Теплоэнергетика в производстве чугуна
Доменное производство является наиболее крупным потребителем энергоресурсов. Здесь расходуется около 50% топлива, потребляемого отраслью.
Процесс плавки в доменной печи является энергетическим процессом: кокс, горячее дутьё, кислород в дутьё; природный газ, мазут, пылеугольное топливо (ПУТ) используют как заменители кокса. Кокс выполняет функции топлива и восстановителя. Стоимость кокса составляет 40…50% себестоимости чугуна. Поэтому снижение расхода кокса или замена его более дешёвым топливом эффективны.
На экономию кокса оказывают влияние многие технологические и энергетические факторы. Так, например, повышение температуры дутья на 100°С сверх 900°С приводит к снижению расхода кокса на 2…4%.
Расход дутья определяет производительность печи и её тепловую мощность. Однако увеличение расхода дутья лимитируется некоторыми технологическими и эксплуатационными факторами. Расход дутья выше определённого значения для данной печи может привести к нарушению ровного хода печи и нормального движения шихтовых материалов.
В настоящее время на 1 м3 полезного объёма вдувается ~2 м3/мин воздуха. Для подачи воздуха в печь применяют центробежные турбовоздуходувки. В качестве привода воздуходувок используют паровые турбины, работающие на паре с давлением от 3,5 до 9 МПа.
Нагрев дутья для доменной печи осуществляется в воздухонагревателях регенеративного типа. Отапливаются водонагреватели в основном доменным газом с добавками коксового и природного газа. В современных печах температура дутья достигает 1100…1300°С. С целью уменьшения размеров воздухонагревателей и более эффективного использования их рабочего объёма применяют насадки с развитой поверхностью теплообмена.
Интенсификация доменного процесса в значительной степени достигается применением дополнительных, кроме кокса и горячего дутья, энергоносителей. Обогащение дутья кислородом – один из эффективных методов интенсификации доменной плавки. С увеличением содержания кислорода в дутье снижается содержание азота, уменьшается расход дутья, растёт теоретическая температура горения. На действующих заводах содержание кислорода в дутье достигает 25…30%.
Вторичные энергоресурсы доменного производства
Источниками вторичных энергоресурсов являются: топливные – доменный газ и тепловые ВЭР – физическое тепло чугуна, шлака, доменного газа, тепло охлаждающей среды. Эти статьи превышают 65% тепла, внесенного в доменную печь.
Ко вторичным энергоресурсам доменного производства относятся также тепло уходящих газов воздухонагревателей, составляющее 15…20% от расхода тепла на подогрев дутья. Для использования тепла отходящих газов воздухонагревателей доменных печей разработана установка-теплообменник, в которой нагревается воздух и доменный газ, подаваемые в горелки воздухонагревателя, до 200…300°С. Физическое тепло доменного газа зачастую не используется, т. к. после применяемой мокрой газоочистки газ поступает при низкой температуре. Тепло охлаждения печи может быть использовано при замене водяного охлаждения испарительным. Коэффициент использования тепловых ВЭР доменного производства составляет в среднем 30%.
Доменный газ представляет собой дешевое топливо с теплотой сгорания Qнр = 3,5…4,5 МДж/м3. В составе газа содержатся горючие компоненты СО=24-28%, Н2=2-3% , СН4≈0,1% и негорючие СО2=10-12%, N2=54-56%, Н2О=3-4%. Выход газа зависит от многих факторов: качества и подготовки сырья, расхода кокса, температуры дутья, концентрации кислорода в дутье, вдувание заменителей кокса и др. Чем ниже расход кокса, тем меньше выход газа. С увеличением доли кислорода и заменителей газа в дутье выход доменного газа снижается.
Состав доменного газа и его теплота сгорания также переменны, как и выход его. И здесь решающее влияние оказывают интенсификаторы плавки. Повышение температуры дутья способствует некоторому снижению теплоты сгорания. При вдувании природного газа теплота сгорания несколько повышается. Обогащение дутья кислородом сопровождается увеличением содержания в доменном газе СО и Н2 и повышением, следовательно, теплоты сгорания доменного газа.
