Общие положения
Ранее мы уже говорили о трех обязательных этапах освоения минеральных ресурсов недр:
- обеспечение доступа с земной поверхности к месторождению;
- придание горным породам подвижности;
- выдача полезных ископаемых и «пустых» пород в подвижном состоянии к пунктам их переработки и отвалообразования (складирования).
Новое для вещества литосферы свойство — подвижность — может быть обеспечено в рамках применяемых горных технологий либо дезинтеграцией (разрушением) этого вещества в заданном объеме, либо изменением его агрегатного состояния (например, выплавкой серы), либо путем создания условий для миграции с места залегания только полезного компонента — физических (нефть, газ, вода) или химических (выщелачивание).
Для твердых полезных ископаемых доминирующее положение занимает первый вариант и ограниченное — второй и третий. Третий же вариант является основным для жидких и газообразных полезных ископаемых.
Для дезинтеграции твердых литосферных образований применяются различные способы разрушения, различающиеся по виду используемой энергии:
- механическое разрушение;
- взрывное разрушение;
- термическое разрушение;
- электрофизическое разрушение.
На современном уровне наших знаний и возможностей в горнодобывающей промышленности в основном применяют взрывной и механический способы. Причем последний применяется в нескольких модификациях, зависящих от механизма разрушения горных пород:
- резание;
- удар;
- раздавливание;
- гидравлическое воздействие.
В горном деле в качестве объекта техногенного воздействия рассматриваются массивы горных пород и собственно горные породы.
По аналогии с геологическими терминами под массивом горных пород понимается вся их совокупность в границах месторождения или его части. В такой постановке любой массив состоит из участков, сложенных конкретными горными породами. О типах горных пород по их генезису мы уже говорили ранее.
Теперь рассмотрим свойства горных пород в связи с требованиями горных технологий, практически все показатели которых в той или иной степени определяются этими свойствами.
Поэтому среди огромного разнообразия физико-механических свойств горных пород выделяют группу «свойств геотехнологических».
Так как понятие «разработка полезного ископаемого» включает в себя широкий комплекс различных по содержанию работ, то и перечень геотехнологических свойств пород достаточно велик.
Наиболее существенными из этих свойств, оказывающих влияние на эффективность разрушения горных пород и ведения горных работ, являются строение и сложение пород, слоистость, прочность, крепость, пористость, вязкость, упругость, твердость, пластичность, разрыхляемость и др.
Горные породы состоят из минеральных частиц, связанных между собой силами молекулярного сцепления и трения. Механическая характеристика горных пород выражается формулой
τ = C + kTN
где τ — касательные напряжения на площадке сдвига; с — сила сцепления между отдельными частицами; kт — коэффициент трения (kт = tg φ ); φ — угол внутреннего трения; N — нормальная сила.
Физико-механические свойства горных пород
По строению горные породы подразделяют на связные, сыпучие и плывучие.
В связных породах минеральные частицы соединены между собой силами внутреннего сцепления. Сыпучие породы состоят из отдельных зерен, не имеющих между собой связи. Некоторые сыпучие породы при насыщении их водой приобретают свойства текучести, образуя плывуны.
Сила сцепления между частицами породы определяет устойчивость горных пород, имеющую большое значение при ведении горных работ, особенно подземным способом. Под устойчивостью понимают способность горных пород не обрушаться после обнажения их на той или иной площади. Устойчивость пород снижается при образовании в них трещин в результате высокого давления горных пород или при взрывных работах.
По степени устойчивости руды и вмещающие породы можно подразделить на следующие группы.
- Очень устойчивые — допускают обнажения снизу на площади десятков и сотен квадратных метров и не обрушаются в течение десятков лет.
- Устойчивые — допускают значительные обнажения без обрушения в течение нескольких месяцев. Выработки небольших размеров могут стоять без крепления в течение ряда лет.
- Средней устойчивости — допускают значительные обнажения на относительно короткий срок.
- Неустойчивые — требуют крепления вслед за обнажением.
- Весьма неустойчивые — совсем не допускают обнажений и, как правило, требуют применения опережающей крепи.
К наиболее устойчивым относятся вязкие породы, имеющие большую силу сцепления между частицами (кварциты, мелкозернистые граниты, окремненные известняки и пр.); к неустойчивым — мягкие и рыхлые (глины, суглинки); к очень неустойчивым — сыпучие породы (песок, осыпи) и плывуны.
Строение и физические свойства горных пород обусловливают безопасное и эффективное ведение горнопроходческих и очистных работ. Состояние и свойства пород определяют способ проведения выработок, тип и плотность крепи подготовительных выработок.
Проявление горного давления и устойчивость выработок в значительной степени зависят от плотностных, водно-физических, прочностных и деформационных свойств пород. Существенное влияние эти свойства оказывают и на технологию проведения выработок.
Основными плотностными свойствами горных пород являются плотность, объемная масса, удельный вес, объемный вес, насыпная объемная масса и пористость.
Под плотностью породы ρ понимают ее массу в единице объема за вычетом объема пор, пустот и трещин. Плотность породы измеряют в кг/м3 (иногда т/м3). Плотность каменных углей 1300–1500; песчаников, алевролитов, известняков — 2580–2800; магматических и метаморфических пород, в зависимости от содержания в них металла — от 2700 до 5000 кг/м3.
Объемная масса горной породы ρ0 — это масса в ее естественном состоянии без нарушения ее пор, пустот и трещиноватости в единице объема. Объемная масса большинства пород находится в пределах от 1300 до 4500 кг/м3, т. е. от 1,3 до 4,5 т/м3. Объемная масса каменных углей — 1300–1400; песчаников, алевролитов и аргиллитов — основных пород кровли и почвы пластов угля — 2400–2650 кг/м3. Объемная масса глин, суглинков и других пород вблизи земной поверхности равна в основном 1700–2300 кг/м3.
Понятиями плотности и объемной массы породы пользуются при оценке количества породы или добытого полезного ископаемого.
