Вакуумная индукционная плавка (ВИП) — это выплавка металлов и сплавов в вакуумной индукционной печи с керамическим тиглем.
Создание высоколегированных сплавов, представляющих результат развития современного физического металловедения, в значительной мере стимулировало разработку все более совершенных промышленных способов плавки, одним из которых, и основным, способом выплавки широкого спектра сплавов является вакуумная индукционная плавка.
Общие сведения о вакуумной индукционной плавке
Разработка концепции и технологии промышленной вакуумной индукционной плавки (ВИП) относится к началу использования реактивных двигателей, когда быстро возросла потребность в высокотемпературных материалах с повышенными свойствами и жесткими техническими требованиями. Уже в 60-х годах ХХ века были построены установки ВИП с производительностью до 30 т. Эти установки традиционной камерной конструкции весьма широко применяются по настоящее время. Использование ВИП осуществляется при производстве следующих основных видов материалов:
- сплавы, требующие особо тщательного контроля состава и содержания газов, а также растворимых примесей и нерастворимых включений;
- сплавы с химически активными элементами;
- сверхчистые материалы. Специальные сплавы, выплавляемые по технологии ВИП, в основном характеризуются следующим перечнем:
- суперсплавы для аэрокосмической промышленности и ГТД;
- сплавы на основе Ni-Co для химической промышленности;
- сплавы на основе Fe-Ni для электронной промышленности;
- сплавы цветных металлов: – медные сплавы; – сплавы Al-Li;
- редкоземельные сплавы для магнитов;
- специальные сверхпрочные сплавы;
- быстрозакаленные сплавы.
Вакуумная индукционная плавка широко применяется как основная технологическая операция в металлургическом производстве разнообразных материалов в сочетании с использованием широкого спектра технологий получения современных материалов, в том числе быстрозакаленных сплавов и методов порошковой металлургии. На рис. 1 приведена схема применения ВИП в промышленном производстве материалов и изделий.
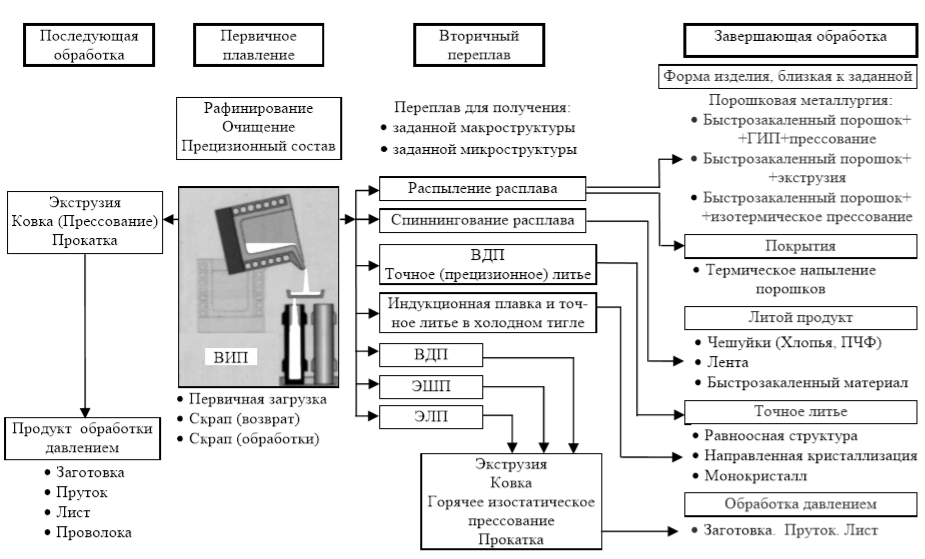
Первичное плавление, дегазация, рафинирование, очищение, достижение прецизионного состава сплава, соответствующего с высокой точностью заданному составу, осуществляются методом вакуумной индукционной плавки в традиционных камерных печах при первичной загрузке исходных компонентов (шихты) и скрапа, представляющего собой возврат (переплав литого металла) или скрап обработки (стружка и т.д.). Современные конструкции вакуумных индукционных печей типа VIDP (Vacuum Induction Degassing and Pouring Furnaces) – новое поколение печей для получения металлов и сплавов наивысшей чистоты по классической технологии вакуумного индукционного плавления. В конструкции печи применена концепция минимально возможного объема корпуса закрытой вакуумной печи с наклонным разливочным желобом, что позволило создать на ее основе промышленные горизонтальные системы непрерывного литья для слитков жаропрочных сплавов.
Последующая обработка, обычно заключается в обработке давлением полученных слитков с использованием методов экструзии, ковки (прессования), прокатки и обеспечивает производство заготовок (полуфабрикатов), прутов, листов, проволоки. Опыт применения вакуумной индукционной плавки выявил в ряде случаев проблему повышения качества слитка в связи с наличием дефектов, приводящих к низкой технологичности.
Вторичный переплав с использованием других таких современных способов плавки, как вакуумная дуговая, электрошлаковая, электронно-лучевая плавка, сопровождается повышением качества литого металла и применяется в промышленном производстве в виде дуплекс- (ВИП+ВДП) и триплекс-процессов при получении слитков никелевых суперсплавов типа ЭП741, ЭП962, ЭП975, коррозионно-стойких жаропрочных сталей.
При осуществлении переплава обычно руководствуются критериями достижения заданной макро- или микроструктуры слитка.
Последующей операцией при вторичном переплаве является обработка давлением слитка с использованием экструзии, ковки, горячего изостатического прессования и прокатки.
Вторичный переплав с использованием ВИП осуществляется также при получении быстрозакаленных сплавов, например методами бестигельного распыления расплава и его спиннингования.
Продуктом высокого качества современного металлургического производства, основанного на использовании ВИП, является точное литье.
Передовые разработки конструкций вакуумных индукционных печей для выплавки химически активных металлов обеспечили создание метода индукционной плавки и литья в «холодном» тигле, что позволило преодолеть основные ограничения традиционного метода индукционной плавки с керамическими тиглями.
Завершающая обработка предполагает использование операции вакуумной индукционной плавки при получении прекурсоров в виде быстрозакаленных порошков, фольг, чешуек, лент в аморфном, нанокристаллическом, микрокристаллическом состоянии для получения изделий методами порошковой металлургии.
Следует отметить также возможность непосредственного применения методов индукционного оплавления и распыления электрода при напылении корозионно-стойких и жаростойких покрытий.
Получение таких изделий, как лопатки ГТД, методами точного литья с применением вакуумной индукционной плавки обеспечивает формирование регламентированного типа структуры: равноосной, направленной, монокристаллической.
Завершающая обработка может заключаться в обработке давлением слитков, полученных с использованием дуплекс- и триплексметодов выплавки, путем экструзии, ковки (прессования), прокатки и обеспечивать производство высококачественных заготовок (полуфабрикатов), прутов, листов, проволоки.
Основы технологии вакуумной индукционной плавки
Исходные материалы
Основным процессом при плавке является образование однородного расплава и растворение в нем компонентов сплава. Интенсивность растворения легирующего компонента, вводимого в виде добавки, и однородность получаемого расплава в значительной степени определяются температурой плавления добавки и ее плотностью по сравнению с металлом – основой сплава.
Естественное или принудительное перемешивание расплава играет большую роль в растворении добавок, вводимых в расплав, и в получении расплава однородного состава во всем объеме, особенно если этот объем измеряется кубометрами. При лабораторных плавках и сравнительно небольшом объеме достижение однородности расплава также составляет одну из важных задач успешного осуществлении плавки.
