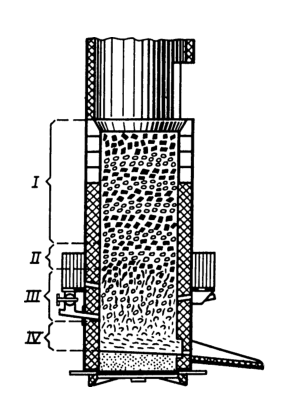
I – зона подогрева; II – зона плавления; III –
зона перегрева; IV — горн
Вагранка — шахтная печь, работающая по принципу противотока. По условиям теплообмена между металлом, коксом и газами всю шахту вагранки можно условно разбить на четыре зоны (рис. 52). Зона I – зона подогрева шихты; она простирается от завалочного окна вниз до того уровня, на котором температура поверхности кусков чугунной шихты достигает температуры плавления (1150—1200 °С). Размеры этой зоны не постоянны. Они зависят от многих факторов, в первую очередь от расхода кокса и воздуха и размеров кусков шихты. Зона II — зона плавления кусков металлической шихты. Продолжительность плавления 5—15 мин в зависимости от размеров кусков, состава материала и условий теплообмена. За это время куски успевают опуститься в холостую колошу на 300—500 мм, т.е. время плавления определяет размеры зоны плавления. Зона III — зона перегрева жидкого чугуна, которая начинается с того места, где образуются капли чугуна и простирается до нижнего ряда фурм. Капли чугуна, стекая по кускам раскаленного кокса и омываясь потоком разогретых до высокой температуры газов, значительно перегреваются. Этому способствует и состав газовой атмосферы, так как в зоне фурм газы содержат свободный кислород, который частично окисляет примеси чугуна и за счет этого дополнительно его перегревает. Зона IV — горн вагранки; она находится в нижней части шихты между нижней кромкой нижнего ряда фурм и лещадью. В этой зоне кокс и продукты его горения имеют более низкую температуру из-за недостатка кислорода. Чугун, стекая по кускам кокса и располагаясь между ними (при отсутствии копильника), охлаждается и насыщается углеродом и серой, поэтому желательно, чтобы время пребывания чугуна в горне вагранки было минимальным.
В вагранке происходит ряд химических реакций. Основные из них – угар элементов чугуна под воздействием окислительной атмосферы и образование шлака из флюсов, оксидов элементов чугуна, частиц неметаллических материалов, приставших к кускам шихты, оплавленной футеровки печи и золы кокса. Кроме того, жидкий чугун взаимодействует со шлаком и насыщается серой и углеродом из кокса. Все металлургические процессы, протекающие в вагранке, взаимосвязаны. На них влияют температурные условия в печи, характер газовой атмосферы, состав шихты, жидкого металла и шлака.
Горение ваграночного топлива
В вагранке твердое кусковое топливо горит в слое большой высоты, так что весь кислород воздуха успевает полностью прореагировать с топливом. Воздух, поступая в фурмы вагранки с определенной скоростью, проникает в шахту на некоторую глубину, а затем начинает подниматься вверх по шахте, все время взаимодействуя с углеродом топлива по реакциям:
С + 0,5 O2 = СО + 110964 кДж/моль;
С + O2 = CO2 + 395052 кДж/моль.
Образовавшейся СО при наличии свободного кислорода догорает:
СО + 0,5 O2 = CO2 + 284088 кДж/моль.
У поверхности кусков топлива повышается концентрация CO2 и температура газов и, в соответствии с законами физики, CO2 будет перемещаться в поток газов, где его концентрация мала. Однако частично CO2 будет
взаимодействовать с раскаленным углеродом топлива по реакции
С + CO2 = 2CO – 173124 кДж/моль.
Образовавшейся СО догорает и образуется CO2, т.е. поток воздуха обогащается CO2 и обедняется кислородом, который расходуется на процесс горения. Та зона холостой колоши, где имеется свободный кислород, называется кислородной зоной. Она простирается от фурм до зоны, где кислород практически израсходован. В конце кислородной зоны температура газов достигает максимума; реакции горения, протекающие с выделением теплоты, затухают, а реакция восстановления CO2, идущая с поглощением теплоты, получает значительное развитие. Зона холостой колоши, где увеличивается концентрация СО в ваграночных газах называется редукционной зоной. Она простирается вверх над кислородной зоной до зоны плавления, где температура газов падает до 1250 °С, а реакция восстановления CO2 значительно замедляется.