Удельный вес горной породы γ — вес единицы объема твердых частиц (минерального скелета) породы (Н/м3):
γ = gρ,
где g — ускорение свободного падения, м/с2.
Объемный вес породы ρ0 — вес единицы объема породы в естественном состоянии (Н/м3).
Понятиями удельного и объемного веса породы пользуются при оценке горного давления или нагрузки на крепь.
Насыпная объемная масса породы — масса разрыхленной породы в единице объема. Ее измеряют, как и объемную массу ρ, в кг/м3. Насыпная объемная масса ρн:
ρн = ρ/Kр,
где Kр — коэффициент разрыхления породы.
Насыпная объемная масса каменных углей 900–1000, песчаников и алевролитов 1200–1400 кг/м3.
Пористость горной породы характеризует объем пустот, имеющихся в ней. Пористость определяется делением объема пустот в породе на полный ее объем и выражается в процентах. Средняя пористость магматических и метаморфических пород составляет 0,2–3 %; известняков, песчаников, алевролитов, аргиллитов, каменных углей — 5–15 %.
Пористость породы определяет ее водопоглощение, водопроницаемость, газопроницаемость, прочность и другие свойства.
Водно-физические свойства горных пород характеризуются естественной влажностью, водопоглощением, размокаемостью, размягчаемостью и набуханием.
Под влажностью горной породы понимают массу воды, которая содержится в ней. Ее определяют по разности массы образца в естественном состоянии и массы этого же образца, высушенного при температуре 100–110 °С. Она выражается в процентах. В природных условиях залегания влажность магматических пород не превышает 2 %, каменных углей и осадочных пород — 6 %.
Водопоглощение — способность пород поглощать воду. Ее оценивают количеством воды, поглощенной породой при полном ее погружении в воду в условиях атмосферного давления. Водопоглощение прочных пород составляет от 0,3 до 6 %, мягких слабосцементированных осадочных пород — от 10 до 25 % и более.
Под размокаемостью понимают способность породы при поглощении (впитывании) воды терять связность и превращаться в рыхлую массу. Магматические, метаморфические и прочные углевмещающие породы не размокают. При взаимодействии с водой лишь снижается их прочность и другие механические свойства.
Быстро размокает большинство грунтов вблизи земной поверхности. Размокает также значительная часть углевмещающих аргиллитов на глинистом цементе.
Размягчаемость характеризует снижение прочности породы под влиянием воды. Ее оценивают коэффициентом размягчаемости, представляющим собой отношение предела прочности породы при сжатии после и до насыщения ее водой.
Набухание — способность породы к увеличению своего объема при поглощении воды. Оно проявляется у глинистых слабосвязанных пород. Набухаемость породы характеризуется величиной набухания, которая выражается относительным изменением объема или высоты образца в процентах.
Песчаники, алевролиты, аргиллиты и переслаивания этих пород набухают очень мало. Величина относительного набухания их, как правило, не превышает 0,8–1,0 %. Глинистые и другие слабосвязанные породы (грунты), залегающие главным образом вблизи земной поверхности, подразделяют по величине свободного (без нагрузки) набухания на следующие классы: ненабухающие — менее 4, слабонабухающие — 4–10, средне-набухающие — 10–15, сильнонабухающие — более 15.
Набухание глинистых пород оказывает большое влияние на их пучение и устойчивость выработок.
Прочность — свойство горной породы воспринимать внешние силовые воздействия не разрушаясь. Критерием прочности являются временные сопротивления одноосному сжатию, сдвигу и растяжению (σсж, σсд и σр).
Горные породы характеризуются различной величиной прочности на сжатие, растяжение и сдвиг. Наи-большей прочностью обладают породы на сжатие, наименьшей — на растяжение. Прочность на сдвиг (срез) занимает промежуточное положение между прочностью пород на сжатие и растяжение. Предел прочности горных пород при сжатии в 5–35 раз больше, чем при растяжении.
Показатели прочности пород на сжатие и растяжение имеют первостепенное значение для решения вопросов разрушения и отбойки их от массива в забое выработки, погрузки, транспортирования горной массы и нормирования горнопроходческих работ.
В среднем для горных пород указанные критерии прочности находятся примерно в соотношении σсж : σсд : σр = = 1,0 : 0,3 : 0,1. Прочность горных пород при объемном сжатии в несколько раз выше, чем при одноосном.
Крепость — свойство пород сопротивляться воздействию внешних усилий в процессе разрушения (при бурении, отбойке, взрывании и пр.). Количественно это свойство оценивается коэффициентом крепости ƒ, предложенным проф. М.М. Протодьяконовым.
Коэффициент крепости ƒ равен отношению временного сопротивления одноосному сжатию к единице крепости. За единицу крепости принято временное сопротивление сжатию образцов кубической формы, равное 10 МПа. Следовательно, ƒ = σсж/10.
По этому критерию М.М. Протодьяконов предложил классификацию, в которой горные породы разделены на 10 категорий. Пределы изменения коэффициента крепости от 0,3 до 20.
Существуют и другие классификации горных пород, учитывающие особенности ведения горных работ.
Абразивность — способность горных пород изнашивать контактирующие с ней поверхности режущего инструмента и деталей горных машин при работе. Абразивность пород оценивается средней потерей в массе (в миллиграммах) мерного цилиндрического стержня при истирании его в определенных условиях. По абразивности горные породы разделены на 8 классов.
Твердость — свойство горной породы сопротивляться проникновению в нее горного инструмента.
Упругость — свойство горной породы возвращаться к первоначальной форме и размерам после устранения воздействия на нее внешних сил.
Пластичность — свойство пород изменять свою форму при сохранении объема.
Хрупкость — способность горной породы разрушаться при незначительной пластической деформации.
Разрыхляемость — увеличение объема породы при выемке ее из массива. Оценивается коэффициентом разрыхления:
кр = Vв/Vм;
где Vв — объем вынутой породы; Vм — объем породы в массиве (в целике).
Коэффициент разрыхления характеризует увеличение объема породы при разрушении. Коэффициент разрыхления угля составляет 1,2–1,4; осадочных пород (песчаника, алевролита, аргиллита) — 1,4–2,2; магматических и метаморфических пород — 1,7–2,3.