В случаях, когда добавка более тугоплавка, чем основа, добавка в твердом состоянии будет постепенно растворяться в расплаве металла – основы. При этом, если ее плотность выше, чем расплава, она погрузится на дно ванны, в противном случае она будет плавать на поверхности. Растворение добавки и усреднение состава расплава возможны за счет свободной конвекции или принудительного перемешивания. Вклад диффузионного массопереноса, как правило, незначителен. Повышение интенсивности массопереноса можно обеспечить, удерживая добавку у поверхности в первом случае и погружая ее вглубь расплава во втором. Однако в обоих случаях надежное растворение добавки и получение однородного расплава оказывается затруднительным. В первом случае трудно визуально определить, растворилась ли полностью добавка, находящаяся на дне ванны. Во втором случае плавающая на поверхности добавка может окислиться и перемешаться в шлаке. В обоих случаях содержание добавляемого металла или элемента в расплаве окажется ниже заданного. Очевидно, что необходимо тщательное перемешивание расплава. Примером введения более тяжелой добавки может служить введение молибдена в сталь, а примером более легкой добавки – введение углерода в чугун или кремния в медные сплавы.
Когда добавка более легкоплавка, чем основной металл, но также существенно отличается по плотности, она образует жидкий слой либо на дне ванны, когда ее плотность выше, чем металла основы, либо на поверхности. Растворение в случае более легкоплавкой добавки идет заметно быстрее, чем в случае более тугоплавкой добавки, но недостаточно интенсивно, если действует только диффузионный массоперенос. Опасность нерегламентированного отклонения от заданного состава вследствие потерь добавки и неполного усреднения состава сохраняется. Принудительное перемешивание расплава снижает вероятность отклонения от заданного состава. Приведенный выше пример более легкоплавкой и тяжелой добавки характерен для введения свинца в медные сплавы, меди и никеля в стали, цинка в магниевые сплавы. Примером более легкой и легкоплавкой добавки может служить введение кремния в стали и чугуны, алюминия в медные сплавы, магния в алюминий.
Растворение вводимых добавок происходит быстрее и введение их сопровождается меньшим отклонением от заданного состава сплава, если плотность добавки и ее температура плавления близки к плотности и температуре плавления основы сплава.
В связи с этим добавки легирующего компонента вводят не в чистом виде, а в виде промежуточного сплава, обычно с основой рабочего сплава. Этот промежуточный (технологический) сплав называют лигатурой.
Содержание добавки в лигатуре обычно существенно, в несколько раз больше, чем в рабочем сплаве. Практика применения лигатур привела к целесообразности использования таких лигатур, которые состоят в основном из промежуточных фаз, что обеспечивает невысокую прочность и большую хрупкость сплавов-лигатур и позволяет легко подобрать навеску, необходимую для ввода в расплав необходимого количества легирующего компонента.
Получение лигатур является самостоятельной отраслью производства сплавов. Лигатуры получают либо прямым сплавлением компонентов, либо металлургическим путем, восстанавливая нужный легирующий компонент из его соединения с одновременным растворением восстановленного металла в основе рабочего сплава.
Лигатуры, используемые для введения различных легирующих компонентов в стали и чугуны, представляют собою сплавы на основе железа и называются ферросплавами. Существует крупное промышленное производство ферросилиция, ферромарганца, феррохрома, ферровольфрама и др., которое является самостоятельной отраслью сталеплавильного производства.
При плавке имеет место испарение металлов, поскольку равновесное давление пара металла, как правило, больше парциального давления пара этого металла в атмосфере над расплавом. С испарением металлов в значительной степени обычно приходится считаться при плавке летучих металлов, обладающих большим давлением пара при своей температуре плавления, к которым относятся Cd, Zn, Mg, Ca, Mn, Cr. При повышении температуры расплава испарение сменяется кипением, когда равновесное давление пара металла или сплава превысит общее давление в газовой фазе над расплавом. При плавке чистых металлов подобное явление почти не встречается, поскольку нет необходимости в столь высоких перегревах расплавов. Однако следует отметить, что при выплавке некоторых сплавов кипение или временное вскипание расплава является обычным процессом.
Введение магния в расплав при модифицировании чугуна (t > 1350 °С) вызывает бурное вскипание, в связи с тем, что температура кипения чистого магния равна 1100 °С. Положение усугубляется тем, что магний практически нерастворим в жидком чугуне, и поэтому он испаряется при сохранении высокого давления своих паров, определяемого температурой расплава. Подобное явление происходит при введении кадмия (tкип = 700 °С) и цинка (tкип = 910 °С) в расплавленную медь при 1150 °С. Однако эти металлы хорошо растворяются в расплаве меди, и вскипание быстро прекращается, так как давление пара будет определяться уже не чистым металлом, а раствором, и оказывается существенно меньше атмосферного.
В некоторых случаях имеет место общее закипание расплава не в процессе введения добавок, а при окончательном нагреве готового расплава перед разливкой. Типичным примером этого явления может служить поведение латуней – сплавов системы медь – цинк.
В этих сплавах коэффициенты активностей компонентов близки к единице, поэтому общее давление паров над сплавами определяется законом Рауля. Это позволяет определить зависимость температуры начала кипения сплавов от состава, т.е. температуру, при которой общее давление будет равно атмосферному. Кривая этой зависимости наиболее близко подходит к кривой ликвидуса в районе сплавов состава 40–60 % Zn. Температурный интервал между кривыми составляет здесь всего 100–150 °С, и поэтому сплавы с таким содержанием цинка закипают при весьма небольших перегревах.
Испарение металлов при плавке является нежелательным явлением, поскольку связано не только с потерями компонентов, изменением состава сплава, но загрязняет и отравляет атмосферу.
Снизить испарение металла можно за счет увеличения давления газов над расплавом. Этот способ применяют при введении добавок магния в чистом виде в чугуны для модифицирования: процесс осуществляют в специальных автоклавах под повышенным газовым давлением.
Для снижения нежелательного испарения и тем более закипания отдельных добавок при введении их в расплав также широко используют лигатуры. Поскольку в лигатуре содержание летучего компонента менее 100 %, поэтому давление пара при ее плавлении будет пониженным. Наряду с этим необходимо иметь в виду, что в лигатурах вводимый компонент нередко находится в виде промежуточных фаз и соединений. Поэтому его коэффициент активности меньше единицы, вследствие чего давление пара еще более понижается. В общем случае использование лигатур позволяет в несколько раз снизить потери летучих компонентов и, соответственно, повысить качество слитков в точности соответствия заданному составу, а также улучшить экологическую обстановку. В ряде случаев получение сплава регламентированного состава возможно только при использовании лигатуры.
В качестве примеров, когда из-за летучести легирующих компонентов и добавок используются лигатуры, можно привести примеры введения кальция для раскисления сталей, который вводят не в чистом виде, а в виде сплавов с кремнием, марганцем и другими металлами.
Необходимо отметить, что если температура плавления добавки выше температуры расплава и кроме этого поверхность добавки покрыта химически стойким и тугоплавким слоем оксидов, то ввести такую добавку в расплав, то есть растворить ее в расплаве, почти невозможно. Слой оксидов препятствует растворению и может быть настолько химически прочным, что не взаимодействует с расплавом, поскольку, будучи тугоплавким и плотным (без пор и трещин), не допускает проникновения расплава к материалу добавки.
Примером такой ситуации может служить введение хрома в расплавы меди, простых двойных латуней и оловянно-цинковосвинцовых бронз. В подобных случаях используют флюсы, которые разрушают поверхностный оксидный слой или значительно повышают температуру расплава.
Оборудование для проведения плавки
Высокотемпературные нагревательные устройства различных типов – печи, обеспечивающие плавление металла, широко распространены в металлургическом производстве.
Основная функция печи заключается в создании зоны равномерного нагрева в определенном объеме пространства и обеспечение заданного температурного режима во времени. Основными составляющими печи являются: источник тепловой энергии, камера нагрева, средства управления и контроля.
Нагрев исходных материалов – компонентов сплава (шихты), и ее плавление осуществляются в промышленности методами индукционного, электродугового, плазменного, электронно-лучевого, электрошлакового нагрева, а также пламенного нагрева при использовании, например, мартеновских печей. В лабораторной практике широко применяются косвенный резистивный нагрев с использованием печей сопротивления.
