Процессы получения губчатого железа осуществляются при умеренных температурах с использованием газообразного или твердого восстановителя в различных агрегатах: шахтных, трубчатых, туннельных, муфельных, отражательных, электронагревательных печах, ретортах периодического действия, конвейерных машинах, реакторах с кипящим слоем и др. Иногда эти агрегаты соединены в комплексы, в которых наиболее часто сочетаются с электропечью (электродоменной или дуговой), для получения жидкого металла (чугуна и стали).
Чаще всего губчатое железо применяют как высокочистую добавку к стальному лому, а также для замены лома в случае его дефицита или высоких цен. Однако повышение цен на лом не является главной причиной возросшего интереса к губчатому железу. Наиболее стабильный спрос на него отмечается в странах с недостаточными мощностями доменного производства и поставками стального лома. Меньшую роль в производстве металла губчатое железо играет в промышленно развитых странах Европы, в Японии и США, где железная руда, стальной лом и твердое топливо продолжают оставаться достаточно дешевыми, что обеспечивает производство чугуна при более низких затратах, чем производство губчатого железа.
Основными процессами, используемыми на работающих, строящихся и проектных установках для производства губчатого железа, являются процессы с применением шахтных печей (главным образом процессы Мидрекс, ХиЛ-III) и реторт периодического действия (ХиЛ-I, ХиЛ-II). Процессы с использованием вращающихся печей и твердого восстановителя (процессы СЛ-РН, Крупп-Айзеншвам, Кавасаки и др.) в последние годы находят промышленное применение главным образом при переработке металлургических отходов — пылей и шламов, которые содержат примеси цинка, свинца и др., а также комплексных железных руд (богатых титаном, хромом, никелем, марганцем и др.), не пригодных для использования в доменных печах.
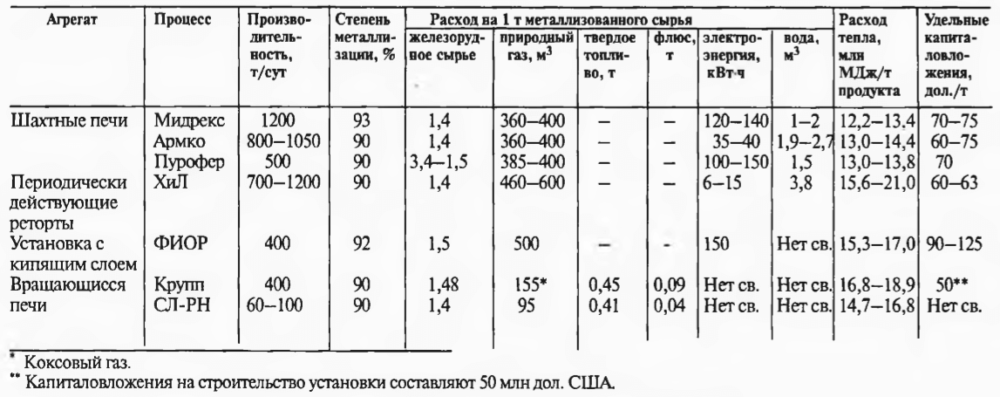
Процессы в кипящем слое получили меньшее распространение в связи с целым рядом специфических особенностей (жесткие требования к гранулометрическому составу, газодинамические ограничения существования кипящего слоя, температурные условия и др.). Преимущественное развитие в мировой практике прямого восстановления процессов Мидрекс и ХиЛ обусловлено их лучшими технико-экономическими показателями.
Химический состав
Основными показателями качества металлизованного продукта являются степень металлизации, содержание углерода и вред ных примесей.
Степень металлизации равна отношению металлического железа к железу общему: ηмет = Feмет/Feобщ, 100%.
Для губчатого железа, предназначенного для выплавки стали, ηмет = 87—97%. Низкая степень металлизации (87—89%) применяется в случае использования высокофосфористых руд и для получения необходимой окисленности шлака при дефосфорации металла в процессе расплавления губчатого железа.
Практикой установлено, что с целью использования высокой мощности трансформаторов электропечей и предохранения футеровки стен и сводов от воздействия электрических дуг плавление металлизо- ванных окатышей должно сопровождаться вспениванием шлака за счет реакций окисления углерода. Толщина шлакового слоя на ванне металла при этом увеличивается в четыре-пять раз и экранирует электрические дуги. Создать такой шлаковый слой можно, вдувая в ванну газообразный кислород, а в случае его отсутствия, добавляя окисленные окатыши или применяя металлизованные окатыши с пониженной степенью металлизации. Такая технология некоторое время применялась на ОЭМК, однако это вело к повышенному расходу электроэнергии при расплавлении.