Повышение давления на колошнике позволяет увеличить производительность доменной печи за счёт увеличения массового расхода дутья. При повышении давления газа на колошнике остаются резервы давления газа, которые можно использовать в газовой турбине, для обеспечения электроэнергией потребностей доменного цеха. Себестоимость электроэнергии, полученной на таких установках в 3 раза меньше, чем электроэнергии от центральной энергосистемы.
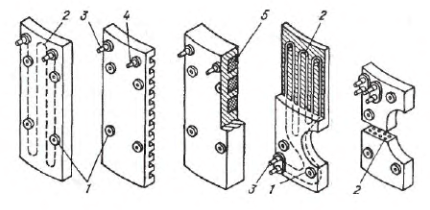
Значительная часть футеровки доменной печи охлаждается при помощи специальных холодильников, назначение которых заключается в отводе некоторого количества тепла для стабилизации теплового состояния футеровки, кожуха и его опорных элементов и соответственно продления срока их службы. Различаются водяные и испарительные системы охлаждения. Первые характеризуются повышенными расходами охладителя. Для вторых к показателям качества воды предъявляются повышенные требования. Схемы некоторых видов холодильников для элементов конструкций доменных печей представлены на рис. 1.9.
Теплоэнергетика в производстве и разливке стали
Несмотря на то, что в мировой практике доля мартеновской стали крайне мала, на украинских металлургических предприятиях до половины производимой стали выплавляется в мартеновских печах.
Топливом для мартеновских печей служат доменный, коксовый, природный газы и мазут, а также смеси этих топлив. Большинство печей сейчас отапливается природным газом.
Лучшие технико-экономические показатели работы печей получены при использовании природного газа с добавкой 20…30% мазута.
Мазут как самостоятельное топливо применяют значительно реже, чем как добавочное к природному газу. На чистом мазуте выплавляется 10% стали.
Воздух, необходимый для горения, подогревается предварительно в регенераторах до 1200…1250°С.
Кислород применяется в мартеновском производстве как мощный интенсификатор. Большая часть выплавляемой в настоящее время мартеновской стали выплавляется с применением кислорода.
Для повышения температуры, улучшения организации факела применяют подачу в факел технического кислорода при давлении 1,0 – 1,2 МПа. Подача кислорода в факел увеличивает производительность печи, т. к. при этом повышается температура горения топлива.
В настоящее время факельный метод использования кислорода в чистом виде применяют редко. На большинстве крупных заводов применяется более эффективный метод – продувка жидкой ванны. Большая эффективность продувки кислородом по сравнению с обогащением факела объясняется следующими факторами: с одной стороны, при продувке кислородом резко увеличивается доля участия газообразного кислорода в окислении примесей ванны. С другой стороны, при кислородной продувке резко увеличивается интенсивность экзотермических реакций в ванне, термический КПД которых в 2…3 раза выше, чем реакций в факеле. В тоже время значительно увеличивается износ огнеупорной футеровки.
Практика передовых отечественных заводов подтвердила возможность повышения производительности печей на 20% и снижения расхода топлива на 10…17% при обогащении дутья до 25% кислородом.
Наиболее рациональный оказался комбинированный подвод кислорода: в факел и в ванну. При этом количество вдуваемого в факел кислорода в два раза больше, чем в ванну.
Особенности теплоэнергетики двухванных сталеплавильных агрегатов
Для увеличения мощности агрегата при минимальных капитальных затратах производят реконструкцию мартеновских печей в двухванные сталеплавильные агрегаты. В такой печи одна плавильная ванна заменена двумя ваннами, разделёнными между собой порогом в подине и пережимом в своде. В печи отсутствуют регенераторы. Двухванные печи следует рассматривать как временную конструкцию, соответствующую сложному (в техническом и экономическом отношении) полному переходу отечественной металлургии на конвертерный способ производства стали.
Процесс в двухванных печах по интенсивности приближается к конвертерному. Интенсификация процесса и экономия топлива достигается сдвигом во времени периодов плавки. При этом в первой «горячей» ванне по ходу газов идут периоды плавления и доводки с интенсивной продувкой кислородом, которые требуют большего подвода тепла и более высокой температуры. Во второй холодной ванне в это время идут процессы завалки и прогрева шихты за счёт догорания СО; сюда поступают газы, отдавшие уже часть тепла в горячей ванне. Недостающее тепло восполняется подачей природного газа через горелки, установленные в своде печи.
