются в печь сушки и затем в печь восстановления хлоридов, отапливающуюся природным газом.
Для восстановления хлоридов используется водород. Температура восстановления составляет 600…700 °С. В результате, после восстановления, образуется химически чистое железо.
Отходящий из печей газ, содержащий водород и пары воды, подвергается осушке, очистке и используется как восстановитель при восстановлении хлоридов. Кислота, образующаяся в результате охлаждения и очистки отходящих газов, поступает в систему сбора соляной кислоты, откуда направляется в реакторы растворения руды.
Таким образом, процесс построен максимально рационально, поскольку обеспечивается рециркуляция всех реагентов, участвующих в процессе.
Источник: Скляр В. О. Инновационные и ресурсосберегающие технологии в металлургии. Учебное пособие. – Донецк.: ДонНТУ, 2014. – 224 с.