Расчеты и опыт показывают, что с повышением степени металлизации с 90 до 94% удельный расход электроэнергии на расплавление 1 т металла снижается примерно на 18 кВт·ч на каждый процент степени металлизации.
Оптимальным содержанием углерода в металлизованном продукте, предназначенном для получения стали, является такое содержание, которое достаточно до восстановления оксидов железа металлизован- ных окатышей и науглероживания металла до требуемых пределов. Это важно при выплавке ответственных марок стали, так как углерод окатышей по сравнению с углеродом других науглероживателей, особенно кокса, не содержит вредных примесей. Кроме того, в настоящее время стоимость углерода, полученного из природного газа, значительно меньше, чем углерода в кокса. В некоторых случаях выгодно иметь в губчатом железе большое (до 3,5 %) содержание углерода. Выжигание 3% углерода кислородом во время плавления губчатого железа позволяет экономить до 50 кВт·ч/т жидкой стали. На установках металлизации ОЭМ К производят металлизованные окатыши с содержанием углерода 0,5—2,0 % по требованиям заказчика.
Физические свойства
Крупность кусков губчатого железа, используемого при выплавке стали, находится в пределах 3—50 мм.
Время расплавления металлизованных окатышей фпл прямо пропорционально квадрату их размера R: τпл =AR2, где A — постоянная величина.
С уменьшением среднего размера окатышей, например с 12 до 10 мм, время расплавления уменьшается почти в 1,5 раза, что, по-видимому, существенно сказывается на производительности электропечей, так как электропечи ОЭМК имеют большой резерв по мощности трансформаторов. Нижний предел размеров ограничивается выносом пыли при непрерывной загрузке, а также повышенным окислением железа при плавлении.
Кажущаяся плотность губчатого железа (отношение массы частицы к ее объему, ограниченному внешней поверхностью) также влияет на скорость процесса плавления окатышей и, как правило, с увеличением плотности скорость плавления увеличивается. Кажущаяся плотность зависит от пористости материала, которая составляет 50—60 % и обусловлена пористостью исходных материалов и уменьшением объема оксидов в результате восстановления. Высокая пористость уменьшает теплопроводность губчатого железа, которая для Лебединских окатышей при нагреве от 20 до 1000 °С изменяется от 1,6 до 1,0 Вт/(м·К). Прочность металлизованных окатышей на раздавливание зависит от свойств обожженных окатышей и температуры восстановления в шахтных печах, обычно она находится в пределах 500—1500 Н/окатыш.
Прочность металлизованных окатышей на истирание в барабане (содержание фракции 5%, а на удар (содержание фракции >5 мм) ≥ 95%, что обеспечивает транспортировку, складирование и загрузку окатышей в электропечь с образованием небольшого количества мелочи.
Большое значение для хранения металлизованных окатышей имеет удельная поверхность, доступная взаимодействию железа с окислителями, включающая внешнюю поверхность кусков и внутреннюю поверхность открытых пор. Удельная поверхность металлизованных окатышей обычно составляет 0,5—1,5 м2/г. Большая величина внутренней поверхности губчатого железа объясняется большим количеством пор малого размера (в основном 0,1—1,0 мкм), количество которых уменьшается, а размер увеличивается с увеличением времени выдержки и подъемом температуры, т. е. с увеличением степени металлизации. При степени металлизации 83—85% удельная поверхность окатышей составляет 2—3 м2/г, тогда как при степени металлизации 90% удельная поверхность сокращается в полтора-два раза.