Итак, активная часть холостой колоши — слой кокса, расположенный от фурм до зоны плавления, условно может быть разделена на две зоны: кислородную, где поток газов еще содержит кислород и горение завершается в основном образованием CO2, и редукционную, где свободного кислорода практически нет продукты горения обогащаются СО за счет восстановления CO2, температура поверхности кусков кокса ниже температуры газов.
Высота кислородной зоны определяется в основном размерами кусков кокса (поверхностью взаимодействия) и колеблется от шести до восьми диаметров кусков при холодном дутье и от четырех до шести при подогреве воздуха до 500 °С. Изменение расхода воздуха не сказывается на высоте этой зоны. Реакция восстановления CO2 протекает тем медленнее, чем ниже температура, поэтому в зоне плавления, когда газы теряют значительное количество теплоты на реакцию восстановления CO2, плавление и перегрев жидкого чугуна, эта реакция замедляется. Таким образом, зона плавления определяет верхнюю границу редукционной зоны. Выше зоны плавления до самого загрузочного окна состав газов изменяется незначительно, в основном за счет реакции диссоциации известняка.
Состав колошниковых газов изменяется в зависимости от расхода кокса, воздуха, способа подвода воздуха, температуры его подогрева, размеров кусков кокса, его реакционной способности и других факторов.
Из табл. 8 видно, что при подогреве дутья, когда в вагранку вносится большое количество дополнительной теплоты и температура газов в зоне холостой колоши значительно возрастает, реакция восстановления CO2
протекает быстрее и газ больше насыщается СО. В металлургических вагранках, работающих на горячем дутье и мелкой окисленной (дешевой) шихте, специально повышают расход кокса для получения большего количества СО в продуктах горения, чтобы создать восстановительную атмосферу в печи для предотвращения угара железа и примесей чугуна.
Из сказанного следует, что продукты горения топлива в вагранке являются не только источником теплоты, но и важным металлургическим фактором, влияющим на металлургические процессы, протекающие в печи.
Так как максимальное количество теплоты выделяется при превращении углерода в CO2, то изменение температуры газов по высоте холостой колоши в редукционной зоне пропорционально концентрации CO2. Чем
выше температура газов на выходе из кислородной зоны, тем быстрее протекает реакция восстановления CO2 и резче падает температура газов в результате реакции и затрат теплоты на расплавление шихты в конце редукционной зоны и зоны плавления. Выше зоны плавления наблюдается постепенное снижение температуры колошниковых газов, отдающих теплоту на нагрев кусков шихты и кокса. На рис. 53 показано изменение состава и температуры газов по высоте шахты вагранки от фурм до загрузочного окна.
Следовательно, процесс горения ваграночного топлива является основой ваграночной плавки, поэтому в зависимости от организации этого процесса (подача воздуха через один или два ряда фурм, его подогрев или обогащение кислородом, применение двух видов топлива и др.) зависят состав и температура ваграночных газов и, как следствие, условия теплообмена и металлургические процессы, протекающие в печи.
Изменение химического состава компонентов шихты в разных зонах печи
Чтобы получить чугун требуемого химического состава, нужно составить шихту — подобрать в определенном количестве разные шихтовые материалы и учесть те изменения, которые произойдут с химическим составом этих материалов в разных зонах вагранки. Рассмотрим изменения (химические реакции), которые протекают при взаимодействии компонентов шихты с ваграночными газами, коксом и шлаком. Ваграночные газы в зависимости от соотношения 100 CO2 / (CO2 + СО) могут иметь слабо окисленный нейтральный или восстановительный характер. В обычной слабоокислительной атмосфере происходят следующие реакции взаимодействия газов с компонентами чугуна (окислитель CO2 ) :
Fe + CO2 = FeO + CO;
Si + 2CO2 = SiO2 + 2CO;
Mn + CO2 = MnO + СО;
3Fe + SO2 = FeS + 2FeO;
С+ CO2 = 2CO;
Fe3C + CO2 = 3Fe + 2CO.
В зоне нагрева шихты все ее компоненты (чушковый чугун, чугунный и стальной лом, ферросплавы, стружка) будут окисляться по указанным реакциям начиная с поверхности куска, образуя оксиды железа, кремния, марганца. Кроме того, поверхность кусков металла будет обезуглероживаться и насыщаться серой. Однако все эти реакции проникают вглубь не более чем на 0,25—0,3 мм и при обычных размерах кусков шихты на изменение химического состава значительно не влияют.
Если в шихту добавлять тонкий листовой материал или стружку навалом (без брикетирования), то реакции окисления оказывают существенное влияние на конечный состав чугуна.