Буримость горной породы — способность горной породы сопротивляться проникновению в нее бурового инструмента или интенсивность образования в породе шпура или скважины под действием усилий, возникающих при бурении. Показателем служит скорость бурения (мм/мин), иногда — продолжительность бурения 1 м шпура (мин/м). Существует классификация горных пород по буримости.
Разрушение горных пород взрывом
Взрывной способ разрушения горных пород универсален и является наиболее распространенным. В общей массе около 90 % минерального сырья добывается с помощью взрывных работ. Взрывная отбойка части горной массы от целого массива может применяться при любой крепости полезного ископаемого и вмещающих пород.
Взрывные работы применяются в тех случаях, когда механическое разрушение неэффективно. При добыче рудных полезных ископаемых и проведении горных выработок по крепким породам взрывное разрушение является единственным способом, имеющим промышленное применение.
Взрывной способ разрушения основан на применении взрывчатых веществ, при быстротечном разложении которых освобождающаяся энергия взрыва отделяет от массива и осуществляет дробление породы. Чтобы осуществить взрывное разрушение горных пород, необходимо иметь три компоненты:
- зарядную камеру (полость в породе, в которой располагается заряд);
- взрывчатое вещество (заряд);
- средства взрывания (устройства или приспособления для возбуждения химической реакции во взрывчатом веществе).
Рассмотрим каждый из этих компонентов немного подробнее.
Разрушение массивов горных пород взрывом как технологический процесс всегда начинается с подготовки зарядной камеры, т. е. полости в разрушаемом объеме горных пород, предназначенной для размещения необходимого количества взрывчатого вещества (заряд ВВ), за счет энергии которого и происходит разрушение этих пород.
По особенностям зарядной камеры в зависимости от ее формы, размеров и расположения различают следующие способы ведения взрывных работ: шпуровыми, скважинными, камерными и накладными зарядами.
Шпуровой способ взрывных работ применяют при проведении горных выработок, в отдельных случаях для отбойки угля в очистных забоях и руд в блоках при небольшой мощности рудных залежей. Шпур — продольное цилиндрическое углубление в горной породе диаметром до 75 мм и глубиной до 5 м, предназначенное для размещения заряда взрывчатого вещества. Шпуры могут быть горизонтальные, наклонные, вертикальные (нисходящие и восходящие).
Скважинный способ взрывных работ применяют при массовой отбойке руды в блоках мощных тел, а также на отрытых горных работах для разрушения пород в уступах. Взрывная скважина — горная выработка цилиндрической формы глубиной более 5 м и диаметром 75 мм, пройденная в породе способом бурения. Скважины, как и шпуры, могут быть горизонтальные, наклонные, вертикальные (обычно нисходящие).
Метод камерных зарядов применяют в отдельных случаях для отбойки руды в блоках, а также для осуществления массовых взрывов на поверхности. С этой целью проводят специальные горные выработки (например, шурф), нередко с нишами, в которых размещают сосредоточенные заряды взрывчатого вещества. Их масса может достигать нескольких тонн и даже десятков тонн.
Накладные заряды, как следует из названия, устанавливаются на наружной поверхности разрушаемого массива. Этот вид зарядов применяется очень широко, но только для вспомогательных целей (разрушение крупных кусков породы, ликвидация зависаний породы в выработках, разрушение конструкций и т. п.). Для технологического дробления горных пород этот метод не применяется. Процесс проведения шпуров и скважин называют бурением; весь комплекс этих работ, включая все вспомогательные, — буровыми работами, а машины, применяемые при бурении, — буровыми машинами.
На современном этапе развития буровых работ применяют несколько основных способов бурения: ударный, вращательный, ударно-вращательный, шарошечный, а также — в очень небольших объемах — огневой.
При ударном бурении буровой инструмент наносит удар по забою шпура или скважины и образует в нем соответствующей формы углубление — вруб. При последующих ударах буровой инструмент, будучи повернут после каждого удара на некоторый угол, постепенно разрабатывает все сечение шпура или скважины.
При вращательном бурении буровой инструмент непрерывно вращается вокруг своей оси, совпадающей с осью шпура или скважины, и одновременно подается на ее забой. При этом лезвие бура скалывает или срезает с поверхности забоя тонкий слой породы.
Кроме ударного и вращательного различают еще ударно-вращательный и вращательно-ударный способы бурения, характеризуемые одновременным вращением и ударным действием бурового инструмента. Однако при первом из них осевое усилие и крутящий момент на лезвии инструмента настолько малы, что не имеют существенного значения, и разрушение породы осуществляется, как и при ударном бурении, только за счет ударного действия инструмента. При втором же способе разрушение породы производится главным образом также за счет ударов, но сообщаемых породе, когда она находится под значительным напряжением от больших окружных и осевых усилий на лезвии инструмента. Поэтому эффективность вращательно-ударного бурения увеличивается.
При шарошечном бурении скважин инструментом является долото, имеющее несколько лап, чаще всего три лапы с пальцами-осями, на которых насажены и вращаются на шариковых опорах конические стальные шарошки с наваренными на них зубьями. Для наиболее крепких и абразивных пород конуса шарошек имеют вместо наваренных зубьев цилиндрические вставки — штыри из металлокерамических твердых сплавов типа ВК, запрессованные в тело шарошек.
При вращении долота шарошки обкатываются по забою скважины и при этом наносят удары своими зубьями или головками штырей (рис. 4.1).
