Конвертер – металлургический агрегат для получения стали путём продувки расплавленного чугуна воздухом или кислородом. По характеру технологического процесса конвертеры делятся на кислородные, бессемеровские и томасовские. В кислородных конвертерах продувка чугуна осуществляется технически чистым (не менее 99,5 %) кислородом через верхнюю фурму, что позволяет получать сталь с низким содержанием азота. Обычно футеровка кислородного конвертера основная. В бессемеровском и томасовском конвертерах продувка чугуна происходит через донные фурмы воздухом. В бессемеровском процессе используется кислая футеровка, а в томасовском – основная. По сравнению с бессемеровским томасовский процесс позволяет эффективно удалять фосфор из фосфористых чугунов методом окисления. В 70-х годах ХХ века бессемеровский и томасовский процессы были вытеснены кислородно-конвертерным процессом.
Схема кислородного конвертера приведена на рис. 3.6. Принцип работы конвертера следующий. Конвертер – сосуд грушевидной или цилиндрической формы, открытый сверху. Через верхнее отверстие (горловину) подаётся стальной лом, заливается жидкий чугун, вводится кислородная фурма и ведётся продувка. Одновременно с началом продувки вводится 2/3 шлакообразующих добавок (известь с бокситом или плавиковым шпатом). Остальное количество добавок вводится по ходу продувки в течение 1/3 ее длительности. Загрузка добавок происходит из бункеров по специальным транспортерам в непрерывном режиме без остановки конвертера.
Кислородная фурма является водоохлаждаемой, многосопловой и располагается на расстоянии 0,7-3,0 метра от поверхности чугуна. Применение многосопловых фурм взамен односопловых позволяет резко снизить количество выбросов, увеличить расход кислорода, сократить длительность плавки. Давление кислорода составляет около 9-14 ат, сопла имеют форму сопла Лаваля, что позволяет создавать высокие (сверхзвуковые) скорости кислородной струи и внедрять кислород по всей высоте слоя жидкой ванны с образованием активно циркулирующих макрообъемов металла. Высокая концентрация кислорода способствует быстрому окислению кремния, марганца, углерода, фосфора, а также некоторого количества железа. Образующиеся окислы взаимодействуют с известью, образуя легкоплавкий шлак.
Готовая сталь выпускается в сталеразливочный ковш через лётку – специальное отверстие в боковой стенке. Шлак выливается через горловину в шлаковую чашу.
Раскисление конвертерной стали проводят в сталеразливочном ковше во время выпуска, т.к. ввод раскислителей в самом конвертере вызывает их высокий расход. При выплавке спокойной стали её раскисляют ферромарганцем, затем ферросилицием и в конце алюминием. При выплавке кипящей стали раскисление проводят только ферромарганцем.
В конвертере очень сложно получить легированную сталь из-за высокой степени окисления легирующих элементов, вводимых в конвертер, неравномерного распределения легирующих в объеме металла и захолаживания плавки при присадке большого количества легирующих в конвертер или ковш. Небольшое количество легирующих элементов (до 2-3 %) в виде ферросплавов вводят в ковш во время выпуска стали или загружают на дно ковша перед выпуском. Таким образом, в конвертере выплавляют, в основном, низколегированную сталь. Операция высокого легирования выполняется в установках внепечной обработки, типа “ковш-печь”.
В ходе плавки температура материала поднимается с 1250-1400 °С (температура жидкого чугуна) до 1600-1650 °С (температура готовой стали). Подъём температуры происходит без подвода извне химической энергии. Теплота выделяется в результате окисления примесей чугуна (углерода, кремния, марганца, фосфора) и железа. Общее количество теплоты, выделяющееся при окислении примесей, значительно превышает потребности теплоты для нагрева стали и шлака до требуемой температуры и для компенсации тепловых потерь через футеровку и горловину конвертера. Для компенсации избытка теплоты обычно вводят до 25-30 % стального лома. Редко используется для тех же целей железная руда (до 8 %). Возможно использование в виде охладителя таких материалов, как агломерата, окатышей, известняка, доломита и т.п.