Технико-экономические показатели рабочих двухванных печей зависят от эффективности использования в них тепловой энергии. Источниками энергии в процессе являются: тепло сгорания топлива, физическое тепло чугуна, тепло окисления примесей металла, тепло окисления железа.
Холодная ванна частично выполняет роль регенератора, аккумулируя тепло газов, покидающих горячую часть с температурой 1700°С.
Количество уходящих газов из рабочего пространства печи составляет 50…60 тысяч м3/час их температура 1400…1500°С. Полная утилизация высокотемпературных газов осуществляется с установкой котлов утилизаторов специальной конструкции радиационно-конвективного тепла.
Теплоохлаждение конструкции печи осуществляется путём оборудования её испарительным охлаждением.
Теплоэнергетика кислородно-конвертерного производства
Сущность кислородно-конвертерного процесса заключается в продувке жидкого чугуна кислородом, вводимым через водоохлаждаемую фурму.
Процесс в конвертере – периодический. За один цикл чередуются два положения конвертера: вертикальное, при котором производится продувка и получение стали, и наклонное, при котором осуществляется выпуск стали и загрузка материалов для следующей плавки. Продолжительность плавки составляют 20…50 минут. Период продувки составляет 30…50% цикла.
Особенностью конвертерной плавки является получение в ней стали без использования топлива. Необходимое для процесса тепло вносится на 50% жидким чугуном и на 50%
экзотермическими реакциями технологического процесса.
Образующиеся в процессе плавки газы покидают конвертер через горловину. Основные составляющие этих газов: СО – до 90% и СО2 – 10%; теплота сгорания Qрн = 8-10 МДж/м3.
Температура конвертерных газов колеблется в пределах 1400 –1800 °С. Конвертерные газы охлаждают в охладителях до температуры 300°С. Габариты охлаждающих устройств значительно превышают габариты самого конвертера.
Газы отводят из конвертеров различными способами, которые отличаются в основном величиной коэффициента расхода воздуха на входе в охладитель:
- α > 1,0 – с доступом воздуха и полным дожиганием газов;
- 0
- α = 0 – без доступа воздуха и без дожигания газов.
Опыт работы установок по охлаждению конвертерных газов с дожиганием и использованием тепла для производства пара показал экономическую целесообразность их применения. Охладитель конвертерных газов за конвертером даёт выработку пара примерно в 10 раз больше, чем котёл утилизатор за большегрузной мартеновской печью. Опыт работы без дожигания привел к выводу о нецелесообразности из-за взрывоопасности, непостоянства состава и нестабильности подачи.
Теплоэнергетика производства стали в электродуговых печах
Дуговая электропечь – сталеплавильный агрегат, в котором основным источником энергии для нагрева шихтовых материалов и их плавления является энергия электрических дуг. Электрические дуги возникают между тремя электродами и жидким металлом или металлической шихтой. Дуговые электропечи являются мощными потребителями электроэнергии, поэтому для уменьшения потерь ее подают к печам под напряжением 6–110 кВ. Рабочее напряжение, подаваемое на электроды, должно быть в пределах 110–800 В, поэтому каждая печь имеет отдельный понижающий трансформатор и другое электрическое оборудование, обеспечивающие снижение напряжения до рабочего, подвод тока к электродам и регулирование подводимой электрической мощности.
Печной трансформатор предназначен для преобразования электрической энергии высокого напряжения в энергию низкого напряжения. Трехфазный печной трансформатор состоит из трех связанных между собой сердечников, на каждом из которых закреплены обмотки высокого и низкого напряжения. Сердечник с обмотками помещены в кожух, заполненный трансформаторным маслом, являющееся изолятором и охлаждающее трансформатор. В трансформаторах мощностью более 5 MBА применяют принудительную циркуляцию масла, которое пропускают через водяной маслоохладитель. У некоторых трансформаторов мощностью до 10 MBА в кожухе с маслом дополнительно размещен дроссель, а у многих высокомощных – переключатель ступеней напряжения, работающий под нагрузкой. Современной тенденцией является увеличение мощности печных трансформаторов (в настоящее время эта величина может достигать сотен МВА) с целью сокращения длительности плавки.