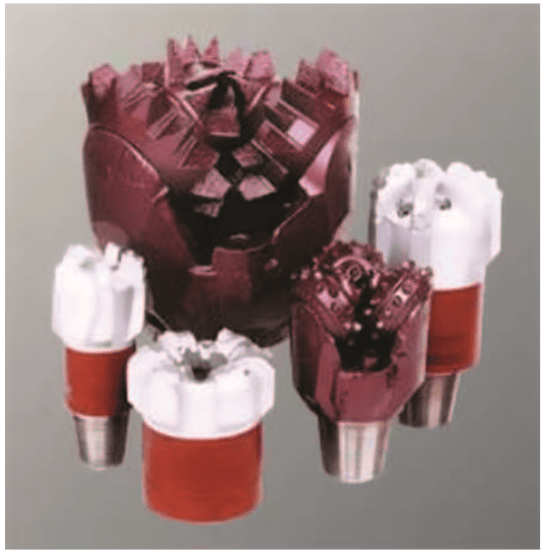
По характеру разрушения породы на забое скважины шарошечное бурение должно быть отнесено к ударному бурению. Разница между ударным и шарошечным бурением заключается только в том, что в первом случае последовательные удары по забою наносятся одним и тем же лезвием, во втором случае лезвия все время меняются. Поэтому стойкость шарошечных долот значительно выше стойкости долот обычного ударного бурения.
По характеру движения инструмента шарошечное бурение аналогично вращательному. Станки шарошечного бурения могут быть использованы для вращательного без каких-либо изменений и переделок. Поэтому в практике бурения скважин при геологической разведке, а также на нефть или на воду шарошечное бурение обычно относят к вращательному бурению, что не совсем правильно.
Очистка скважин от буровой мелочи при шарошечном бурении осуществляется водой или сжатым воздухом, подаваемыми к забою по буровым штангам через специальные отверстия в теле шарошечного долота.
Сущность огневого бурения состоит в разрушении горной породы высокотемпературной (2200 °С) газовой струей, истекающей на забой скважины из реактивной горелки, в которой сгорают керосин и окислитель (обычно кислород). Продукты сгорания имеют скорость до 1800 м/сек. Они нагревают породу; горелка вращается, и по ее периферии на забой попадается вода, которая резко охлаждает породу, от чего она трескается, и кусочки выносятся струей газа и пара.
Пока опыт такого бурения есть только на открытых работах, для которых выпускаются станки типа СБО–160/20. Но массового применения этот способ бурения пока не находит, хотя имеет вполне очевидную перспективу.
Взрывчатыми называют вещества, способные под влиянием внешнего воздействия быстро разлагаться с образованием большого количества сильно нагретых газов. Эти газы, имеющие в момент взрыва высокое давление (десятки тысяч атмосфер), разрушают породу. Таким образом, взрыв характеризуется высокой скоростью протекания реакции, образованием газообразных продуктов и выделением тепла.
Взрывчатые вещества (ВВ), применяемые в горной промышленности, представляют собой однородные химические соединения (аммиачная селитра NH4NO3, тротил С6Н2 (КО2)3СН3 и др.) или механические смеси (аммонит, динамит и др.).
Скорость взрывчатого разложения измеряется сотнями и тысячами метров в секунду. Так, аммониты разлагаются со скоростью 2000–3000 м/сек, нитроглицерин — 8400 м/сек, а дымный порох — 400–800 м/сек. Частным случаем взрыва является детонация — разложение с постоянной и максимальной для данных условий скоростью, измеряемой тысячами метров в секунду. При определенных условиях (низкая плотность, повышенная влажность) некоторые ВВ разлагаются с небольшой скоростью (несколько метров в секунду). Такое разложение называют выгоранием ВВ. При выгорании ВВ образование газов происходит медленно и разрушения породы не наблюдается.
Чем выше скорость взрывчатого разложения, тем лучше дробление породы. В горном деле применяют ВВ с ярко выраженными дробящими свойствами — бризантные. В отличие от бризантных, ВВ с относительно низкой скоростью разложения (например, порох) называют метательными.
Бризантность ВВ измеряется в миллиметрах и определяет величину сжатия свинцового цилиндра определенных размеров при взрывании на нем 50 г ВВ.
Работоспособность ВВ устанавливают взрыванием 10 г испытываемого BВ в канале свинцового цилиндра. Величина приращения объема цилиндра (выраженная в см3) и будет характеризовать работоспособность ВВ.
Бризантность и работоспособность — основные показатели, характеризующие мощность ВВ.
Кроме этих показателей в характеристику ВВ входят:
- плотность (г/см3); чем больше плотность ВВ, тем выше его эффективность, т. к. шпур будет вмещать больше ВВ;
- влагостойкость — способность не терять взрывчатых свойств в сырых условиях или в воде;
- физическая и химическая стойкость, характеризующая способность ВВ сохранять неизменными свои свойства;
- чувствительность, которая определяется величиной энергии, необходимой для взрыва ВВ.
Эта внешняя энергия называется начальным импульсом. Начальный импульс может быть тепловым (пламя, накал проводника электричеством), механическим (удар, трение) и взрывным (энергия взрыва другого ВВ). ВВ по-разному относятся к различным видам импульсов. Так, зажженный тротил в небольших количествах спокойно сгорает, а гремучая ртуть от искры детонирует. Чем выше чувствительность ВВ, тем легче вызвать взрыв, но тем опаснее данное ВВ в обращении.
Взрыв является реакцией окисления, и кислород, необходимый для этой реакции, входит в состав самого ВВ. В горнорудной промышленности обычно применяют ВВ с нулевым кислородным балансом, т. е. BB, содержащие столько кислорода, сколько его необходимо для полного окисления всех горючих элементов ВВ. При избытке кислорода (положительный кислородный баланс) или его недостатке (отрицательный кислородный баланс) образуется повышенное количество вредных газов (окиси углерода или окислов азота).
ВВ, используемые на взрывных работах в качестве основного заряда, называют промышленными. По физическому состоянию они бывают твердыми (сыпучими или монолитными) и пластичными; разновидностью пластичных являются водонаполненные (льющиеся) ВВ.
Промышленные ВВ по составу делят на: нитроглицериновые, нитроароматические и аммиачно-селитренные ВВ.