Наибольшее распространение получили электрические печи. В зависимости от способа нагрева электрические печи можно разделить на следующие типы:
- печи сопротивления;
- дуговые печи;
- плазменно-дуговые печи;
- электронно-лучевые печи;
- индукционные печи.
Индукционные печи. Этот тип печей обеспечивает высокотемпературный нагрев, хорошо регулируемый и обеспечивающий равномерный нагрев расплава в условиях его индуктивного перемешивания. Размер зоны нагрева определяется размером индуктора. Следует иметь в виду, что неметаллические и немагнитные материалы с трудом подвергаются индукционному нагреву.
Благодаря своим преимуществам индукционные печи получили широкое распространение в металлургии. Особенность конструкции индуктора состоит в том, что электромагнитная связь между индуктором и расплавом пропорциональна отношению их диаметров. Это обстоятельство создает определенные трудности при конструировании оборудования, так как приводит к необходимости уменьшать толщину тепловой изоляции между металлом и индуктором.
Для лучшего использования мощности тока необходимо, чтобы глубина проникновения, т. е. расстояние от поверхности металла (слитка, шихты), на котором плотность тока существенно уменьшается по сравнению с плотностью тока у поверхности тока, была минимальной. Глубина проникновения зависит от частоты тока и природы различных материалов. Хорошие проводники, такие, как медь, с трудом поддаются высокочастотному нагреву. Для плавки этих материалов применяют косвенный индукционный нагрев, используя обычно в качестве нагревателя графит в форме трубы или тигля. Вместо графитового нагревателя может быть использован также молибденовый нагреватель.
Индукционные печи для нагрева и плавки могут быть открытыми или закрытыми. В открытых печах в индукторе помещают слой изоляции, внутри которой располагается тигель для расплавляемого вещества. Обычно индуктор изготовляют из медной трубки, по которой циркулирует охлаждающая вода.
Закрытые печи работают в защитной атмосфере и в вакууме. В лабораторных печах этого типа индуктор может быть вынесен за пределы камеры нагрева или плавильной камеры. В этом случае корпусом печи обычно служит кварцевая трубка. Кварцевые печи легко изготовляются, но при работе в вакууме при давлении ниже 3 Па внутри кварцевого корпуса появляется блуждающий электрический разряд вследствие испарения металла и возникновения ионизированной атмосферы в печи. Это нарушает электрический режим, затрудняет измерение температуры, наблюдение и может привести к пробою корпуса. Более удобными для исследований являются печи с металлическими корпусами. В этих печах индуктор помещен внутри вакуумной камеры с водяным охлаждением.
Индукционные печи находят широкое применение для зонной очистки металлов и полупроводников, когда осуществляется локальное оплавление материала в зонной печи за счет тепловыделения, сконцентрированного в узкой зоне.
Основным недостатком индукционных печей является контакт расплавляемого металла с огнеупорной футеровкой. Устранение этого недостатка обеспечивается плавкой металла в водоохлаждаемом тигле без футеровки (плавка в «холодном» тигле). Наилучший путь решения проблемы – индукционная бестигельная плавка металла, которая осуществляется в зонной печи. Установки бестигельной плавки применяют для исследования равновесия металла со шлаком, растворимости газов в металлах, свойств жидкого металла, например плотности, поверхностного натяжения.
Однородность температуры по объему расплава является важным фактором, зависящим от конструкции печей. Теплоперенос в расплавах обычно определяется кондуктивной теплопроводностью и конвективным теплообменом. Конвективный теплообмен в жидкостях происходит вследствие свободной конвекции, протекающей за счет зависимости плотности жидкости от температуры. Cвободная конвекция может возникнуть, когда в вертикальном направлении расплава существует перепад температур. Если плотность жидкости уменьшается с ростом температуры, то в случае, когда нижние слои горячее верхних, в жидкости возникнет свободная конвекция. В случае же, когда верхние слои горячее нижних, жидкость будет неподвижна при любой разнице температур по вертикали. Такая ситуация имеет место при пламенном нагреве, так как наибольшую температуру имеют поверхностные слои расплава. Поэтому для ускорения нагрева всей ванны расплава и выравнивания распределения температуры необходимо обеспечивать его перемешивание. Для ускорения однородного нагрева всей ванны расплава применяют различные методы его перемешивания. Теплопередача в расплавах за счет свободной конвекции обычно происходит в 10–15 раз более интенсивно, чем за счет кондуктивной теплопроводности.
Наиболее интенсивное перемешивание достигается при плавке в электрических индукционных печах за счет электромагнитного воздействия на расплав. Иногда перемешивание может приобретать нежелательную интенсивность, что вызывает захват оксидов и шлака с поверхности в объем расплава.
Загрязнение расплавов и потери при плавке
Расплавленный металл обычно характеризуется весьма высокой активностью взаимодействия с теплоизолирующей облицовкой тигля. Обычно при получении расплавов высокого качества ограничиваются качественной оценкой возможных процессов взаимодействия расплава с футеровкой и атмосферой.
В общем случае необходимо учитывать, что расплав при плавке в той или иной степени будет загрязнен растворенными газами. В случае если расплав практически не растворяет газов, то следует иметь в виду возможность загрязнения частицами нерастворимых оксидов. Легкоплавкие металлы Sn, Pb, Zn, a также Bi, Cd и сплавы на их основе обычно могут быть загрязнены частицами оксидов.
При наличии в атмосфере сернистого газа, в сплавах на основе Sn, Bi, Pb может появиться примесь растворенной серы, а в сплавах на основе Cd и Zn – частицы нерастворимых сульфидов. Сплавы на основе Mg и А1 могут насыщаться растворенным водородом и загрязняться частицами оксидов. В алюминиевых сплавах при плавке в чугунных тиглях может появиться примесь железа и примесь кремния при плавке с использованием футеровки, содержащей SiO2. Сплавы Ag–Cu и Au–Ag могут насыщаться водородом и кислородом, а при наличии таких легирующих компонентов, как Sn, Zn, Al, Si, Be, Cr, – частицами и пленами оксидов этих металлов и элементов.
В сплавах на основе Ni и Fe в зависимости от условий плавки может изменяться содержание кислорода, водорода, азота, углерода. Сплавы, содержащие Al, Ti, Cr, могут загрязняться оксидами этих металлов. При превышении содержания примеси кислорода выше определенного уровня в расплаве могут появиться жидкие включения, состоящие из сплавов оксидов SiO2, MnO, FeO, NiO.
Особенностью плавки тугоплавких металлов является активное разрушение любых огнеупорных материалов. Поэтому тугоплавкие металлы плавят в электрических печах, снабженных кристаллизаторами (изложницами или тиглями), обычно имеющими медные водоохлаждаемые стенки, что не исключает возможности появление примеси меди в поверхностных слоях слитка.
При плавке металлов обычно образуется естественный шлак, который представляет собой сплав оксидов элементов, входящих в состав выплавляемого сплава. Эти оксиды частично находятся на поверхности исходных металлов, подлежащих плавке, частично образуются при взаимодействии расплава с кислородом атмосферы.
Образующийся при плавке шлак может быть твердым, жидким и творожистым (частично жидким – двухфазным) в зависимости от температуры расплава. При плавке легкоплавких металлов (от Sn до Аl), как правило, шлак твердый, при плавке меди и ее сплавов – частично жидкий, при плавке никелевых и железных сплавов – жидкий.
Следует иметь в виду, что при плавке в вакуумных печах естественного шлака почти не образуется, так как обычно используется чистая шихта и окисление расплава не происходит.