Электрическая дуга является основным источником тепла в дуговой сталеплавильной печи. Электрическая дуга или дуговой электрический разряд в газовой среде – это поток электронов и ионов между анодом и катодом. При приложении к последним напряжения достаточной величины происходит эмиссия электронов с катода, которые, соударяясь с молекулами газа в межэлектродном пространстве, вызывают их ионизацию; при этом положительно заряженные частицы движутся к катоду, а электроны к аноду, создавая дугу. Движущиеся к аноду электроны бомбардируют его, в результате чего кинетическая энергия электронов превращается в тепловую и световую энергию, аналогичный процесс идет на катоде, бомбардируемым положительно заряженными частицами; температура бомбардируемого пятна анода составляет 3600-4000 °С, катода 3200-3600 °С, а температура столба дуги достигает 6000°С.
В дуговой сталеплавильной печи дуга горит между электродами и металлом (жидкая ванна, нерасплавившаяся шихта) и представляет собой поток электронов, ионизированных газов и паров металла и шлака. Поскольку дуговые печи питаются переменным током, в течение каждого полупериода меняются катод и анод, а напряжение и сила тока дуги достигают максимума и проходят через ноль. Эмиссия электронов с катода существенно облегчается при повышении температуры катода, поэтому в дуговой печи после расплавления шихты дуга горит более устойчиво, чем в начале плавки при холодной шихте. Длина дуги на больших высокомощных печах может достигать 150–200 мм, сила тока 60–100 кА.
В электродуговых печах предусмотрено водяное охлаждение ряда элементов при помощи водяных холодильников.
В современных печах для интенсификации процессов нагрева и плавления шахты в свод печи вводятся газокислородные горелки, тепловая мощность которых может достигать 20-30 % от подводимой в печь электрической мощности.
Теплоэнергетика внепечной обработки стали
Ограниченные возможности регулирования физических и физико-химических условий протекания процессов плавки стали в сталеплавильных агрегатах, повышение требований к качеству стали, а также необходимость разработки технологии и производства стали принципиально нового качества привели к развитию технологий внепечной обработки стали.
Методы внепечной обработки стали могут быть условно разделены на простые (обработка одним способом) и комбинированные (обработка металла несколькими способами одновременно). К простым методам относятся:
- обработка металла вакуумом;
- продувка инертным газом;
- обработка металла синтетическим шлаком, жидкими и твёрдыми шлаковыми смесями;
- введение реагентов в глубь металла.
В мировой практике получает всё большее распространение процесс, названный процессом ковш-печь. В зарубежной литературе процесс получил наименование LF-процесс (Ladle-Furnace), в отечественной литературе часто используют аббревиатуру АКОС (агрегат комплексной обработки стали). Процесс включает в себя перемешивание путём продувки металла аргоном в ковше, дуговой подогрев и обработку металла синтетическим шлаком в процессе его перемешивания аргоном. Процесс обеспечивает не только получение металла заданного химического состава и температуры, но и снижение количества неметаллических включений в результате удаления серы и кислорода. Такой агрегат может быть установлен в любом сталеплавильном цехе.
Для реализации внепечной обработки стали необходимо использование следующих энергоносителей:
- электрическая энергия для подогрева расплава за счет тепла выделяющегося при горении электрических дуг;
- аргон для продувки металла и организации его перемешивания с целью выравнивания температурного поля, более полного усвоения реагентов, всплытия неметаллических включений и дегазации металла;
- кислород для продувки расплава в агрегатах доводки, предполагающих покрытие теплопотерь за счет некоторого окисления примесей расплава;
- пар или другие энергоносители, необходимые для работы вакууматоров.
Разливка стали
Жидкий металл принципиально может быть разлит двумя способами: в изложницу и на машине непрерывного литья заготовок (МНЛЗ).