Образующиеся при окислении углерода в большом количестве оксиды углерода (СО, СО 2 ) выделяются в газовую фазу и через горловину конвертера удаляются в тракт газоочистки. Оксиды Si, Mn, P, Fe участвуют в формировании шлака, а часть из них, главным образом оксиды железа (Fe2O3), удаляются с газом в виде пыли (до 280 г/м3 ). Поэтому конвертерный газ подвергают очистке. Состав очищенного конвертерного газа: СО = 85-90 %; СО2 = 8-14 %; О2 = 1,5-3,5 %; N2 = 0,5-2,5 %. Теплота сгорания газа довольно высокая – 9÷10 МДж/м3 . Выход конвертерного газа составляет 100-150 м3/т стали. Периодичность выхода газа затрудняет его использование.
Футеровка конвертера является основной, двух- или трехслойной. Внутренний слой толщиной 500-750 мм называется рабочим. Он выполняется из пропитанных обезвоженной каменноугольной смолой доломитовых или магнезитовых кирпичей. При обжиге новой футеровки летучие из смолы удаляются и остается цементирующий коксовый остаток, уменьшающий разъедание футеровки шлаком. Рабочий слой изнашивается в процессе работы под влиянием термических напряжений (из-за колебаний высоких температур), под воздействием ударов кусков шихты, особенно, крупных кусков металлолома, а также в результате химического взаимодействия со шлаком. Стойкость рабочего слоя составляет 400-800 плавок. Наружный слой футеровки называется арматурным и выполняют его из магнезитового или магнезитохромитового кирпича толщиной 110-250 мм. Этот слой непосредственно примыкает к кожуху и он не требует замены при ремонтах. Между рабочим и арматурным слоями обычно выполняется набивка из массы, по химсоставу соответствующей рабочему слою. Толщина набивки 50-100 мм.
Технологический режим конвертерного процесса (на примере конвертера ёмкостью 400 тонн) приведен в табл. 3.5.
Как следует из табл. 3.5, длительность цикла производства стали в конвертере составляет 38 минут. Для сравнения – процесс мартеновской плавки длится 8-12 часов.
Строго говоря, конвертер не является плавильной печью. Во-первых, в конвертер не подаётся топливо, а, во-вторых, исходный материал почти весь уже расплавлен (напомним, что плавильная печь – это печь для превращения каких-либо материалов в жидкое состояние…). Таким образом, конвертер по своим признакам является установкой внепечной обработки с продувкой окислительным газом. Однако наличие в завалке стального лома, компенсирующего чрезмерный разогрев стали при окислении примесей, позволяет исключить конвертер из установок внепечной обработки материала и поместить в особую категорию плавильных печей: с теплогенерацией за счет химической энергии жидкого чугуна. К слову сказать: иногда к этой категории относят и мартеновские печи, что не совсем правильно, т.к. мартеновская печь использует также и химическую энергию органического топлива.
Это же обстоятельство затрудняет сравнение конвертеров по расходу топлива. Обычно сравнение идёт по производительности, по расходу кислорода, по расходу огнеупоров, по расходу дополнительных материалов (известь, боксит, плавиковый шпат, железная руда). Эти показатели конвертерного процесса не учитывают теплотехническую сторону процесса. Предлагается считать топливом примеси, содержащиеся в чугуне. Тогда удельный расход условного топлива составит (при 79 % жидкого чугуна, 21 % лома) примерно 30-35 кг у.т./т стали. Косвенно расход теплоты в конвертере можно оценить по тепловому к.п.д. конвертера, который составляет примерно 70 %.
Ориентировочные материальный и тепловой балансы конвертера приведены, соответственно, в табл. 3.6 и 3.7.
Для снижения безвозвратно теряемой теплоты в конверторах можно предложить ряд мероприятий:
- сокращение потерь теплоты в окружающую среду через горловину (излучением) и через кладку (теплопроводностью);
- создание оригинальных устройств с целью использования физической и химической энергии конвертерного газа для, например, подогрева лома и сыпучих материалов до 1000 °С или для выработки пара, для обжига известняка;
- использование окатышей и металлизованных окатышей в качестве охладителей плавки взамен лома. Преимущества этого способа:
- сокращается длительность плавки за счёт исключения периода завалки лома;
- уменьшается зона максимальных температур в подфурменной зоне;
- уменьшается возможность повреждения футеровки кусками лома;
- использование физической теплоты шлака для получения пара, горячей воды;
- использование неочищенного конвертерного газа с температурой 900-1200 °С для восстановления окатышей и пыли, которые пойдут на разбавление лома. Отходящий при этом газ (900-1100 °С) можно использовать для предварительного нагрева окатышей при их восстановлении и далее на обжиг известняка, т.к. в газе содержится ∼ 50 % СО;
- отвод конвертерного газа без дожигания, отвод его после в газгольдеры с последующим использованием в качестве топлива;
- применение сухих способов очистки конвертерного газа для сохранения возможности использования физической теплоты газа.