В связи с тем, что жидкие металлы обычно взаимодействуют с кислородом и другими газами атмосферы, при плавке на воздухе возникает необходимость в защите расплава. При открытой плавке практически невозможно получить сплав заданного состава с точно регламентированными допусками по легирующим элементам. Следует иметь в виду, что в некоторых случаях при выплавке сплавов, не растворяющих кислород, плавка без защиты расплава также невозможна. Например, жидкий магний и его сплавы при плавке без защиты загораются, если температура превышает 660–670 °С.
Для осуществления плавки в атмосфере воздуха обычно широко используют различные защитные покровы в виде жидких шлаков и флюсов, а также специальные сыпучие материалы. Шлак, используемый для защиты расплавов от взаимодействия с воздухом, обычно представляет собой сплав оксидов. Флюсом называют жидкий защитный слой, представляющий в основном сплав солей. Жидкий защитный покров в общем случае должен иметь температуру перехода в жидкое состояние более низкую, чем температура начала плавления расплава примерно на 100 °С. Необходимо, чтобы флюс или шлак не только хорошо растекался по поверхности расплава, но и покрывал сплошным слоем твердый металл в начале плавки. Защитный слой флюса должен быть непроницаем для кислорода и азота, т.е. эти газы не должны растворяться в защитном шлаке или флюсе. Защитный покров не должен взаимодействовать с расплавом и вызывать по этой причине изменения в составе сплава. Желательно также, чтобы жидкие защитные покровы не взаимодействовали с огнеупорной футеровкой.
В качестве защитных шлаков при плавке сталей и вообще сплавов на основе железа используются шлаки, основанные на системе CaO–SiO2 с различными добавками: FeO, MnO, MgO, Аl2О3, CaF2, CaC2. Для предотвращения разрушающего действия защитного шлака на огнеупорную футеровку необходимо, чтобы основность шлака была близка к основности футеровки.
Оксидные сплавы системы CaO–SiO2 практически не растворяют кислород и азот, поэтому эти оксидные шлаки непроницаемы для данных газов. Проницаемость оксидных шлаков для кислорода определяется содержанием в них оксидов железа и марганца.
Для медных сплавов используют более легкоплавкие шлаки на основе силиката натрия (75% SiO2 + 25% Na2O), плавящегося при 900 °С. Этот силикат хорошо растворим в воде и его водные растворы (жидкое стекло, силикатный клей) используют как связующий материал для изготовления литейных форм и стержней.
Алюминиевые сплавы, в общем случае, не требуют защитных покровов при плавке, так как образующаяся на поверхности расплава плена оксида алюминия хорошо защищает расплав от дальнейшего окисления.
Однако защитный покров необходим при переплавке стружки алюминия, мелких отходов, когда велика окисляющаяся поверхность. Это могут обеспечить защитные составы, плавящиеся при температуре 450–500 °С. Оксидные смеси, удовлетворяющие этим условиям отсутствуют, и поэтому используют солевые составы – флюсы. Основой флюсов для плавки алюминия обычно является карналлит – природный минерал, представляющий собою двойную соль КСl·MgCl2 и плавящийся при 480 °С. В состав флюса вводят также NaCl, CaF2 и другие хлориды и фториды.
Кроме жидких защитных покровов используют твердые материалы, предотвращающие доступ кислород воздуха к поверхности расплава. При плавке меди и некоторых ее сплавов для этой цели традиционно применяют древесный уголь, который, находясь на поверхности расплава и непрерывно сгорая, создает атмосферу из оксидов углерода над расплавом. Эти газы, не взаимодействуя с жидкой медью, создают защитный газовый покров.
Надежный способ защиты расплавов от взаимодействия с воздухом заключается в проведении плавки в защитной или инертной атмосфере или в вакууме.
Выбор защитной атмосферы для плавки можно сделать на основании данных по термохимии образования возможных продуктов взаимодействия расплава с используемой атмосферой.
В вакууме массо- и теплоперенос изменяется от конвективного к диффузионному. На основе термохимического подхода вакуум определяется давлением, которое меньше давления диссоциации рассматриваемого химического соединения. В этом случае понятие «вакуум» как определенный уровень давления будет различным для разных веществ.
В технологии выплавки металлов и сплавов давление от 105 до 133 Па (1 мм рт. ст.) считается пониженным по сравнению с атмосферным. Давление 0,1–13 Па характерно для «плохого» вакуума; давление 10-3–10-1 Па соответствует нормальному или «хорошему» вакууму; 10-5–10-3 Па – «высокий» вакуум; -5 Па – «сверхвысокий» вакуум. В общем случае вакуум характеризуется величиной остаточного давления, при этом существенным является вопрос о том, какие газы определяют это остаточное давление. Обычно остаточное давление создают азот, кислород, углекислый газ и углеводороды диффузионного масла, используемого в паромасляных вакуумных насосах.
При проведении вакуумной плавки необходимо определить, какие соединения расплавляемых металлов являются неустойчивыми при заданном остаточном давлении и рабочей температуре. Определение условий предотвращения образования свободного оксида металла осуществляется обычно в предположении, что остаточное давление обусловлено давлением кислорода, а сам металл и его оксид имеют пренебрежимо малое давление паров по сравнению с остаточным давлением в вакуумной установке.
Опыт плавки и оценочные расчеты показывают, что вакуумная плавка при остаточном давлении 100–200 Па обеспечивает практически полное удаление из обычных металлических расплавов примеси водорода, а расплавы на основе железа и никеля очищает также от примеси азота. При остаточном давлении, равном 1 Па, чистая жидкая медь не только не окисляется, но содержание кислорода снижается ниже 10-3 %. При плавке под остаточным давлением ~ 10-3 Па аналогичное явление наблюдается для Ni, Fe, Mo, W. Для того чтобы избежать окисления при плавке таких активных металлов, как Ti, Zr, V, Nb, остаточное давление должно быть менее 10-5 Па. Наконец, чтобы при плавке не окислялся алюминий, остаточное давление должно быть менее 10-8 Па. Обычный уровень остаточного давления при вакуумной плавке сплавов на основе Ni, Fe, Ti составляет ~ 10-1 Па, при плавке Nb, Та, Mo, W ~ 10-3 Па.
Одной из главных проблем при вакуумной плавке металлов является испарение, вызывающее общие потери металла, а также приводящее к изменению состава сплавов вследствие неодинаковой скорости испарения разных компонентов.
Испарение при вакуумной плавке обычных металлов составляет заметную, но сравнительно небольшую величину. Например, при вакуумной плавке титана Т = 2000 К, если площадь испарения (площадь зеркала расплава) равна 0,02 м2, время плавки 1 ч, то потеря массы расплава составляет ~ 100 г. В случае, когда выплавляемый металл имеет высокое давление пара, т.е. является летучим, испарение становится недопустимо интенсивным. Например, хром характеризуется давлением пара при Т = 2250 К равным 2000 Па и скорость испарения составляет ~ 2000 г/(м2·с). Столь большая величина предопределяет большие потери металла на испарение и в связи с этим большой расход энергии. При попытке вакуумной плавки хрома подводимая электрическая энергия затрачивается на сублимацию и образование жидкой ванны не происходит.
Таким образом, при использовании вакуумной плавки необходимо предварительно оценить возможную скорость испарения основы сплава, всех легирующих компонентов и разных примесей. Сплавы на основе летучих металлов (Cd, Zn, Mg, Ca, Mn, Cr) вообще невозможно подвергать вакуумной плавке. В подобных случаях (например, хром и его сплавы) плавку осуществляют в атмосфере инертного газа – аргона.
Основные технологические операции и физико-химические процессы при плавке
Нагрев, плавление, перегрев
При плавке исходные материалы обычно нагревают до температур образования расплава и перегревают его до температуры, при которой расплав можно заливать в литейные формы, чтобы получать высококачественные отливки. Эта температура, называемая температурой заливки, обычно превышает температуру начала кристаллизации сплава на 50–200 °С. С повышением температуры начала кристаллизации расплава разница между температурами заливки и начала кристаллизации возрастает. Это обусловлено тем, что с ростом температуры начала кристаллизации сплава увеличиваются теплопотери за счет усиления естественной конвекции окружающего воздуха и за счет излучения. В случае легкоплавких сплавов на основе олова, свинца, цинка температура заливки превышает температуру начала кристаллизации расплава всего на 50– 70 °С, а для сплавов на основе меди, никеля, железа это превышение должно быть не менее 100–150 °С и может доходить до 200 °С.
