Подземный транспорт и подъем
Все процессы перемещения руды из очистных блоков к месту ее отгрузки потребителю на поверхности образуют в совокупности единую систему транспортирования. Звенья этой системы — подземное транспортирование и подъем, связанные друг с другом через перегрузочные комплексы околоствольных дворов.
Подземное транспортирование руды представляет собой перемещение ее от пунктов выгрузки из очистных блоков до рудничного подъема. Подземный транспорт используют для своевременного и бесперебойного снабжения добычных участков материалами, инструментом, оборудованием и при необходимости для перевозки людей к месту работы и обратно.
На рудниках, добывающих металлические руды, используют следующий подземный транспорт:
- периодического действия (рельсовый или безрельсовый, самоходное оборудование на пневмошинном ходу);
- непрерывного действия (конвейерный).
Наибольшее распространение на подземных рудниках получил рельсовый транспорт. Это обусловлено тем, что руда представляет собой обычно крупнокусковой материал, обладающий большим удельным весом, крепостью и абразивностью.
Безрельсовое транспортирование с использованием самоходного оборудования применяется пока редко. Основной вид транспорта — автосамосвалы типа МоАЗ грузоподъемностью 20–22 т.
Ленточные конвейеры применяют только для транспортирования мелкокусковых мягких руд, например, на марганцевых шахтах. При этом нередко для вспомогательных целей приходится использовать рельсовый или автомобильный транспорт. Разработаны и проходят испытания конвейеры типа КЛТ, в которых лента уложена на лотки колесных тележек, перемещающихся по раме конвейера. Эти конвейеры могут транспортировать крупнокусковую (до 1,2 м) руду.
Рудничный подъем — выдача руды и породы на поверхность с подземных горизонтов. Он необходим только при вскрытии стволами.
По типу оборудования рудничный подъем разделяют на клетевой, скиповой, конвейерный, автомобильный, а по назначению — на главный (для выдачи руды) и вспомогательный.
Подъем руды вагонетками в одно- и двухэтажных клетях применяют на небольших рудниках с производительностью 0,3–0,7 млн т/год, а при малой глубине разработки (300–400 м) — до 1–1,5 млн т/год. Вместимость поднимаемых вагонеток при этом не превышает 4,5 м3. При клетевом подъеме требуется меньший объем проходки околоствольных выработок, чем при скиповом.
На рудниках с производительностью более 0,7–1 млн т/год и при значительной глубине разработки используют, как правило, скиповой подъем руды. Высокая производительность скипов объясняется их большей вместимостью (до 22 м3), скоростью движения (до 20 м/с и более, тогда как клети движутся со скоростью не более 8 м/с), а также полной автоматизацией погрузочно-разгрузочных операций и подъема–спуска скипов.
Конвейерный подъем применяют на сравнительно неглубоких рудниках (до 400–600 м) большой производительности (свыше 4–5 млн т/год), а при глубине разработки до 100–150 м — на рудниках с производительностью более 1–1,5 млн т/год. Как правило, применяют мощные ленточные конвейеры. Для использования конвейерного подъема необходимо сравнительно мелкое дробление руды на куски размерами не более 0,1–0,15 м. Угол наклона ствола не должен превышать 16–18°.
Автомобильный подъем руды целесообразен при глубине разработки до 150– 200 м и производительности рудника 0,5–1 млн т/год. Поэтому он применяется в нашей стране в единичных случаях. Угол наклона автомобильных стволов 6–8°.
Для вспомогательного подъема по вертикальным стволам используют то же оборудование, что и для главного. Его назначение заключается в выдаче на поверхность породы (вагонами в клетях или скипами); спуске–подъеме людей (в клетях), спуске в шахту материалов, инструмента (в клетях), спуске рабочего и подъеме неисправного оборудования (малогабаритное — в клетях; крупногабаритное — на подвеске под клетями, целиком или частями, либо на специальных грузовых платформах в неразобранном виде по отдельным стволам).
Электроснабжение горных предприятий
В подземных рудниках для привода горных машин используют два вида энергии: электрическую и пневматическую (сжатый воздух). Кроме того, для самоходного оборудования все шире применяют двигатели внутреннего сгорания, главным образом дизельные, топливо для которых при больших расходах может подаваться под землю с поверхности по трубам. Электроэнергию используют для освещения подземных выработок, зданий, сооружений на поверхности, а также для получения сжатого воздуха (рис. 6.80, 6.81).