Исторически вид разливки стали в изложницу возник первым. Его сущность состоит в заливке жидкой стали в специальную форму (изложницу) и затвердевания расплава. Различают разливку стали сверху и сифонную разливку. Каждый из методов имеет свои достоинства, которые определяют ряд технологических преимуществ, и недостатки, определяющие вероятность появления специфических дефектов. Масса слитков, отливаемых для прокатки, колеблется от 200кг до 30т. Масса слитков для поковок достигает 350 т. Слитки для кузнечных поковок разливают в многогранные изложницы. Основной проблемой при разливке стали в изложницы является высокая доля обрези перед прокаткой. Удалению перед прокаткой подлежат части слитка с серьезными дефектами макроструктуры (головная часть слитка из спокойной стали, содержащая усадочную раковину), а также характеризующиеся значительной химической неоднородностью (например, донная часть слитка). Для слитков из спокойной стали суммарная доля обрези может достигать 25-30%, что определяет низкие показатели ресурсоэнергосбережения таких технологий. Доля обрези на усадочную раковину может быть значительно уменьшена благодаря утеплению прибыльной надставки, использованию экзотермических засыпок или даже практически сведена к нулю при помощи метода электрошлаковой разливки стали. Эффективным способом разливки особо крупных кузнечных слитков является порционный метод электрошлаковой разливки.
Под непрерывной разливкой стали понимают систему операций, которые позволяют обеспечить квазинепрерывный переход жидкой стали в твердое состояние в виде заготовок заданной геометрической формы. При этом реализуется последовательная разливка определенного количества сталеразливочных ковшей, подаваемых от сталеплавильного агрегата. Получаемая заготовка разрезается на мерные длины. Выход годного составляет от 98,5 до 99,5% от исходной массы разливаемого металла. Агрегатом для реализации непрерывной разливки стали является машина непрерывного литья заготовок (МНЛЗ). В ряде работ для названия этих агрегатов иногда используется устаревшее понятие «установка непрерывной разливки стали» (УНРС). Основными технологическими участками МНЛЗ являются кристаллизатор и зона вторичного охлаждения (ЗВО). Кристаллизатор представляет собой конструктивный элемент, в который заливается жидкий металл и происходит образование твердой корочки по периметру сечения заготовки. Различают гильзовый кристаллизатор (для сортовых МНЛЗ) и сборный плитовый кристаллизатор (для слябовых МНЛЗ). Кристаллизаторы охлаждаются водой в оборотном цикле, рекомендуется чтобы повышение температуры воды при прохождении кристаллизатора не превышало 10°С, при этом расход воды на один кристаллизатор может достигать несколько сотен м3/ч. В зоне вторичного охлаждения тепло отводится от поверхности заготовки, орошаемой водой или водовоздушной смесью, распыливаемыми затвердевающего металла в результате омывания наружной поверхности гильзы или плит через специальные форсунки. Для гибкости регулирования интенсивности охлаждения по длине ЗВО ее разделяют на несколько секторов. Расход воды на сектора ЗВО принято измерять в л/мин и для одного сектора он может находиться в пределах 50-400 л/мин.
Стоимость тонны проката, полученного из непрерывнолитых заготовок, приблизительно на 28% ниже, чем слитков, отлитых в изложницу. Существенной является не только экономия металла, но и экономия энергии. Исключение обжимного цеха определяет снижение итоговых затрат топлива на нагрев, и сокращение расхода электроэнергии на прокатку. Также исключается тяжелый ручной труд по ремонту и обслуживанию парка изложниц.
В конце XX века доля стали, полученной непрерывным литьем, составила для стран ЕС – 96,4%, Японии – 97,2%, США – 95,6%. В целом для украинской металлургии доля стали, разлитой непрерывным способом составляет не более 50%.
Необходимо иметь в виду, что при разливке стали любым способом имеет место расход газообразного топлива на разогрев сталеразливочных ковшей, а при непрерывной разливке стали добавляется такая статья расхода как разогрев промежуточного ковша МНЛЗ.
Теплоэенергетика в производстве проката
Прокатное производство – это получение путём обработки давлением (прокатки) стали и других металлов в различных изделиях и полуфабрикатах, а также дополнительная обработка их с целью повышения качества (термическая обработка). К основным видам проката относятся: полупродукт, или заготовка (блюмы, слябы), листовой и сортовой прокат, катаные трубы, заготовки деталей машин, колёса, кольца, оси, свёрла, шары, профили переменного сечения и др.
Производство стального проката на современном металлургическом заводе осуществляется двумя способами. При первом исходным материалом служат слитки (отлитые в изложницы), которые перерабатываются в готовый прокат обычно в две стадии. Сначала слитки нагревают и прокатывают на обжимных станах в заготовку (блюмы, слябы). После производят повторный нагрев и прокатку готовой продукции на специализированных станах (рис. 1 .10а).