Нитроглицериновыми называют ВВ, содержащие в качестве основной составной части нитроглицерин или нитрогликоль. При обычных условиях нитроглицерин и нитрогликоль представляют собой бесцветные, маслянистые жидкости, чувствительные к удару, мощные по взрывчатым свойствам. Из нитроглицериновых ВВ допущен к применению 62 %-ный труднозамерзающий динамит, состоящий из 62 % нитроглицерина и нитрогликоля. В состав динамита, кроме того, входят: коллодионный хлопок (который, растворяясь в нитроглицерине, образует студнеобразную массу), калиевая или натриевая селитра, древесная мука, сода и мел.
Динамит негигроскопичен, обладает большой мощностью на единицу веса и особенно на единицу объема, т. к. имеет высокую плотность.
Наряду с этим динамиты имеют ряд отрицательных свойств, из числа которых следует отметить: высокую чувствительность к механическим воздействиям, что вызывает опасность в обращении; низкую химическую стойкость, характеризующуюся снижением чувствительности к передаче детонации с течением времени; эксудацию, выражающуюся в выделении при длительном хранении на оболочке патронов жидкого нитроглицерина и нитрогликоля, что повышает опасность в обращении.
Нитроароматические ВВ. Тротил (тол или тринитротолуол) — кристаллический порошок желтого цвета. Тротил малочувствителен к внешним воздействиям, влагоустойчив, обладает хорошей химической стойкостью. Он относится к сильным бризантным ВВ. В чистом виде тротил применяют на открытых работах для заряжания обводненных скважин, его используют в качестве добавок в аммиачноселитренных ВВ. При сплаве тротила с порошком алюминия получают мощное, водоустойчивое, сыпучее ВВ — алюмотол. Крупногранулированный, хорошо тонущий в воде тротил называют гранулотолом.
Гексоген — белый кристаллический порошок, используется в последнее время в качестве компонента мощных промышленных ВВ и в средствах взрывания. К этой же группе относится динитро-нафталин, сходный по своим свойствам с тротилом.
Аммиачно-селитренные ВВ. Основной составной их частью является аммиачная селитра, представляющая собой белый или желтоватый кристаллический порошок с положительным кислородным балансом, обладающий относительно слабыми взрывчатыми свойствами и низкой чувствительностью.
Аммиачная селитра гигроскопична, при хранении слеживается (уплотняется); выпускается в виде порошка, гранул или чешуек. При определенных способах приготовления (введение раствора сернокислого железа с последующей обработкой гранул смесью жирных кислот и парафина) получают водоустойчивую аммиачную селитру марки ЖВ.
Аммиачно-селитренные ВВ подразделяют на следующие группы.
- Аммониты — механические смеси аммиачной селитры с тротилом (5– 21 %). Кроме тротила иногда добавляют другие ВВ или горючие добавки (древесную муку, алюминиевую пудру и др.). В зависимости от количества и типа добавок аммониты имеют различную мощность и разные свойства. Скальные аммониты отличаются от обычных тем, что кроме тротила в их состав входят гексоген и алюминиевая пудра. Разновидностью аммонита является аммонал — водоустойчивый аммонит, содержащий алюминиевую пудру. Сходный по свойствам с аммонитами динафталит представляет смесь аммиачной селитры и динитронафталина.
- Зерногранулиты — крупнодисперсные смеси аммиачной селитры с тротилом (до 30 %).
- Детониты — порошкообразные ВВ, сходные по составу с аммоналами, но с добавками (6–15 %) нитроглицерина (нитрогликоля).
- Динамоны — смеси аммиачной селитры с горючими невзрывчатыми материалами. Гранулиты — смеси гранулированной аммиачной селитры с жидким горючим (3–5 %), обсыпанные древесной мукой или алюминиевой пудрой для предотвращения потерь жидкого горючего при хранении ВВ и транспортировании. В отличие от гранулита заводского изготовления игданит готовят на месте его применения пропитыванием селитры соляровым маслом.
- Акватолы (водонаполненные, льющиеся ВВ) представляют смесь гранулированной аммиачной селитры, тротила (до 35 %) и загустителя. При добавлении к сухим акватолам 15–20 % воды непосредственно на местах применения получают вязкую массу с консистенцией густого теста, способную заполнять взрывные камеры и вытеснять из них воду.
- Акваниты не имеют явно выраженной текучести (содержат воды 4–10 %); их консистенция зависит от температуры; по мере охлаждения акваниты густеют.
- Оксиликвиты (горючие вещества, пропитанные жидким кислородом), пороха и другие ШЗ, не получившие широкого распространения в горной промышленности, в данном курсе не рассматриваются.
Для возбуждения детонации многие малочувствительные ВВ (алюмотол, гранулотол, гранулит, зерногранулит, акватол) требуют применения промежуточных детонаторов из порошкообразного или прессованного аммонита, детонита, тротиловых или тротило-тетриловых шашек-детонаторов.
Промышленные ВВ делятся на следующие классы.
- I класс — непредохранительные ВВ для взрывания только на земной поверхности (цвет упаковки или оболочки патронов белый): гранулотол, алюмотол, гранитол марок 1 и 7А, гранулит С-6М;
- II класс — непредохранительные ВВ для взрывания на земной поверхности и в забоях подземных выработок, не опасных по скоплениям горючих газов или пыли (отличительный цвет красный): гранулит марок 79/21, АС-4, АС-4В, игданит, аммонит скальный № 3, аммонит 6ЖВ, детонит М;
- III класс — предохранительные ВВ только для взрывания пород в забоях выработок, в которых выделяется метан, но отсутствует взрывчатая пыль (отличительный цвет синий): аммонит АП-5ЖВ;
- IV класс — предохранительные ВВ для взрывания по углю и по породе в забое выработок, опасных по взрыву пыли или сотрясательного взрывания (отличительный цвет желтый): аммонит марок Т-19, ПЖВ-20;
- V класс — предохранительные ВВ повышенной предохранительности для взрывания по углю и породе в особо опасных по метану забоях подземных выработок, но в отсутствие контакта заряда с метановоздушной смесью (отличительный цвет желтый): угленит Э-6;
- VI класс — высокопредохранительные ВВ для взрывания по углю или породе в особо опасных по метану забоях подземных выработок, когда возможен контакт заряда с метановоздушной смесью (отличительный цвет желтый): угленит марок 12ЦБ, П-12ЦБ-2, патроны СП-1;
- VII класс — предохранительные ВВ для ведения специальных взрывных работ в забоях выработок, опасных по метану и угольной пыли (отличительный цвет желтый): ионит, ЗПН-1.