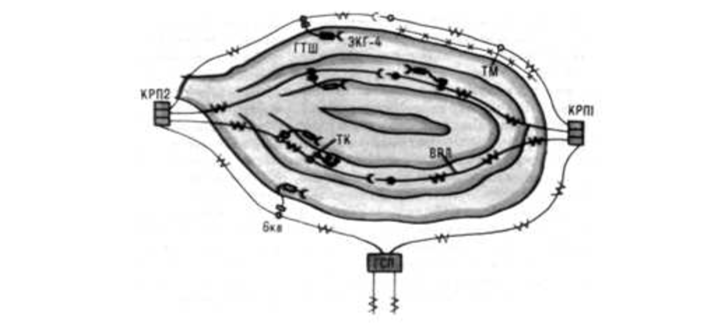
Подземные рудники при высоком уровне механизации трудоемких производственных процессов являются крупными потребителями энергии, в первую очередь электрической.
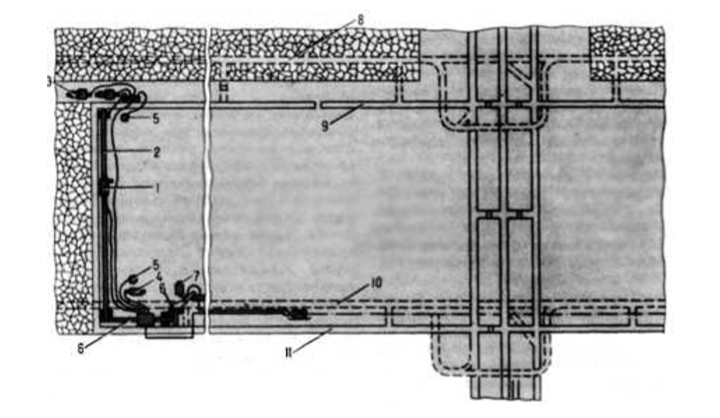
На каждый участок электроэнергию подают по отдельному кабелю — фидеру. В начале фидера для защиты шахтной электросети устанавливают автоматический фидерный выключатель, срабатывающий и отключающий участок при длительных перегрузках или коротких замыканиях. Подключение горных машин к фидеру осуществляют через рудничные пускатели. Аппаратуру, оболочки кабелей, трубы, рельсы и т. п. необходимо заземлять.
Осветительную сеть питают электроэнергией через специальные аппараты, понижающие напряжение до 220/127 В для постоянного освещения и до 36 В для переносных светильников.
Рудничный водоотлив
Водоотлив — удаление на поверхность шахтных вод из подземных выработок. Если месторождение вскрыто стволами, то водоотлив осуществляют посредством подъема воды по трубам. При вскрытии штольнями воду удаляют из рудника самотеком по канавкам.
Источники поступления шахтных вод: водоотдача насыщенных водой горных пород, фильтрация воды по трещинам из вышележащих подземных водоносных горизонтов или заполненных водой подземных пустот, фильтрация по трещинам или через зоны обрушения воды из поверхностных водоемов (рек, озер, болот и т. п.) и от атмосферных осадков.
Способы борьбы с водопритоками:
- ограждение шахтного поля от поверхностных вод;
- осушение пород, вмещающих месторождение;
- собственно водоотлив из подземных выработок;
- защита подземных выработок от затопления.
Вентиляция
Рудничную вентиляцию, или проветривание шахт, применяют для создания в подземных выработках нормальных атмосферах условий. Она должна исключить вредное воздействие на человека ядовитых газов, содержащихся в рудничном воздухе, высоких и низких температур, а также предотвратить опасные скопления вредных газов.
Рудничный воздух — смесь атмосферного воздуха и других газов, образующихся в подземных выработках или выделяющихся в них из массива.
Как известно, атмосферный воздух, окружающий земную поверхность, состоит из газов и паров. В нем на уровне моря содержится около 78,08 % азота, 20,95 % кислорода, 0,93 % аргона, 0,03 % углекислого газа и 0,01 % таких газов, как гелий, неон, криптон, озон, радон, водород и аммиак.
При прохождении по подземным горным выработкам состав атмосферного воздуха изменяется, т. к. содержание кислорода уменьшается, а углекислого газа и азота увеличивается. Кроме того, к нему примешиваются различные газы (вредные примеси), выделяющиеся в выработки из горных пород (метан, водород и др.) или появляющиеся вследствие производства взрывов, работы дизельных машин, гниения деревянной крепи и т. д.
Для получения информации о составе и состоянии рудничной атмосферы на рудниках осуществляют систематический анализ газового состава рудничного воздуха, его запыленности и температуры.
Анализ газового состава может быть оперативным и лабораторным. Оперативный анализ газового состава рудничной атмосферы выполняют с применением переносных газоанализаторов в забоях, выработках и камерах. При этом устанавливают, как правило, содержание какого-либо одного вредного газа (иногда двух-трех), наиболее опасного в условиях данного рудника. На многих рудниках ведут также систематический оперативный контроль стационарными автоматическими газоанализаторами, устанавливаемыми, например, на струе загрязненного воздуха, отводимого после проветривания из шахты. Лабораторный контроль полного газового состава осуществляют периодически на основе анализа проб шахтного воздуха, взятых в подземных выработках.