В зоне плавления, располагающейся, как правило, в редукционной зоне холостой колоши, отсутствует свободный кислород и в избытке присутствует углекислый газ Все процессы химического взаимодействия,
которые имеют место в зоне нагрева будут протекать и здесь, но скорости этих реакций значительно возрастут из-за того, что температура газов и кусков шихты значительно выше и образовавшиеся на плавящейся поверхности оксиды стекают оголяя неокисленную поверхность для протекания реакций, т.е. в этой зоне отсутствует защитный покров пленки оксидов. Образовавшиеся капли металла отрываются от поверхности куска и стекают вниз по раскаленным кускам кокса.
В зоне перегрева чугуна, располагающейся как в редукционной, так и в кислородной зонах капли чугуна, перетекая по кускам раскаленного кокса перегреваются, а оксиды железа частично восстанавливаются углеродом, а частично растворяются в металле, передавая кислород элементам, имеющим большое сродство с ним, чем железо. В итоге обменных процессов происходит угар элементов чугуна по реакциям
2Fe + O2 = 2FeO;
Fe + CO2 → FeO + CO;
2FeO + Si = SiO2 + 2Fe;
FeO + Mn = MnO + Fe;
FeO + C = CO + Fe.
При наличии в чугуне хрома в этой зоне он окисляется по реакции
3FeO + 2Cr = Cr2O3 + 3Fe.
Так как реакции окисления кремния, марганца и хрома протекают с выделением теплоты то по мере повышения температуры капли чугуна интенсивность протекания этих реакций уменьшается, несмотря на то, что в кислородной зоне холостой колоши в продуктах горения еще находится свободный кислород
Реакция взаимодействия оксидов железа с углеродом протекает с поглощением теплоты поэтому чем выше температура газов и перегрев капель, тем быстрее происходит процесс раскисления и обезуглероживания металла. Однако капли, стекая по кускам раскаленного кокса, растворяют углерод кокса повышая его концентрацию в металле. Общее содержание углерода определяется скоростями этих двух реакций и повышается с увеличением температуры выплавляемого чугуна. В зоне перегрева жидкого чугуна заканчивается формирование шлака
В горне вагранки состав газовой фазы является восстановительным ; так как реакция восстановления углекислого газа идет до конца при отсутствии кислорода: металл и шлак охлаждаются в результате передачи теплоты поверхности кускам кокса, станкам и поду печи. В горне, если вагранка работает без копильника, жидкий чугун покрыт слоем шлака и находится между кусками кокса. Он продолжает насыщаться углеродом, если не был им насыщен, и серой.
Так как шихта ваграночной плавки состоит из кусков разного размера с разной температурой плавления, то куски чугуна и стали одной и той же колоши металла плавятся на разной высоте в разное время и металл стекает отдельными струйками, а чугун, скапливаясь между кусками кокса, плохо перемешивается, в результате чего химический состав в начале выпуска в ковш может отличаться от состава в конце выпуска.
Итак, при прохождении компонентов шихты через все зоны вагранки происходит изменение химического состава (угар и пригар) в зависимости от условий работы вагранки (табл. 9).
Изменение содержания углерода, серы и легирующих элементов при плавке
Пригар углерода в зависимости от условий работы вагранки может значительно изменяться. Это изменение связано с составом шихтовых материалов. Если шихта содержит незначительное количество стального лома, а основные компоненты — доменные чугуны, машинный лом и отходы собственного производства с высоким процентом углерода, то насыщение углеродом будет минимальным; если же шихта содержит большой процент стального лома (например, при плавке ковкого чугуна), то пригар значительно возрастает. Капли жидкой стали содержат 0 , 2 — 0,45 % С и, стекая по кускам раскаленного кокса, интенсивно поглощают углерод, в результате чего содержание его повышается до 2,5 %. Когда капля науглероженной стали попадает в горн вагранки, она смешивается с чугуном и соприкасается с коксом. Науглероживание неподвижной жидкой массы чугуна в горне вагранки протекает значительно медленнее, и содержание углерода здесь повышается дополнительно на 0,3 – 0,5 %.
Науглероживание — сложный физико-химический процесс, на скорость протекания которого влияют многие факторы: температура выплавляемого чугуна, расход кокса температура подогрева воздуха, содержание углерода в шихте, размер кусков кокса, содержание в нем золы, глубина горна и др. На науглероживание оказывает влияние также состав чугуна и шлака: чем больше в чугуне кремния и меньше марганца, тем меньше степень науглероживания; чем кислее шлак, тем он более вязкий и дольше задерживается на поверхности кусков кокса и тем меньше чугун насыщается углеродом.