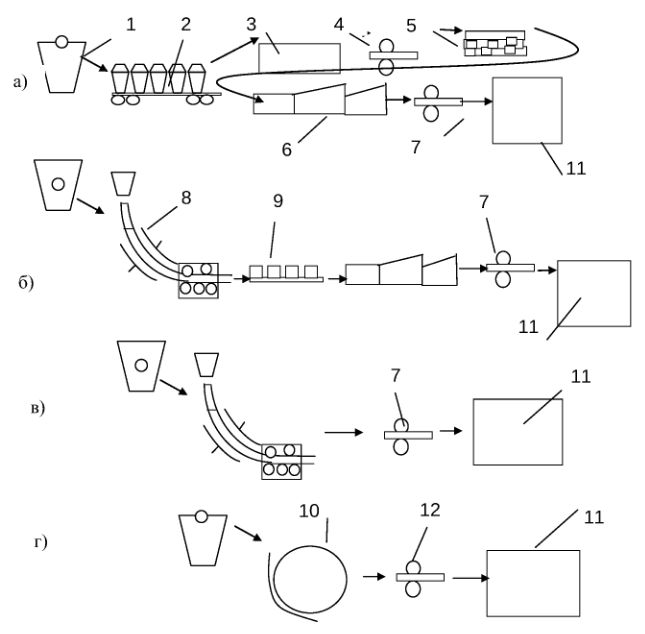
нагревательная печь, 7–сортопрокатный стан, 8–сортовая МНЛЗ, 9– адъюстаж МНЛЗ, 10–концептуальная сортовая МНЛЗ для заготовок с размерами конечного проката; 11–печь для термообработки проката; 12– клеть холодной прокатки; а–схема для разливки стали в изложницу, б–для непрерывной разливки стали; в–совмещенный процесс разливки-прокатки;
г–размер заготовки максимально приближен к размеру готового проката.
При втором способе получение исходной заготовки заменяется непрерывным литьём (разливкой) на машинах непрерывного литья заготовок (рис. 1.10б). Благодаря применению непрерывнолитой заготовки упраздняются нагрев слитков и соответствующие затраты энергии, а также уменьшаются потери металла на обрезь, доходящие до 15–20%.
Преимущества применения непрерывнолитой заготовки в производстве проката становятся ещё более значительными при совмещении процессов непрерывного литья и прокатки в одном неразрывном потоке. Для этой цели создаются литейно-прокатные модули (ЛПА), в которых в слитках на выходе выравнивается температура по сечению, и затем они поступают в валки прокатного стана (рис. 1 .10в).
Таким образом, осуществляется процесс кристаллизации и прокатки бесконечного слитка, т.е. непрерывное производство проката из жидкого металла.
Округленные значения удельных расходов условного топлива, затрачиваемого на нагрев металла в печах, для производства тонны готового сортового проката по разным технологическим схемам представлены на рис. 1.11.
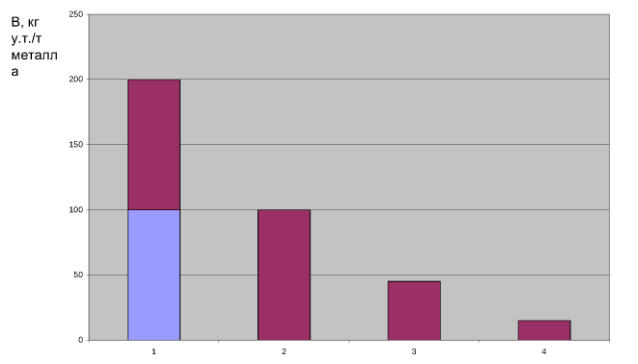
процессов разливки-прокатки.
Как видим, переход на каждый очередной этап эволюции рассматриваемых технологических систем (внедрение процессов непрерывной разливки стали, повышение энергоэффективности процессов тепловой обработки заготовок в печах, совмещение процессов разливки-тепловой обработки заготовок в рамках литейно-прокатных модулей) позволяет существенно снизить затраты энергии для производства тонны готового продукта.