Контроль запыленности воздуха в подземных выработках ведут, используя переносные пылемеры, которые позволяют установить массовую концентрацию пыли в шахтном воздухе.
Основная мера борьбы с примесями вредных газов — разжижение их свежим воздухом до предельно допустимых концентраций, т. е. подача в забои дополнительного количества свежего воздуха.
Для борьбы с запыленностью шахтного воздуха применяют специальный комплекс мер, среди которых наиболее распространено гидрообеспыливание.
Расход рудничного воздуха, являющегося единственным источником дыхания для всех работающих под землей, ограничивается объемом подземных выработок. Так как кислород рудничного воздуха расходуется на дыхание людей, работу горных машин, окисление руд и т. д., необходимо его постоянное пополнение за счет притока свежего воздуха с поверхности.
Расход воздуха, необходимый для проветривания горных выработок, определяют по нескольким факторам.
Во-первых, по разжижению газообразных продуктов взрыва ВВ (в первую очередь СО) до безопасного содержания (0,008 %). Как уже отмечалось, при взрыве 1 кг ВВ выделяется от 700 до 1000 л различных газов.
Во-вторых, расход воздуха определяют по максимальному числу людей в выработке, исходя из нормы 6 м3/мин на одного человека.
В-третьих, учитывают суммарную мощность работающих в выработке дизельных машин. Для разжижения выхлопных газов, содержащих вредные примеси (например, угарный газ), полагается подавать 6,8 м3 воздуха в минуту на 1 кВт мощности дизельных двигателей.
В-четвертых, расход воздуха, необходимый для проветривания, определяют по пылевому фактору (по выносу пыли из забоев).
Для эффективного выноса пыли из забоя скорость воздуха должна быть не менее 0,3 м/с.
Схема проветривания — порядок распределения и движения воздуха по выработкам. Воздух подают в шахту по одним выработкам, а отводят на поверхность по другим.
На подземных рудниках наиболее часто применяют диагональные схемы проветривания, являющиеся прямоточными. При размещении вскрывающих выработок на флангах месторождения свежий воздух подают по клетевому стволу, по которому осуществляют спуск— подъем людей, или специальному воздухоподающему стволу, а загрязненный отводят на поверхность по вентиляционному стволу на другом фланге месторождения.
Все выработки и очистные забои проветривают, как правило, за счет общешахтной струи при сквозном движении воздуха. Однако тупиковые проходческие и очистные забои таким образом проветривать не удается. Если они имеют длину менее 10 м, то их проветривание осуществляют за счет диффузии (постепенного проникновения свежего воздуха в тупиковый забой). При большей длине тупикового забоя такое проветривание как неэффективное запрещено Правилами безопасности. Для подачи свежего воздуха в протяженные тупиковые забои применяют нагнетательный, всасывающий и комбинированный способ местного проветривания посредством специальных переносных вентиляторов и вентиляционных труб.
Для подачи свежего воздуха в шахту используют вентиляторные установки главного проветривания. Они располагаются на поверхности вблизи герметически закрытых устьев стволов или штолен и обеспечивают проветривание подземных выработок шахты. Установки включают в себя рабочий и резервный вентиляторы, помещенные в специальном здании, связанном со стволом или штольней вентиляционным каналом, а также устройства для реверсирования (изменения направления) воздушной струи, необходимого при авариях под землей, и устройства для подогрева (калориферы) или охлаждения (кондиционеры) воздуха, подаваемого в шахту.
Снабжение рудников сжатым воздухом
Сжатый воздух как источник энергии широко используют для привода бурильных машин, некоторых типов погрузочно-доставочного оборудования, различных лебедок вспомогательного назначения, забойных насосов, а также для продувки шпуров и скважин перед заряжанием, для их пневмозаряжания, подчистки почвы выработок у проходческих забоев и т. п. Общий расход сжатого воздуха в руднике может достигать нескольких тысяч кубических метров в минуту. Рабочее давление сжатого воздуха для большинства горных машин составляет 0,4–0,6 МПа. Сжатый воздух для нужд рудника получают при использовании компрессоров, которые устанавливают, как правило, на поверхности вблизи главных стволов в помещении компрессорных станций. На крупных рудниках применяют мощные турбокомпрессоры с подачей 250–1290 м3/мин с электродвигателями мощностью 100– 900 кВт. На средних и мелких рудниках используют поршневые компрессоры с подачей до 100 м3 /мин при мощности двигателя до 630 кВт. Подачу сжатого воздуха от компрессорных установок в забои осуществляют по трубопроводам диаметром до 0,4 м, которые опускают под землю по стволам и далее разводят по подземным выработкам. Для сглаживания пульсации давления сжатого воздуха, поступающего после компрессоров (особенно поршневых), в начале трубопровода устанавливают воздухосборники (ресиверы) — металлические баки вместимостью до 25 м3.