Футеровка кислородных конвертеров
Футеровку кислородных конвертеров выполняют двухслойной из рабочего и арматурного слоев и реже — трехслойной, когда между ними имеется промежуточный слой из огнеупорной смолодоломитовой массы. На отечественных заводах в настоящее время применяют двухслойную футеровку (см. рис. 1). Примыкающий к кожуху слой называют арматурным; он снижает тепловые потери и защищает кожух в случае прогара рабочего слоя футеровки. Толщина арматурного слоя составляет 110—230 мм, обычно его выкладывают из хромитопериклазового или периклазового (магнезитового) кирпича в один ряд, а арматурный слой днища — в два и более рядов.
Рабочий слой толщиной 500—900 мм на отечественных заводах выполняют из безобжиговых и иногда других огнеупоров, применяя кирпичи больших размеров — блоки. На конвертерах малой вместимости кладка может выполняться в один ряд (см. рис. 1,а), а на конвертерах большой вместимости — в два ряда с перевязкой этих рядов (рис. 1,б,в) . Футеровку рабочего слоя горловины зачастую выполняют комбинированной — низ из безобжиговых, а несколько верхних рядов из периклазо-хромитового или хромито-периклазового кирпича, поскольку последние обладают несколько более высокой прочностью при высоких температурах, чем безобжиговые огнеупоры, и лучше противостоят химико-эрозионному воздействию потока отходящих газов со взвешенными в нем частицами пыли. Для рабочего слоя летки применяют специальные леточные блоки из плавленого периклаза(МПЛК-93), имеющие сквозное круглое отверстие диаметром до 180 мм и иногда периклазо-хромитовые блоки.
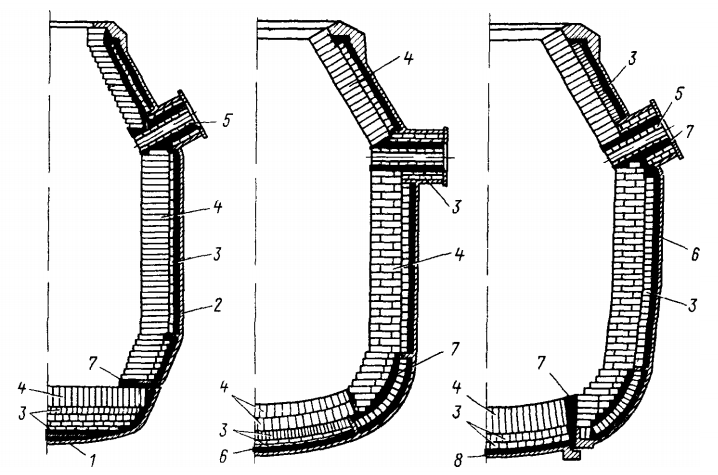
Кладка футеровки
При футеровке конвертеров с неотъемным днищем вначале выполняют кладку арматурного и рабочего слоев днища, затем цилиндрической части и далее горловины. Перед укладкой арматурного слоя для выравнивания внутренней поверхности корпуса на него наносят тонкий слой смолодоломитовой или смолопериклазовой массы (предарматурный слой).
Футеровку днищ глуходонных конвертеров выполняют несколькими способами:
- два ряда хромито-периклазовых кирпичей, укладываемых на торец всухую и затем рабочий слой в один ряд из безобжиговых изделий, укладываемых на торец;
- два ряда шамотного кирпича на плашку всухую или на растворе, ряд периклазового кирпича на плашку и ряд этого же кирпича на торец, на растворе или всухую и затем рабочий слой из одного-двух рядов изделий, укладываемых на торец (см. рис. 1,б);
- один ряд на плашку и два ряда на торец из хромито-периклазового кирпича всухую и затем рабочий слой в один ряд из изделий, укладываемых на торец. Кирпичи в каждом
ряду выкладывают вперевязку («паркетная перевязка») параллельно расположенными рядами (рис. 2,а), либо крестообразно, с расположением рядов под прямым углом (рис. 2,6). Направление кладки кирпичей в последующем ряду смещают относительно предыдущего на 45° вокруг вертикальной оси.