В угольных шахтах, опасных по взрыву газа и пыли, применяют предохранительные ВВ III–VII классов в виде патронов диаметром 36–38 мм.
Для инициирования взрыва заряда ВВ применяют взрыв небольшого по величине заряда, инициирующего ВВ, получающего внешний тепловой импульс. Инициирующие ВВ обладают большой мощностью, высокочувствительны к нагреву и механическим воздействиям. Совокупность принадлежностей, предназначенных для инициирования зарядов ВВ, называется средствами инициирования (взрывания).
Взрывчатые вещества, используемые для снаряжения средств инициирования, подразделяются на первичные (гремучая ртуть, азид свинца и тринитрорезорцинат свинца — тенерес) и вторичные (тетрил, тэн и гексоген). Взрыв первичного ВВ происходит при тепловом воздействии на него.
В зависимости от способа возбуждения взрыва средств инициирования различают следующие способы взрывания зарядов:
- огневой, при котором возбуждение взрыва капсюля-детонатора (КД) вызывается от пучка искр огнепроводного шнура (ОШ);
- электрический, при котором тепловой импульс в электродетонатор (ЭД) передается от электровоспламенителя;
- электроогневой, при котором капсюль-детонатор взрывается от пучка искр огнепроводного шнура, поджигаемого электровоспламенителем;
- бескапсюльный, при котором инициирующий импульс зарядам ВВ передается детонирующим шнуром (ДШ), взрыв которого инициируется капсюлемдетонатором или электродетонатором.
К средствам огневого взрывания относятся капсюль-детонатор (КД-85, КД8С, КД-8А), огнепроводный шнур, зажигательные патроны, зажигательный тлеющий фитиль.
Капсюль-детонатор (рис. 4.2) представляет собой небольшой заряд первичного и вторичного инициирующих ВВ, размещенный в металлической или картонной гильзе. Диаметр гильзы 6–7 мм, длина 47–51 мм. С одного конца гильза имеет открытое дульце, куда вводят огнепроводный шнур, с другого выемку, формирующую кумулятивную струю, которая усиливает кумулятивное действие. Металлическая чашечка, куда впрессовано первичное инициирующее вещество, имеет центральное отверстие для поджигания ВВ. Промышленностью выпускаются капсюли-детонаторы гремучертутнотетриловые и азидотетриловые.
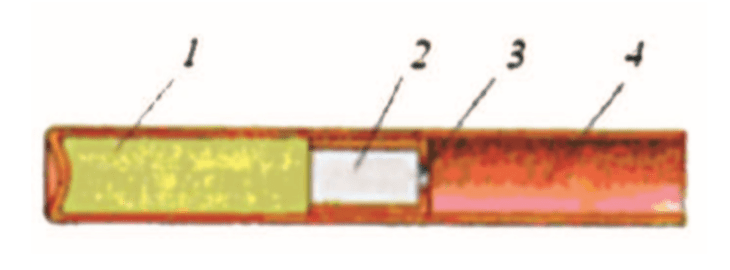
Огнепроводный шнур (рис. 4.3) представляет собой шнур с сердцевиной из прессованного дымного пороха, окруженной наружной и внутренней оплетками, покрытыми влагоизолирующим составом. Диаметр пороховой сердцевины около 2 мм, наружный диаметр 5–6 мм. В зависимости от материала внешней оболочки выпускаются шнуры марок ОША, ОШП и ОШЭ. Шнуры ОШП и ОШЭ предназначены для обводненных забоев. Скорость горения шнура 1 м/с. Шнуры выпускаются отрезками 10 м. Средства зажигания огнепроводного шнура представляют собой как специальные электрические или термические устройства, так и отрезки самого шнура. При зажигании одиночного шнура разрешается использовать спички.
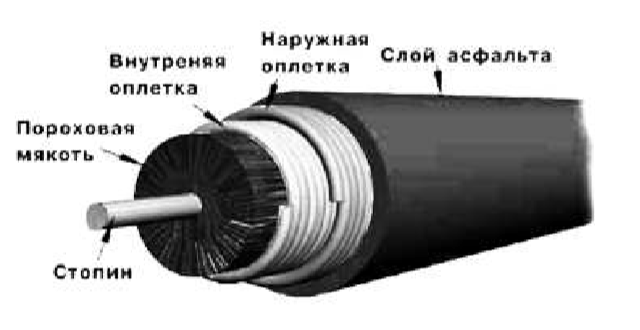
Зажигательный патрон (рис. 4.4) представляет собой картонную гильзу с лепестками, на дно которой помещают зажигательный состав.
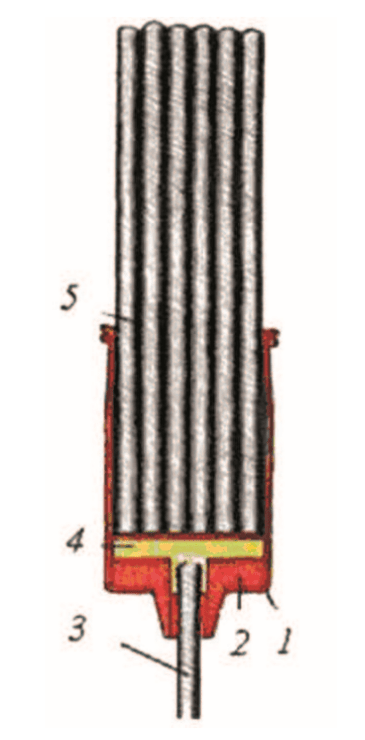
Зажигательные патроны применяются для одновременного группового зажигания 10–13 отрезков шнура. Зажигательную смесь патрона поджигают с помощью воспламеняющего шнура.