Технологический комплекс поверхности рудников
Рудничная поверхность, или промплощадка рудника, — спланированная и благоустроенная часть земной поверхности, на которой расположены комплекс зданий и сооружений, железные и автомобильные дороги, сети электро- и водоснабжения, канализации и т. п., необходимые для обеспечения производственной деятельности рудника (рис. 6.82, 6.83).
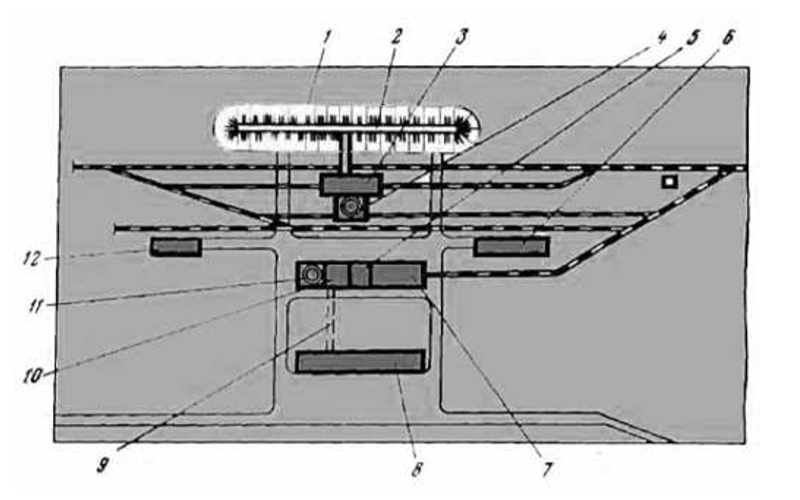
Промплощадку разделяют на зоны основного производства, транспортноскладскую, вспомогательных производств и административно-общественную. Кроме того, предусматривают резервные участки для расширения предприятия.
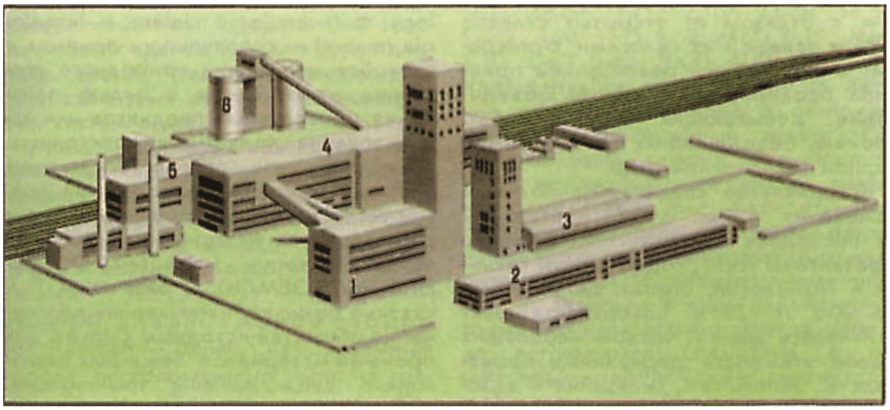
Застройку промплощадки можно осуществлять по блокированной и рассредоточенной схемам. Блокированная схема застройки отличается компактным размещением сооружений в одном или нескольких крупных зданиях.
Рассредоточенная схема застройки промплощадки, как правило, вынужденная, например, при размещении объектов рудничной поверхности в узких горных долинах или на крутых склонах.
Техника безопасности и горноспасательное дело, освещение выработок
Подземная разработка месторождений, в том числе рудных, относится к производствам с повышенной опасностью для работающих. Поэтому здесь действуют весьма строгие Единые правила безопасности при разработке рудных, нерудных и россыпных месторождений подземным способом (ЕПБ). Неукоснительное соблюдение этих правил — залог безопасной работы. Для осуществления спасательных и аварийных работ в подземных выработках созданы Военизированные горно-спасательные части (ВГСЧ), которые дислоцируются на всех добывающих предприятиях.
Подземные выработки, в которых осуществляют транспортирование руды, породы или других грузов, передвижение людей, погрузочно-разгрузочные работы, а также выработки и камеры околоствольных дворов необходимо освещать в соответствии с нормами освещенности, установленными Правилами безопасности. Для освещения используют стационарные светильники, переносные прожекторы, питающиеся от шахтной сети и имеющие защитное исполнение (пылевлагонепроницаемое или взрывобезопасное).
Шахтное самоходное оборудование оснащено прожекторами и фарами для местного освещения, питающимися от силового электрического кабеля, контактного провода или аккумулятора самой машины. Кроме того, каждый рабочий обязан иметь переносной индивидуальный светильник.