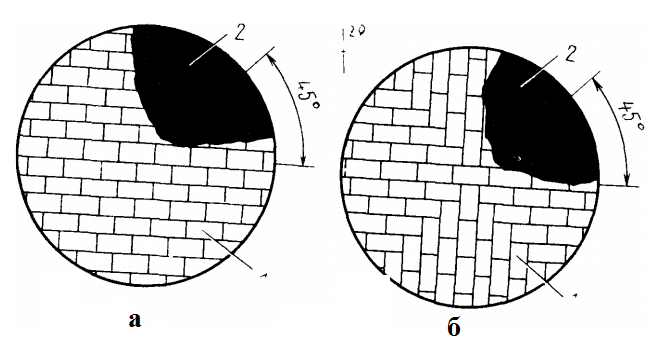
Кладку арматурного слоя цилиндрической части и горловины выполняют из хромито-периклазового или периклазового кирпича в один ряд в перевязку, так чтобы не совпадали вертикальные швы, обычно — всухую и реже — на растворе. Кладку арматурного слоя обычно ведут с опережением кладки рабочего слоя на два-три ряда.
Рабочий слой цилиндрической части выполняют из большемерных кирпичей (блоков)чаще всего в два ряда с перевязкой рядов. Последнее достигается укладкой в этих рядах блоков различной длины (рисунок 3). Рабочий слой горловины выкладывают в один ряд либоиз безобжиговых огнеупоров, либо комбинированным — нижние ряды из безобжиговых блоков, а верхние — из периклазо-хромитового кирпича. Кладку рабочего слоя цилиндрической части и Горловины ведут, укладывая блоки кольцами и иногда по спирали.
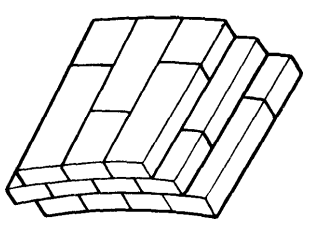
При кладке арматурного слоя насухо зазоры между кирпичами засыпают периклазовым порошком или порошком на основе MgО и Сг2O3 с крупностью зерен 2O3, делают температурные швы, устанавливая прокладки из толи или картона толщиной 1 —1,5 мм (в цилиндрической части конвертера их укладывают через пять рядов кирпича по высоте и через 5—10 кирпичей в каждом ряду; в днище несколько чаще). Рабочий слой из безобжиговых огнеупоров выкладывают без температурных швов с плотной подгонкой блоков. Зазоры в отдельных местах между рабочим и арматурным слоями заполняют смолодоломитовой или смолопериклазовой массой.
Отъемные днища футеруют отдельно от конвертера. У вставных днищ арматурный слой выполняют из двух рядов хромито-периклазового кирпича, рабочий слой — в один ряд из безобжиговых огнеупоров или хромито-периклаза (см. рис. 1,в); кладку ведут так же, как и кладку неотъемных днищ. Чтобы избежать обрушения крайних рядов кладки, их обвязывают снаружи проволокой.
У приставных днищ арматурный слой делают из трех—пяти рядов хромито-периклазового или периклазового кирпича с их укладкой на ребро или плашку, на плашку обычно выкладывают нижние ряды. Рабочий слой выполняют в один ряд из блоков, укладываемых на торец (см. рис. 1,а). После присоединения днища к конвертеру стык заполняют смоло-периклазовой массой.
При футеровке днищ, предназначенных для подачи газов в конвертер снизу, вначале выкладывают арматурные ряды, затем устанавливают фурменные устройства (блоки); патрубки фурменных блоков пропускают через отверстия, высверливаемые в кирпичах арматурных слоев. Затем заполняют пространство между фурменными блоками, причем вначале выкладывают зоны около фурменных блоков, а затем остальные участки.
Толщина швов между кирпичами или блоками не должна превышать 1 мм; при необходимости огнеупоры подвергают резке, такие огнеупоры запрещается ставить у фурменных блоков.
При футеровке летки ее кожух изнутри обкладывают слоем асбеста, затем кладут арматурный слой в один-два ряда из хромито-периклазового или периклазового кирпича. Леточные
блоки из плавленого периклаза устанавливают, насаживая на металлическую трубу, прикрепляемую к фланцу летки. Пространство между блоками и арматурным слоем набивают смолопериклазовой массой или массой из периклазового порошка, затворенного 25%-ным водным раствором сернокислого магния. Зазор между леточными блоками и рабочим слоем футеровки конвертера заполняют смолопериклазовой или смолодоломитовой массой.