В некоторых случаях расплавы специально перегревают до еще более высоких температур, чтобы воздействовать на состояние расплава с различными включениями и примесями, и за счет этого получить в отливке качественную структуру с допустимым содержанием различных примесей и включений. После перегрева и оптимальной выдержки расплав охлаждают в печи или специальной емкости (миксере, ковше, тандише) до температуры заливки и после этого заливают в литейные формы.
Классификация примесей в расплаве
В общем случае расплавы, получаемые при плавке, могут содержать в качестве примесей растворенные газы (кислород, азот, водород), растворенные металлы и элементы, часть которых привносится исходными материалами, а часть появляется в ходе плавки. Кроме того, в расплаве формируются нерастворимые частицы (неметаллические включения) главным образом оксидной природы, но могут быть карбиды, нитриды и сульфиды. Неметаллические включения обычно имеют размеры от субмикронных (наноразмерных
Наиболее детально изучены неметаллические включения в сталях и алюминиевых сплавах.
В применении к сталям предложена классификация неметаллических включений, основанная на температуре их образования относительно температуры кристаллизации самого расплава. Первичные докристаллизационные включения – такие включения, которые присутствуют в расплаве при любых температурах. Типичные неметаллические включения подобного типа – частицы оксида алюминия Аl2О3. В легированных сталях и сложных сплавах на основе железа и никеля, содержащих алюминий и титан, нередко имеются первичные докристаллизационные включения, представляющие собою сложные соединения на основе карбонитридов титана и алюминия. Вторичные докристаллизационные включения существуют в расплаве ниже некоторой температуры, выше которой они полностью растворяются в расплаве. Примером таких включений являются частицы кремнезема SiO2, которые образуются в железном расплаве, содержащем растворенные кислород и кремний. Третичные кристаллизационные включения образуются непосредственно в ходе кристаллизации металла. При выплавке стали – это сложные оксисульфиды железа и марганца. Четвертичные неметаллические включения появляются в твердом металле вследствие снижения растворимости кислорода, серы, фосфора и представляют собой частицы оксисульфидов, сульфидов, фосфидов.
В алюминиевых сплавах неметаллические включения представлены главным образом пленами оксидов алюминия и магния и являются первичными докристаллизационными. В бронзах и латунях наблюдаются также первичные докристаллизационные неметаллические включения в виде частиц оксидов легирующих компонентов.
По механизму образования неметаллические включения делят на экзо– и эндогенные. Экзогенные включения представляют собой включения, попавшие в расплав извне, например из разрушенной огнеупорной футеровки или замешанные в расплав частицы твердого шлака на поверхности расплава. Эндогенные неметаллические включения образуются в расплаве. Неметаллические включения в сталях, согласно данной классификации, являются в основном эндогенными. Часть первичных докристаллизационных неметаллических включений в сталях следует считать экзогенными. В алюминиевых сплавах неметаллические включения практически полностью экзогенные.
Содержание нерастворенных включений в расплаве обычно сравнительно невелико (по массе 5 частиц в 1 см3 металла.
Дегазация расплава
Очистка металлических расплавов от растворенных газов, в частности водорода и азота, называется дегазацией. Удаление из расплавов кислорода называется раскислением. В металлургии этот процесс широко применяется и занимает особое место, в частности при выплавке металлов и сплавов, и обычно рассматривается отдельно.
Дегазация расплавов может быть осуществлена различными способами, основанными на общих закономерностях взаимодействия жидких металлов с газами. Наиболее простой способ дегазации «вымораживание» основан на явлении уменьшения растворимости газов при понижении температуры и неизменном давлении (рис. 2.1).
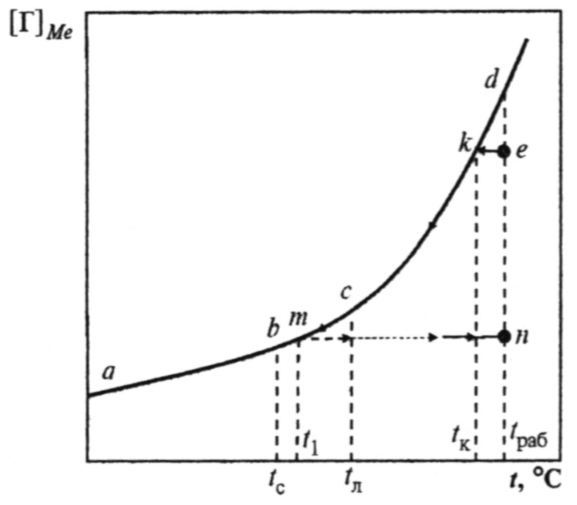
Повышение растворимости газа с повышением температуры расплава некоторого сплава при постоянном давлении на этом графике характеризуется кривой abd, температуры ликвидуса и солидуса выплавляемого сплава обозначены соответственно tл и tс.
Сущность способа заключается в тепловой (температурновременной) обработке расплава путем изменения его температуры согласно следующей технологии.
При плавке сплав нагревают до температуры tраб, при которой в расплаве возможно достижение наибольшего содержания газа, определяемое точкой d. Обычно расплав не насыщен газом до этого предела, так что можно принять, что содержание газа в нем соответствует точке е. Ордината точки е значительно больше – примерно в 3 раза, чем ордината точки b, соответствующей равновесному содержанию при температуре солидуса tc. В связи с этим при охлаждении расплава и последующей кристаллизации его возможно возникновение газовой пористости вследствие выделения растворенного газа в виде пузырьков.
Способ «вымораживания» заключается в медленном охлаждении расплава прямо в печи с температуры tраб до температур частичной кристаллизации расплава, т.е. до температур более низких, чем tк, при этом содержание газа в расплаве снижается по участку кривой kcb и становится возможным выделение газа из раствора. Выделение газа может происходить либо через открытую поверхность, либо за счет образования пузырьков в расплаве. В обоих случаях требуется определенное пересыщение, так что имеющаяся концентрация газа в расплаве будет несколько больше, чем равновесная. В связи с тем, что замедленное охлаждение расплава ведут вплоть до температур частичной кристаллизации расплава, т.е. ниже температуры ликвидуса tл, например до температуры t1, содержание газа в расплаве определяется точкой m.
После этого расплав по возможности быстро нагревают до рабочей температуры tраб. При этом повышение содержания газа в расплаве происходит незначительно (до точки n, см. рис. 2.1), поскольку нагрев совершается быстро и так как обычно атмосфера в печи уже не содержит влаги или атомарного азота, водорода, которые определяли первоначальное газонасыщение при плавке. В результате в расплаве достигается снижение содержания растворенного газа, так что выделение его из расплава при последующем охлаждении и кристаллизации практически устраняется.
Дегазация металлических расплавов часто осуществляется путем продувки расплавов инертными или активными газами, а также обработкой расплавов летучими соединениями (главным образом, хлоридами). Эти способы дегазации расплава основаны на диффузии растворенного газа из расплава в пузырьки, образованные продуваемым газом, где парциальное давление растворенного газа вначале практически равно нулю, а затем приближается к равновесному, определяемому остаточным содержанием газа в расплаве.
Удаление газа из расплава возможно и без продувки, через свободную поверхность при выдержке расплава в атмосфере, где парциальное давление растворенного газа меньше равновесного, определяемого его содержанием и температурой. Однако ввиду малой интенсивности массопереноса, зависящей от диффузии газа через поверхность раздела расплав–газ, на практике значительное увеличение поверхности раздела расплав–газ достигается при продувке, когда газ подается в расплав в виде пузырьков диаметром 1–2 мм, что обеспечивается применением различных пористых насадок на рабочем патрубке (фурме).