Содержание серы в жидком чугуне может значительно увеличиваться (в 1,5—2 раза) при плавке чугуна с кислым шлаком на холодном воздухе, но может и уменьшаться при работе с основными шлаками на горячем дутье (см. табл. 9). Сера относится к числу вредных примесей чугуна; она находится в нем главным образом в виде соединений MnS и FeS и понижает прочность и пластичность, поэтому стараются, чтобы ее содержание было не более 0,12 %. При большем содержании серы значительно понижаются литейные свойства чугуна. Главными источниками повышения содержания серы в металле являются кокс (вносится 70—80 % серы), металлозавалка (20-30 %) и известняк (около 1 %). Уменьшения содержания серы в чугуне можно добиться понижением расхода кокса, применением низкосернистого кокса, повышением температуры выплавляемого чугуна, присадкой в шихту карбида кальция CaC2 . Карбид кальция, сгорая в области фурм, значительно повышает температуру чугуна, шлака и газовой фазы, улучшает условия обмена между чугуном и шлаком, повышая растворимость серы в последнем. Частично локализовать вредное влияние серы можно марганцем, который образует с ней соединение MnS, имеющее температуру плавления 1620 °С и значительно меньшую плотность по сравнению с жидким чугуном, поэтому большая часть этого соединения всплывает в шлак. Даже оставшись в чугуне, MnS образует обособленные включения, не оказывающие заметного влияния на прочность чугуна. Значительного снижения серы в чугуне можно добиться при работе вагранки с основной футеровкой и основными шлаками при подогреве дутья.
Фосфор попадает в чугун только из металлической завалки, так. как в топливе его нет. При переплавке чугуна в вагранке с кислой футеровкой содержание фосфора в процессе плавки не изменяется. Если требуется получить чугун с низким содержанием фосфора, необходимо подбирать шихтовые материалы с низким содержанием фосфора. Снизить его содержание в чугуне можно при плавке в вагранке с основной футеровкой при использовании в качестве флюса смеси известняка с железной рудой. Реакция обесфосфорирования полнее протекает при ’’холодном” ходе вагранки, когда температура чугуна на желобе не превышает 1350 °С.
Из сказанного следует, что для удаления серы и фосфора из чугуна требуется применение основной футеровки вагранки и основных шлаков. Однако одновременно удалить эти элементы нельзя, так как для удаления серы требуется высокая основность шлака, высокая температура в зоне холостой колоши и низкое содержание закиси железа в шлаке, а для удаления фосфора — пониженная температура в холостой колоше и высокое содержание закиси железа в шлаке. Если требуется повысить содержание фосфора в жидком чугуне, в шихту добавляют апатитонефелиновую руду (1 % руды позволяет поднять содержание фосфора на 0,1 %).
При необходимости добавления легирующих элементов в чугун для повышения его качества следует учитывать что никель и медь можно присаживать в шихту в виде природно-легированных материалов или в чистом виде, они не угарают.
Ваграночный шлак
Состав и свойства ваграночного шлака оказывают большое влияние на характер плавки и свойства полученного металла. Шлак в вагранке образуется в результате угара элементов чугуна (1—2 % массы металла, из них кремний угарает на 10-20 %, марганец на 10-30%, железо на 0,25-1,5 %), оплавления футеровки (0,4-3 %), прилипания к шихте песка и формовочной смеси (2 %), образования золы топлива (1—2 %), ввода флюсов в целях понижения вязкости шлаков (2,5-4 %), флюсы полностью переходят в шлак. Таким образом, шлака образуется 6—8 % массы жидкого чугуна. Средний состав шлака для кислого процесса следующий %: 40—60 кремнезема, 20-35 извести; 2—20 глинозема; 1-5 магнезии; 0,5—10 закиси железа; 1—5 закиси марганца; 0,1—0,5 оксидов фосфора; 0,05—0,03 серы; 0,2—0,3 чугуна в виде запутавшихся капель.
Три составляющие — кремнезем, оксид кальция и глинозем — дают 80—90 % всей массы шлака. Их соотношение определяет температуру плавления шлака и его жидкотекучесть. Шлак должен иметь высокую жидкотекучесть, обеспечивающую его легкое отделение от чугуна, стекание по стенкам шахты без образования настылей, дополнительное поглощение серы из чугуна и легкость удаления через шлаковую летку. Вязкость шлака снижается, а жидкотекучесть повышается при замене части CaO на MgO с повышением содержания в шлаке FeO и MnO. Однако повышенное количество FeO и MnO свидетельствует о холодном ходе плавки и повышенной окисленности чугуна. Шлак становится темным, почти черным, вместо зеленого. Оксиды FeO и MnO сильно разрушают футеровку печи.