Для электрического зажигания отдельных отрезков ОШ применяют зажигательные трубки, электрозажигатели. Для зажигания ОШ также применяют тлеющие фитили и зажигательные свечи.
При электрическом способе взрывания для инициирования взрыва ВВ применяют электродетонаторы (рис. 4.5).
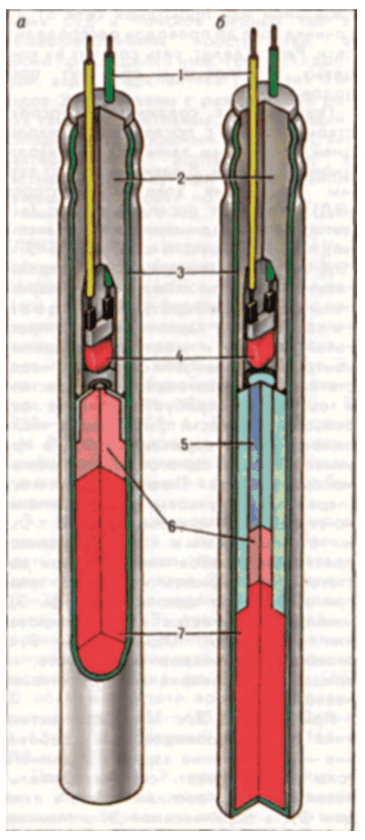
Электродетонатор представляет собой капсюль-детонатор с введенным в него электровоспламенителем. Электровоспламенитель состоит из проводников, нитей накаливания и головки воспламенительного состава.
По времени срабатывания различают электродетонаторы мгновенного, короткозамедленного и замедленного действия. Замедление достигается размещением между капсюлем-детонатором и электровоспламенителем медленно горящего состава.
Капсюли-детонаторы, непосредственно соединенные с электровоспламенителем, называются электродетонаторами мгновенного действия (ЭД-8Ж, ЭД-1-8Т).
Взрывание зарядов при помощи таких ЭД, если они включены в общую сеть, происходит одновременно и мгновенно.
Для повышения эффекта взрывных работ при проведении горных выработок взрывание зарядов в шпурах производят группами в определенной последовательности. При огневом взрывании это достигается применением огнепроводного шнура различной длины. При электрическом взрывании разновременность взрывания зарядов достигается применением электродетонаторов замедленного (ЭДЗД) или короткозамедленного (ЭДКЗ) действия. Интервалы замедления ЭДЗД: 0,5; 0,75; 1,0;,1,5; 2,0; 4,0; 8,0 и 10,0 с. Интервалы замедления ЭДКЗ: 15, 30, 45, 75, 90, 105 и 120 мс или 25, 50, 75, 100 и 125 мс.
B шахтах, опасных по газу и пыли, допускается только электрическое взрывание зарядов с предохранительными электродетонаторами мгновенного и короткозамедленного действия ЭД-КЗ-ОП, ЭД-КЗ-П, ЭД-КЗ-ПМ. Предохранительные свойства электродетонаторов достигаются нанесением на гильзу ЭД слоя пламегасителя.
При электрическом взрывании в качестве источников тока применяют конденсаторные взрывные машинки КПВ-1/100М, ПИВ-100М или электрический ток напряжением 380 В. При электрическом и электроогневом способах взрывания зарядов монтируют взрывные сети. По способу соединения электродетонаторов взрывные сети подразделяются на последовательные, параллельные и смешанные. В забоях подготовительных и очистных выработок применяют последовательное соединение. Более предпочтительным с точки зрения предотвращения отказов является переход на параллельно-последовательное соединение ЭД. До присоединения к взрывной сети провода электродетонаторов замкнуты накоротко.
Безопасное взрывание зарядов осуществляется детонирующим шнуром (ДШ). Детонирующий шнур (рис. 4.6) — шнур с сердцевиной из высокобризантного ВВ. Взрывается ДШ от капсюля-детонатора или электродетонатора. ДШ предназначен для передачи детонации от КД к заряду ВВ или от заряда к заряду. Скорость детонации ДШ 7,0 км/с. Вследствие этого взрывание зарядов происходит одновременно.
В последнее время появились принципиально новые, более эффективные системы инициирования зарядов — абсолютно безопасные (нанэль). Эти системы основаны на замене ДШ с сердцевиной из ВВ на ДШ в виде трубки с напыленным на внутреннюю поверхность слоем взрывного вещества. При возбуждении детонации в этом слое максимум давления, температуры и энергии, достаточный для инициирования заряда, создается вдоль осевой линии трубки. На стенке же трубки температура и давление почти не возрастают, что обеспечивает высокую безопасность.
Механическое разрушение горных пород
Под механическим разрушением горных пород принято понимать технологическое отделение от массива и дробление твердого вещества литосферы за счет использования механической энергии.
В современной горнодобывающей индустрии механическое разрушение горных пород производится за счет ударных нагрузок или усилий резания.
На разрушении массива за счет энергии удара основываются основные способы бурения прочных горных пород — ударно-вращательное, ударно-поворотное и шарошечное.
В результате удара инструмента по забою шпура (скважины) кинетическая энергия инструмента (энергия ударного импульса) затрачивается на дробление породы и вытеснение отделившихся частиц из образующейся лунки. Очевидно, чем большая доля энергии затрачивается на поступательное движение инструмента, тем большее значение приобретают удары для разрушения. При ударных способах бурения вследствие принудительного вращения инструмента при последующих ударах разрушаются новые участки забоя скважины.
При ударном и ударно-вращательном способах бурения разрушение породы происходит в основном в результате последовательных ударов инструмента по забою. Инструмент движется возвратно-поступательно и вращается, при этом обеспечивается разрушение породы по всей площади забоя. В машинах ударного бурения, как правило, принудительный поворот инструмента осуществляется только при его возвратном движении, поэтому такие машины иногда называют ударно-повортными.
При вращательно-ударном бурении инструмент вдавливается в породу под действием динамических нагрузок, как при вращательном способе.