При дегазации расплавов продувкой газами или обработкой летучими веществами важным фактором является содержание примесей в используемых газах и веществах, главным образом влаги, азота, кислорода. Возможность применения данного газа для продувки определяется содержанием водорода и азота, которое должно быть меньше в 3–4 раза, чем содержание их в расплаве.
Следует отметить, что существует определенный предел размеров продуваемых пузырьков в случае, если газ недостаточно чист. При очень малом размере пузырьков капиллярное давление в них существенно возрастает: ркап = 2σ/r, где σ – поверхностная энергия на границе расплав–газ, r – радиус пузырька. В связи с этим парциальные давления вредных примесей (влаги, кислорода) могут достичь столь большой величины, так что примеси газов из раствора-расплава не смогут переходить в пузырьки продуваемого газа.
Для продувки сталей, чугунов, медных и алюминиевых сплавов целесообразно использовать инертный газ аргон высшего сорта с содержанием примесей кислорода 3. Для нелегированных чугунов, медных и алюминиевых сплавов возможно применение азота особой чистоты или высшего сорта с примесью кислорода 3. Алюминиевые расплавы нередко продувают азотом с добавкой ~ 10–20 % хлора. Полезное действие хлора заключается в разрыхлении и разрушении оксидной пленки на поверхности образующегося пузырька и облегчении перехода водорода из расплава в пузырек. Следует отметить, что «кипение», наблюдаемое в основном при производстве кипящих сталей, происходящее за счет выделения пузырьков монооксида углерода, может рассматриваться как продувка расплава, приводящая к существенному снижению содержания водорода и азота в расплаве.
Дегазация может осуществляться также обработкой расплава летучими хлоридами. Для этой цели используются МnСl2, ZnCl2, AlCl3, NH4Cl.
Возможный способ удаления растворенных газов (водорода, азота) из металлического расплава заключается в его кипячении. Этот способ теоретически применим для любых металлов и сплавов. Он основан на том, что в случае постоянного общего давления над расплавом, равного, например, 1 атм при достаточно низких температурах расплава, когда давление пара расплавленного металла ничтожно мало, общее давление будет определяться давлением растворенного в расплаве газа, которое соответствует достаточно высокому содержанию этого газа в расплаве.
При повышении температуры расплава давление пара металла растет, соответственно снижается давление растворимого газа, поскольку общее газовое давление под расплавом постоянно – 1 атм. Когда давление пара металла достигает 1 атм, т. е. достигается температура кипения и расплав закипает, давление растворенного газа должно снизиться до нуля и, соответственно, содержание растворимого газа становится равным нулю, т. е. происходит полная дегазация расплава.
Этот способ рафинирования расплавов реализуется при работе со сплавами, содержащими значительные количества низкокипящих легирующих компонентов. Так, латуни – медные сплавы, содержащие 20–40 % цинка, в случае плавки при атмосферном давлении закипают при 1150–1250 °С. Происходит бурное выделение паров цинка, что приводит к полной дегазации расплава.
Наиболее распространенный способ дегазации металлических расплавов или рафинирования от растворенных газов заключается в их вакуумировании, несмотря на необходимость сложного технологического оборудования – вакуумных камер, насосов, измерительной аппаратуры.
Процессы дегазации вакуумированием основаны на зависимости содержания растворенного газа в расплаве от его давления над расплавом, обычно согласно закону Сивертса [Г] = k√PГ2.
Понижение внешнего давления над расплавом, содержащим растворенный газ, способно вызвать гомогенное появление пузырьков этого газа из-за возникающего пересыщения жидкого раствора. Снижение внешнего давления обеспечивает наиболее эффективную дегазацию расплава как за счет образования пузырьков в объеме расплава, так и за счет удаления газа через свободную поверхность расплава.
Следует отметить существенное влияние на процесс дегазации гетерогенного механизма образования газовых пузырьков в пересыщенном расплаве. Наличие в пересыщенном газом расплаве частиц, для которых межфазная энергия границы включение–газ меньше, чем границы включение–расплав, приводит к появлению на них газовых пузырьков с краевым углом смачивания θ
Особый интерес представляет наличие трещин в инородных включениях. При условии, что межфазная энергия на границе включение–газ меньше, чем на границе включение–расплав, трещины могут быть заполнены газом. Капиллярное давление в данном случае способствует образованию пузырька газа.
Гетерогенное или гомогенное образование, соответственно, «сидящего» на поверхности включения или «свободного» пузырька достаточно малого радиуса r0 может оказаться невозможным из-за того, что расчетное давление в нем по Лапласу, равное 2σ/r0, будет выше давления, обусловленного содержанием газа в пересыщенном растворе.
Снижение содержания растворенных газов при плавке газонасыщенных расплавов под шлаками и флюсами, используемыми для очистки расплавов от взвешенных включений, определяется тем, что при удалении из расплава включений, имеющих полостипузырьки, заполненные газами, достигается снижение содержания растворенных газов. В отдельных случаях такой прием используют именно как способ дегазации.
Экспериментальные исследования и производственный опыт свидетельствуют о том, что процессы газонасыщения металлических расплавов, их дегазация и очистка расплава от нерастворимых включений взаимосвязаны. Однако конкретные закономерности этой взаимосвязи и их трактовка являются предметом дальнейшего изучения металлургии плавки.
Раскисление расплава
Раскисление металлических расплавов представляет собой удаление из них растворенного кислорода. Раскислению подвергают расплавы, в которых кислород присутствует в растворенном виде. В связи с этим при плавке обычно раскисляют железо и его сплавы с небольшими количествами углерода, сплавы систем железо–никель, никель–медь, медь и т.п. В то же время сплавы на основе алюминия, магния, цинка, олова, в расплавах которых кислород присутствует в виде оксидных включений, т. е. в связанном виде, не раскисляют, хотя химический анализ может показывать заметное содержание кислорода в сплаве. В этих случаях применяют рафинирование, т. е. операцию очистки расплава, основанную на других физико-химических процессах.
Раскисление можно осуществлять несколькими способами. Наиболее распространенным способом является глубинное, или осадочное, раскисление, при котором в расплав, содержащий растворенный кислород, вводится элемент-раскислитель, образующий соединения с кислородом (оксиды), нерастворимые в расплаве. Отличительной особенностью осадочного раскисления является то, что этот процесс приводит к загрязнению расплава продуктами реакции в виде частиц оксидов, являющихся типичными эндогенными докристаллизационными включениями, удаление которых из расплава требует проведения соответствующих технологических операций.
Указанного недостатка лишено так называемое диффузионное, или контактное, раскисление, при котором кислород переходит в специально наводимый на расплав шлак в виде оксида расплавляемого металла, либо связывается на поверхности нерастворимого твердого раскислителя в оксид, также нерастворимый в расплаве. Диффузионное раскисление через шлак широко применяется в металлургии стали так же, как и глубинное (осадочное) раскисление добавками марганца, кремния, кальция, алюминия.
Раскисление с помощью нерастворимых раскислителей применяется к медным и серебряным расплавам. В этих случаях в качестве раскислителя используют углерод в виде графита, древесного угля. Раскисление осуществляется по реакции, продуктом которой является газообразный монооксид углерода, пузырьки которого уходят из расплава в атмосферу.
Для некоторых сплавов возможно раскисление при плавке в достаточно глубоком вакууме. В этом случае необходимо, чтобы остаточное давление в вакуумной камере было в несколько раз меньше равновесного парциального давления кислорода, определяемого требуемым его содержанием в расплаве.
В литейном производстве используют в основном глубинное, или осадочное, раскисление.