Для получения шлака с наибольшей жидкотекучестью рекомендуется, чтобы отношение кремнезема к глинозему в нем было 6 — 8 , а отношение оксида кальция к оксиду магния 2. Хорошо понижает вязкость шлака плавиковый шпат CaF2, который ускоряет реакции обмена между шлаком и чугуном, увеличивает растворимость серы в шлаке. Однако плавиковый шпат сильно разъедает футеровку печи и дорого стоит.
Состав шлака надо подбирать таким образом, чтобы он меньше взаимодействовал с основными составляющими футеровки печи, последняя для уменьшения разрушения должна быть по возможности менее пористой. Для шамотной футеровки желательно иметь шлак по составу, близкий шамоту %: 40-48 SiO2; 10-15 Al2O3; 25-30 CaO; до 8 FeO; 5-8 MnO; 3-5 MgO. Для вагранки, футерованной основными материалами, желательно иметь шлак следующего состава %: 25-30 SiO2 ; 40-50 CaO; 2-20 Al2O3; 1—5 MgO; 0,5-3 FeO; 1-3 MnO; 0,5-1,0 P2O5; 0,5—1,0 S.
Особенности кислого и основного ваграночных процессов
При кислом процессе в большей степени окисляются элементы, образующие основные оксиды и в меньшей степени элементы, образующие кислые оксиды.
Например, при температуре выше 1450 °С в вагранках с кислой футеровкой в большей степени будет угарать углерод, а в меньшей — кремний. Более того возможно даже восстановление кремния из оксидов. При кислом процессе происходит меньшее насыщение чугуна углеродом, так как кислый шлак менее интенсивно смывает кислую золу с поверхности кусков кокса, при этом уменьшается площадь соприкосновения капель чугуна с углеродом кокса. Для кислого шлака основность (отношение основных оксидов к кислотным) изменяется от 0,4 до 0,9. При взаимодействии шлака с чугуном не удается снизить содержание серы или фосфора, хотя при повышении температуры чугуна и шлака коэффициент распределения серы между шлаком и чугуном увеличивается и создается возможность перехода серы из чугуна в шлак. Большую часть вагранок футеруют шамотным кирпичом работают они с кислыми шлаками.
Если вагранку футеровать магнезитовым или доломитовым кирпичом и увеличить расход известняка до 4—6 %, то основность получаемого шлака будет 1,2—2,0. Такой шлак, однако, имеет повышенную вязкость, поэтому для нормальной работы вагранки надо повысить температуру в печи за счет подогрева дутья. Работа вагранки на основном шлаке (основной ваграночный процесс) имеет следующие особенности: увеличивается угар кремния, повышается насыщение чугуна углеродом за счет того, что основной шлак хорошо смывает кислую золу с кусков кокса, облегчая взаимодействие углерода с чугуном. Кроме того, при повышенном угаре кремния растворимость углерода в чугуне повышается, значительно понижается угар марганца, создается возможность значительного понижения содержания серы в чугуне. Вот почему основной процесс получил развитие при производстве чугуна модифицированного магнием. Для образования шаровидного графита в чугуне в нем должно быть низкое содержание серы.
С повышением основности шлака при горячем ходе ваграночной плавки уменьшается количество серы в металле и повышается ее растворимость в шлаке. Процесс можно описать реакцией
[FeS]+ (CaO) ↔ (CaS) + (FeO).
При этом образуется CaS — прочное соединение, не растворимое в чугуне и хорошо растворимое в шлаке. В присутствии углерода процесс десульфурации (обессеривания) протекает по реакции
[FeS] + (CaO) + [С] ↔ (CaS) + [Fe] + [CO].
Так как с повышением основности шлака вязкость его увеличивается, то для успешной десульфурации необходимо повысить температуру в холостой колоше вагранки, а чтобы реакция не протекала в обратном направлении, необходимо уменьшить содержание закиси железа в шлаке, что также будет происходить в повышении температуры в зоне реакции.
При основном ваграночном процессе снижение содержания фосфора в чугуне происходит по реакциям
[Fe2P]+ 2,5 (FeO) = 0,5 (P2O5)+ 4,5 [Fe];
(P2O5)+ 3 (FeO) = (FeO)3 P2O5;
(FeO)3 P2O5 + 4CaO = (CaO)4 P2O5 + 3FeO.
Для того чтобы этот процесс шел активно, необходимо иметь не менее 7 % известняка, 1—5 % железной руды, а температура чугуна на желобе должна достигать 1300—1350 °С.