Производство проката характеризуется высокой энергоемкостью и потреблением практически всех видов топливо-энергетических ресурсов, при этом преобладают затраты энергии, связанные с нагревом исходных заготовок.
Нагрев заготовок в печах представляет собой сложный теплообменный процесс, включающий передачу тепла от греющей среды, как правило, продуктов сгорания топлива путем излучения и конвекции к поверхности нагреваемого металла и распределение тепла внутри массива заготовок. Для нагрева при температурах греющей среды более 900°С преобладает доля лучистого теплового потока. По мере спада температур доля конвективного теплообмена является все более весомой и при температурах менее 500°С преобладает конвективный теплообмен.
Для охлаждения элементов конструкции печей, особенно толкательных методических, используется тепло охлаждающей среды. В данном случае возможно применение испарительного охлаждения, также как в доменных печах (охлаждение кожуха) и сталеплавильных печах (охлаждение подпятовых балок).
Известно, что снижение температуры нагрева заготовок на прокатку, на 100°С обеспечивает уменьшение удельного расхода топлива на 9,0-10,0%. При этом на самом участке нагрева заготовок как правило не требуется проведение дополнительных технических или организационных мероприятий. Производство проката характеризуется высокой энергоемкостью и потреблением практически всех видов топливо-энергетических ресурсов.
Основным фактором, определяющим выбор температуры нагрева заготовок под прокатку, является необходимость получения заданной структуры металла, обеспечивающей соответствующие служебные свойства готового проката. В то же время снижение температуры нагрева исходных заготовок ограничивается возможностями прокатного стана, так как приводит к повышению механических и электрических нагрузок на весь прокатный стан. Кроме того, из-за неоднозначности изменения температуры конца прокатки при снижении температуры нагрева заготовок на действующих прокатных станах усложняется управление температурным режимом прокатки, что весьма существенно при термической обработке готового проката в потоке стана.
Пропускная способность участков нагрева заготовок под прокатку позволяет реализовать энергоэкономные технологии, в частности технологии прокатки с пониженными температурами нагрева исходных заготовок и низкотемпературной прокатки. Энергозатраты в нагревательных печах и прокатных станах определяется путем совместной оптимизации работы этих участков.
Элементы конструкции печных агрегатов, определяющие уровень энергоэффективности их работы
Уровень энергоэффективности печного агрегата определяется не только выбором рациональных технологических параметров, но и в значительной мере зависит от используемых конструктивных решений.
Некоторая часть энергии топлива теряется на потери аккумуляцией, теплопроводностью через ограждающую конструкцию, с охлаждающей средой. Величина потерь через ограждающую конструкцию зависит от установленного внутри печи температурного уровня, характера работы агрегата во времени, однако в наибольшей мере она зависит от теплоизоляционных характеристик элементов ограждающей конструкции.
В отечественной промышленности вплоть до последнего времени традиционно ограждающая конструкция состояла из двух слоев:
- огнеупорного, выполненного из плотного кирпича, как правило, шамотного (среднее значение коэффициента теплопроводности 1 Вт/(м·К));
- теплоизоляционного, выполненного из пористого кирпича (среднее значение коэффициента теплопроводности 0,4-0,6 Вт/(м·К)).
В последнее время усиливается тенденция использования керамоволокнистых материалов для изоляции тех участков ограждающей конструкции, которые не испытывают значительных механических нагрузок (футеровка свода и стен агрегатов). Керамоволокнистые материалы имеют плотность 100-200 кг/м3 и коэффициент теплопроводности 0,05-0,2 Вт/(м·К). Огнеупорность керамоволокнистых материалов несколько меньше, чем для традиционно используемых плотных кирпичей. Однако этот показатель их работы постоянно совершенствуется. Керамоволокнистые материалы могут использоваться как для тепловой изоляции элементов создаваемых печных агрегатов, так и для реконструкции существующего печного оборудования путем добавления на внутреннюю поверхность имеющейся футеровки.
Продукты сгорания, покидающие камеру печи, уносят значительную часть энергии топлива. Для повышения эффективности печей традиционно используют теплообменные устройства (рекуператоры или регенераторы), позволяющие использовать часть тепла уходящих продуктов сгорания для нагрева воздуха, идущего на сжигание топлива.