Отделение нерастворимых частиц наиболее эффективно происходит, если частицы шарообразны, что обычно имеет место, если продукты раскисления находятся в жидком состоянии. Обеспечение жидкого состояния продуктов раскисления достигается одновременным применением различных раскислителей, когда их оксиды способны взаимно сплавляться, в чем и состоит другая положительная сторона применения комплексных раскислителей.
Важность достижения жидкого агрегатного состояния продуктов раскисления наглядно проявляется на примере раскисления сталей, которые не раскисляют только чистым алюминием, хотя он способен сильно понизить содержание кислорода. Однако при этом расплав интенсивно загрязняется твердыми трудно удаляемыми частицами оксида алюминия, что приводит к резкому снижению пластичности металла. В связи с этим стали вначале раскисляют марганцем, кремнием, комплексными раскислителями и только перед самой разливкой или даже непосредственно при разливке прямо в струю расплава подают небольшое количество алюминия для связывания остатков кислорода.
Выбор раскислителей, определение их количества и способа введения в расплав зависят от состава сплава, набора исходных шихтовых материалов, применяемого плавильного оборудования.
Раскислители представляют собой активные по отношению к кислороду и нередко летучие элементы, поэтому для их введения применяют лигатуры. Кремний и марганец вводят в виде ферросплавов, кальций – в виде сложного сплава кремний–марганец– кальций, только алюминий для раскисления сталей используют в чистом виде. Следует отметить, что удаление растворенного кислорода из углеродистых сталей, т.е. их раскисление, в определенной мере происходит в процессе фильтрования расплава.
Сущность этого явления заключается в следующем. Введение в расплав раскислителей сопровождается химической реакцией с выделением новых фаз – продуктов раскисления. Образование новых фаз в расплаве требует определенного пересыщения и происходит в течение некоторого времени. В процессе фильтрования, когда расплав протекает через поры фильтрующего материала, имеет место интенсификация гетерогенного механизма зарождения продуктов раскисления, если материал фильтра выполняет роль готовых центров образования оксидных фаз – продуктов раскисления, в частности, если он обладает соответствующей кристаллической структурой.
Рафинирование расплава
Рафинирование или очистка металлических расплавов от растворенных металлических и неметаллических примесей представляет собой одну из главных целей металлургического производства.
Удаление растворенных примесей из железных, никелевых и медных расплавов осуществляется методом окислительного рафинирования, при котором расплав глубоко насыщается кислородом при продувке воздухом или кислородом, при использовании окислительного шлака, а также за счет создания окислительной атмосферы в пламенных печах. Растворенные примеси, обладающие высоким сродством к кислороду, связываются в свободные оксиды обычно в виде твердых или жидких фаз.
Характерным примером образования газовой фазы при взаимодействии примеси с кислородом является монооксид углерода СО, образующийся при обезуглероживании металла, например Fe, который в виде пузырьков выходит из расплава, создавая эффект «кипения» расплава.
Рассматриваемый способ удаления примесей из расплава не позволяет удалить из расплава легирующие компоненты, обладающие малым сродством к кислороду. В железных расплавах такими примесями являются, например Ni, Сu, в никелевых – Сu.
При насыщении расплава кислородом, наряду с образованием примесными элементами оксидных фаз, происходит в определенной степени насыщение металла-основы кислородом. В связи с этим после окислительного рафинирования должно быть обязательно проведено раскисление расплава, т.е. удаление избытка растворенного кислорода.
Растворенные в расплаве примеси, обладающие малым сродством к кислороду, могут быть удалены при наличии сильно восстановительных условий, когда атомы подобных примесей образуют отрицательно заряженные ионы, взаимодействующие с положительно заряженными ионами металла в шлаке с формированием нерастворимого в расплаве соединения. Подобное явление лежит в основе процесса удаления серы из железных расплавов, осуществляемого за счет образования сульфида кальция.
В некоторых случаях удаление растворенной металлической примеси может быть достигнуто обработкой расплава не воздухом или кислородом, а другими газами, например, хлором. Продувка алюминиевых расплавов газообразным хлором позволяет снизить содержание магния с 3–5 до 0,5 %, содержание натрия с 0,03 до 0,002 %. Процесс очистки обеспечивается благоприятным соотношением сродства алюминия, магния и натрия к хлору, свободная энергия образования хлоридов этих металлов при 1000 К составляет: для AlСl3 -531 кДж или -354 кДж на 1 моль Сl2; для MgCl2 = -551 кДж на 1 моль Сl2; для NaCl = -335 кДж или 670 кДж на 1 моль Сl2.
Удаление растворенной примеси из расплава может быть осуществлено в результате ее взаимодействия со шлаком или флюсом. Связывание серы в сульфид кальция при ее удалении из железных расплавов в шлак является весьма характерным примером. Магний из алюминиевых сплавов надежно удаляется до концентраций менее 0,1 % при обработке расплавов криолитом Na3AlF6 в результате протекания обменной реакции
3Mg + Nа3АlF6 = 3MgF2 + 3Na + Аl
Летучие растворенные примеси могут быть удалены из металлических расплавов достаточно высоким перегревом или более надежным способом – плавкой в вакууме. Достигаемая степень очистки зависит от равновесного давления пара примеси, определяемого ее содержанием и коэффициентом активности, от величины остаточного давления над расплавом, от экранирующего действия слоя шлака на поверхности расплава, от условий перемешивания расплава и других факторов.
Для легкоплавких сплавов применим еще один способ удаления растворимых примесей, который основан на снижении растворимости примеси при понижении температуры. Сущность способа можно рассмотреть на примере удаления примеси железа из алюминия. Согласно диаграмме состояния системы Аl–Fe при 900 °С растворимость железа в жидком расплаве составляет 10 % Fe, при 800 °С – 5 % Fe и минимальна при эвтектической температуре (655 °С) – 1,8 % Fe. При наличии в расплаве алюминия примеси железа выше, чем 1,8 %, ее содержание можно снизить за счет понижения температуры расплава несколько выше эвтектической и выделения избыточной фазы FeAl3 в виде кристаллов. Подобным способом возможно снижение содержания железа также в сплавах на основе цинка и олова.
В расплавах обычно присутствуют нерастворимые примеси в основном в виде неметаллических включений эндогенного и экзогенного типа и наиболее часто оксидной природы. Встречаются также включения карбидов, нитридов. Кроме неметаллических включений в расплавах могут присутствовать включения интерметаллидов, а в расплавах на основе магния и свинца встречаются частицы железа.
Для удаления из расплавов нерастворенных примесей, т.е. взвешенных частиц, наиболее просто применить отстаивание, которое не обеспечивает глубокую очистку, но привлекательно своей доступностью и простотой. Неметаллические включения оксидной природы в подавляющем большинстве случаев имеют плотность меньше плотности металлических расплавов и включения всплывают на поверхность расплава. В магниевых расплавах, характеризующихся малой плотностью (~ 1,6 г/см3), включения оседают на дно плавильной емкости. В алюминиевых расплавах с плотностью ~ 2,5 г/см3 оксидные включения также должны были бы оседать на дно, поскольку плотность оксида алюминия равна 3,97 г/см3, однако оксидные плены, смешанные в алюминиевых расплавах, имеют много захваченных пузырьков газа (азота), и поэтому собираются на поверхности. В крупных плавильных печах при длительных выдержках оксидные включения освобождаются от пузырьков газа и опускаются вниз на дно плавильной ванны.
Весьма эффективным способом удаления из расплава взвешенных частиц является обработка расплавов шлаками или флюсами. Сущность способа заключается в переводе нерастворенных частиц из расплава в шлак или флюс за счет их растворения или смачивания. Растворение обычно наблюдается в оксидных системах, представляющих собой рафинировочные шлаки, которые применяют при выплавке сталей и чугунов. Никелевые расплавы ввиду меньшей загрязненности примесными включениями подобной рафинировке подвергаются реже, так же как и медные расплавы. Рафинировочные шлаки обычно более жидкотекучие и химически активные, чем покровные, что обусловлено повышенным содержанием CaO, CaF2, Na2O и, следовательно, по химическим свойствам их более высокой основностью.