Бурение шарошечными долотами может быть отнесено к ударному, если разрушение происходит только в результате перекатывания шарошки по забою, и к вращательно-ударному, если, кроме того, наблюдается скольжение зуба шарошки по забою.
Разрушение горных пород за счет усилий резания составляет основу вращательного способа бурения малопрочных горных пород, разработки этих пород экскаваторами непрерывного действия (роторными или многоковшовыми), а также комбайновой и струговой добычи горючих полезных ископаемых — углей и горючих сланцев.
В мировой практике открытых горных работ наибольшее распространение получили роторные экскаваторы, позволяющие обеспечивать большие усилия копания и высоту уступов. Эти экскаваторы отличаются высоким КПД, относительно небольшим износом элементов рабочего оборудования, универсальностью. Производительность этих экскаваторов колеблется от 200 до 19000 м3/ч при высоте уступов от 6 до 50 м.
Многоковшовые цепные экскаваторы применяются при разработке относительно мягких горных пород с удельным сопротивлением копанию до 0,6–0,7 МПа. Цепные экскаваторы, применяемые на горнодобывающих предприятиях, имеют производительность от 300–400 до 6000 м3/ч.
На открытых горных работах широко используются специализированные машины для механического рыхления горных пород. Бульдозеры используются для послойной разработки горных пород с пределами прочности на сжатие до 40 МПа.
Рыхлители на базе мощных промышленных тракторов применяются для безвзрывной подготовки к выемке и погрузке разрабатываемых горных пород с пределом прочности на сжатие до 90 МПа, а также мерзлых и трещиноватых скальных пород.
Колесные скреперы применяются для послойной разработки горных пород с пределами прочности на сжатие до 40 МПа с последующим транспортированием и укладкой этих пород.
Достаточно широко применяется механическое разрушение горных пород в процессе вторичного дробления крупногабаритных кусков, образующихся при взрывном дроблении горного массива.
Для этих целей в крановых бутобоях используют энергию удара падающего груза массой до 3–5 т.
Для дробления негабарита созданы также различные типы пневматических и гидропневматических бутобоев, выполняемых либо как стационарные установки на перегрузочных пунктах, либо как навесное оборудование к экскаваторам.
Наиболее широкое применение механического разрушения пород непосредственно на добыче полезных ископаемых имеет место в угледобывающей промышленности.
Эффективность механического разрушения угля зависит прежде всего от его прочности и крепости. Интегральным показателем усилия резания является сопротивляемость угля резанию.
Сопротивляемость угля резанию — характеристика сопротивления, оказываемая углем разрушению режущим инструментом. Показателем сопротивляемости резанию А (кН/см) является приращение силы резания на один сантиметр толщины стружки.
Между сопротивляемостью угля резанию А и коэффициентом крепости ƒ существует корреляционная зависимость вида А = 1,5ƒ.
Угольные пласты с сопротивляемостью резанию до 1,8 кН/см благоприятны для применения стругов; 1,8–2,4 кН/см — для обычных комбайнов и стругов отрывного действия с высокой энерговооруженностью; 2,4–3,6 — для очистных комбайнов высокой энерговооруженности.
Механическое разрушение при добыче угля осуществляется исполнительным органом очистного комбайна. Очистной угольный комбайн — машина, одновременно выполняющая в забое операции по отделению угля от массива, дроблению его до кусков транспортабельного размера и навалке на забойный конвейер. Угольный комбайн как выемочная машина состоит из электродвигателя, подающей части, исполнительного органа, погрузочного устройства и других узлов.
Действие исполнительных органов большинства комбайнов основано на принципе механического разрушения угля. Наиболее эффективными являются такие исполнительные органы, при работе которых в угле возникают растягивающие напряжения без образования объемного напряженного состояния.
Струговая установка — выемочная машина, предназначенная для механической отбойки, погрузки и доставки угля в очистных забоях. Исполнительным органом установки является струг. При движении вдоль забоя прижимаемого к нему струга снимается стружка угля толщиной 100–150 мм. Отбитый таким образом уголь корпусом струга грузится на конвейер. В отечественной практике струговые установки распространения не получили.
Механическое разрушение углей и пород при проходке выработок осуществляется исполнительным органом проходческого комбайна. Распространены исполнительные органы с коническими резцовыми коронками или шаровыми фрезами, установленными на стреле.
К механическому способу разрушения по сути своей относится и гидравлическое разрушение.
Гидравлическое разрушение горных пород основано на использовании кинетической энергии струи воды, выбрасываемой из гидромонитора. Считается, что эффективная отбойка происходит при напоре, развиваемом гидромонитором:
Н > 5ƒ,
где Н — напор, развиваемый гидромонитором, МПа; ƒ — коэффициент крепости угля по шкале М.М. Протодьяконова.
Гидравлическое разрушение применяют на открытых работах при разработке наносных отложений (вскрышные работы) и в отдельных случаях при подземной добыче угля. В зависимости от крепости угля применяют гидравлическое, взрывогидравлическое и гидромеханическое разрушение.
Гидромонитор — устройство, служащее для создания (формирования) плотной летящей с большой скоростью водяной струи и управления ею при размыве и отбойке полезного ископаемого или породы.
На шахтах, где осуществляется гидродобыча, для выемки угля и проведения горных выработок применяются гидромониторы, развивающие давление воды 12–16 МПа.
Наиболее широкое распространение гидравлический способ разрушения массивов приобрел при разработке рассыпных месторождений полезных ископаемых.
Кроме этих основных способов разрушения горных пород в той или иной степени готовности к массовому применению находятся разработки по использованию тепловой энергии сред разрушения горных пород за счет эффекта теплового расширения твердых тел. Здесь можно выделить также принципиальные направления:
- нагревание породы внешним источником тепла;
- нагревание породы за счет электрофизических излучений.
Эти направления представлены единичными экспериментальными работами по созданию специализированного горного оборудования с инфракрасными или высокочастотными излучателями. Полученные результаты, пока только обнадеживают технологов своими дальними перспективами, но не дают оснований для разработки полупромышленных и тем более промышленных установок.