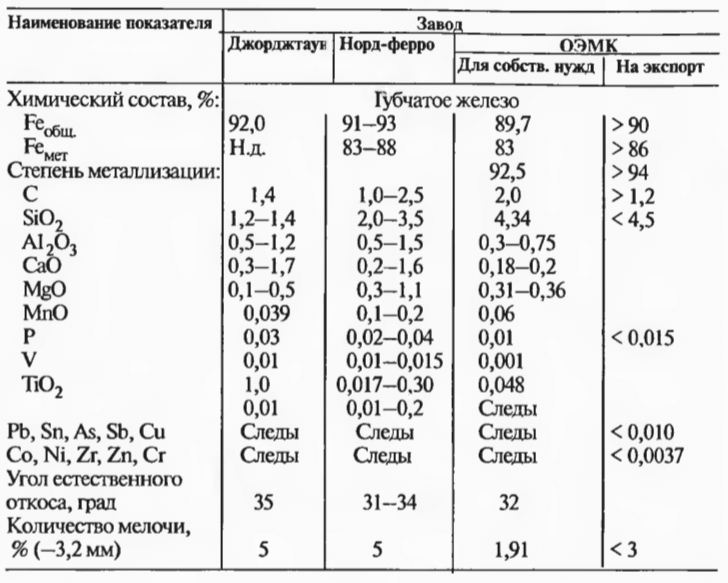
Характеристики губчатого железа процесса Мидрекс приведены в таблице выше.
Хранение и транспортировка металлизованного сырья
Как уже отмечалось, процессы взаимодействия кислорода с железом быстрее проходят в присутствии воды (коррозия):
Fe + H2O + ½ O2 = Fe(ОН)2 + 9300 кДж/кг.
Продукты реакции этого процесса получаются пористыми и не служат защитой от дальнейшей коррозии. На окисление 1 кг железа требуется 0,2 кг кислорода, с которым поступает 0,75 м3 азота и 0,4 м3 паров воды. Если учитывать испарение влаги, нагрев азота и окатышей и не учитывать потерь тепла, то при окислении 1 % Fe система должна нагреться на 60 °С. Если в штабель материала попадает вода, то окатыши начинают разогреваться, в результате чего образуется ток воздуха через металлизированные материалы и фронт окисления начинает передвигаться по ходу потока, нагревая окатыши (обычно снизу вверх). Тепло химической реакции в этом случае расходуется только на нагрев азота воздуха, поэтому температура слоя будет постоянно расти. Однако этот процесс ослабляется потерями тепла через наружную открытую поверхность окатышей и на испарение излишнего количества влаги. Чем больше масса окатышей и выше высота штабеля, тем благоприятнее условия для разогрева окатышей, так как уменьшается поверхность отвода тепла и увеличивается путь продвижения фронта окисления, т. е. увеличивается аккумуляция тепла перед ним.
Из опыта работы и исследований, проведенных на ОЭМК, выработаны определенные правила по транспортировке и хранению металлизованых окатышей без их значительного окисления и возгорания.
Перевозку окатышей железнодорожным транспортом можно осуществлять в открытых полувагонах и окатышевозах. При использовании только сухих окатышей их перевозят в закрытых хопперах. Если окатыши в пути подвергнутся воздействию осадков и содержание влаги в поверхностном слое будет > 5%, то мокрые окатыши нужно отделить от сухих и складировать отдельно в штабель высотой ≤ 1,0 м. Использование этого материала в сталеплавильных печах допускается после удаления из него влаги естественным путем, добавляя его к сухому продукту в количестве ≤ 10%.
Для хранения мзталлизованных окатышей можно использовать герметичные бункера, обособленные складские помещения, открытые или оборудованные навесом площадки, а также различную мелкую тару (контейнеры). Длительное хранение окатышей предпочтительно осуществлять в герметичных бункерах под инертной атмосферой или в крытых складских помещениях с естественной вентиляцией. Длительное хранение окатышей на открытых площадках не гарантирует сохранения качества продукта.
Максимальная высота штабеля не должна превышать 3 м, максимальная ширина 10 м, длина штабеля не ограничивается. Не допускается размещение штабеля над теплотрассами, а также под транспортными эстакадами, по которым перемещаются нагретые и раскаленные материалы, легковоспламеняемые вещества и обожженная известь. Не допускается укладка в штабель увлажненных окатышей. При укладке в штабель учитывается температура окатышей. Если температура 100 °С разгружаются на отдельную площадку слоем до 0,5 м.
При хранении металлизованных окатышей в бункерах в качестве защитной атмосферы можно использовать азот, охлажденный и осушенный дымовой газ с содержанием кислорода ≤ 2%. Избыточное давление азота в бункере должно поддерживаться на уровне 20—30 Па. Контроль за состоянием окатышей в бункерах осуществляется путем ежесменного отбора газа из бункера, определения в нем содержания кислорода и водорода и измерения температуры при выгрузке. Суммарное содержание водорода и оксида углерода в бункерном газе не должно превышать 3%.