Применение флюсов для удаления неметаллических включений из расплавов основано главным образом на поверхностных явлениях (смачивании). В процессе смачивания равновесие наступает обычно, когда включение оказывается не полностью во флюсе, а лишь большей своей долей. Для полного перехода включений с границы раздела во флюс необходима добавочная энергия, которая обеспечивается за счет слабого механического перемешивания.
Для эффективного рафинирования расплавов от нерастворенных взвешенных частиц необходима большая поверхность соприкосновения между расплавом и флюсом, а также перемещение частиц из глубины расплава к поверхности раздела фаз. Это достигается первоначальным активным замешиванием флюса в расплав и поддержанием в дальнейшем слабого перемешивания.
Очистку металлических расплавов от нерастворенных включений можно осуществлять продувкой газами или обработкой летучими веществами, при которой газовые пузырьки, проходя через расплав, захватывают встречающиеся на своем пути частицы и выносят их на поверхность. В связи с этим условия очистки определяются поверхностными явлениями на стыке трех фаз: расплав–флюс(шлак)–включение.
Эффективность рафинирования расплава от нерастворенных примесей путем продувки резко повышается, если используется активный газ хлор или хлориды марганца и цинка. В этом случае улучшение эффективности очистки вызывается тем, что при химическом взаимодействии газов хлора или паров хлоридов с поверхностью раздела фаз межфазная энергия существенно снижается.
Фильтрование расплава
Фильтрование расплавов обеспечивает наиболее полное и надежное удаление нерастворенных примесей из расплавов прежде всего механическим путем, если размер частицы больше размера отверстий в фильтре. Подобным образом работают сетчатые фильтры из стеклоткани для чугуна и медных сплавов и из стали в виде проволочной сетки или перфорированного листа для легкоплавких сплавов на основе А1, Mg, Zn.
Существенно более эффективно фильтрование расплавов через зернистые и спеченные пористые фильтры. Зернистые фильтры представляют собой слой толщиной 30–60 мм из частиц (зерен) диаметром 5–15 мм, в котором средний поперечный размер каналов между зернами составляет 1–3 мм. Спеченные пористые фильтры имеют поры размером 0,5–1 мм.
Следует отметить, что оба типа фильтров способны при фильтровании расплавов задерживать высокодисперсные включения размером до 20–30 мкм. Эффект применения зернистых и пористых фильтров обусловлен удержанием частиц главным образом за счет действия поверхностных сил и химического взаимодействия, приводящего к их адгезии на развитой поверхности материала фильтра.
Физико-химическое взаимодействие включений с материалом фильтра выражается, прежде всего, во взаимном сплавлении, когда включение вплавляется в материал фильтра. Это возможно, когда в системе включение–фильтр имеются легкоплавкие эвтектики.
Данный эффект наблюдается при фильтровании окисленных стальных расплавов через фильтры из динаса или шамота. Оксидные включения в расплаве, содержащие большое количество оксида железа, имеют темную окраску, и при сплавлении с кремнеземом поверхность фильтра, бывшая до этого светлой, покрывается черно-коричневыми пятнами от удержанных неметаллических включений.
В настоящее время фильтрование металлических расплавов как способ повышения их качества широко используется применительно ко всем сплавам. Следует отметить на взаимосвязь процесса фильтрования и раскисления, которая состоит в том, что фильтрование жидкой стали позволяет в определенной мере добиться раскисления расплава.
Модифицирование расплава
Многие сплавы применяются в модифицированном состоянии, которое получают путем специальной технологической операции во время приготовления сплава в конце плавки. Целью модифицирования является получение структуры, отличной от обычной микроструктуры сплава или макроструктуры литой заготовки (без существенного заметного изменения состава сплава), которая обеспечивает повышение механических или технологических свойств сплава.
Модифицирование может осуществляться либо физическим воздействием на расплав, либо введением специальных модифицирующих добавок в количествах, не превосходящих регламентированных техническими условиями весьма низких пределов.
Физические воздействия на расплав обычно заключаются в его тепловой (термовременной или термоскоростной) обработке при нагреве и охлаждении с заданной скоростью, ультразвуковой обработке, воздействии электрического, магнитного, электромагнитного полей. Тепловой обработке расплав подвергают в области однофазного жидкого состояния, все остальные способы модифицирования дают заметный эффект лишь при обработке кристаллизующегося расплава в двухфазной области, т. е. при наличии жидкой и твердой фаз.
Проведение модифицирования осуществляется путем введения в расплав добавок в виде весьма малых количеств (0,01– 0,1 %) элементов, которые обычно по своим свойствам резко отличаются от самого сплава или его основы. Модифицирующие добавки могут быть весьма тугоплавки или наоборот, очень легкоплавки и летучи, обычно они активно взаимодействуют с кислородом, азотом. Для модифицирования сталей часто используют сплав редкоземельных металлов (мишметалл), а также кальций, бор; для чугунов – магний, церий; для силуминов – натрий, стронций и фосфор; для деформируемых алюминиевых сплавов – титан, бор; для алюминиевых бронз – ванадий. Для введения модифицирующих добавок, как правило, используют лигатуры. Кроме обычных лигатур, для введения в расплав элементовмодификаторов можно применять их химические соединения (оксиды, галогениды) в расчете на восстановление элементамодификатора и растворение его в расплаве. Таким путем в чугуны и стали иногда вводят редкоземельные металлы, которые образуются в результате реакции между оксидами РЗМ, углеродом и кремнием, имеющимися в расплаве. Натрий для модифицирования эвтектики алюминий–кремний в сплавах на основе алюминия с кремнием (силуминах) вводится в расплав за счет восстановления из фторида натрия алюминием. Цирконий, бор, титан для измельчения макрозерна отливок из алюминиевых сплавов можно вводить в расплав за счет реакции алюминия с солями (фторцирконатами, фторборатом, фтортитанатом калия).
Общей особенностью всех способов модифицирования является ограниченность во времени эффекта модифицирования. Обычно этот эффект проявляется от 5–10 мин до 0,5 ч. Это связано с выгоранием и окислением введенных добавок, с потерей их активности, изменением структуры расплава. В связи с этим модифицирующая обработка всегда осуществляется как завершающая операция при плавке или во время разливки и даже непосредственно в литейной форме.
Традиционная вакуумная индукционная плавка
Основные процессы при вакуумной индукционной плавке
Индукционная плавильная печь работает по принципу индуктивной связи трансформатора, у которого первичной обмоткой является водоохлаждаемый индуктор, а вторичной обмоткой и нагрузкой – находящийся в тигле металл. Нагрев и плавка металла происходят за счет протекающих в нем токов, которые возникают под действием электромагнитного поля, создаваемого индуктором.
В середине семидесятых годов ХХ в. индукционный нагрев стал способом плавки номер один на заводах цветных металлов и главным методом плавки на сталелитейных заводах. Следует отметить, что большинство крупных печей использовали токи промышленной частоты. В восьмидесятых годах, когда были созданы инверторы, работающие на повышенных частотах, обеспечивающие высокие эффективность и производительность, было отдано предпочтение индукционному методу плавки с использованием печей средней частоты.
В общем случае технологический процесс вакуумной индукционной плавки может быть представлен схемой, приведенной на рис. 3.1. Первичный этап А нагрева шихты и плавления, а также завершающий перегрев расплава А осуществляется индукционным нагревом токами средней частоты. Последующая операция B перемешивания расплава осуществляется электромагнитным методом, в том числе с применением трехфазного способа током промышленной частоты на стадии рафинирования (дегазации) и на завершающей стадии перегрева расплава перед разливкой. Продувка расплава с целью рафинирования (дегазации) C начинается на этапе плавления и продолжается в течение всего процесса плавки.
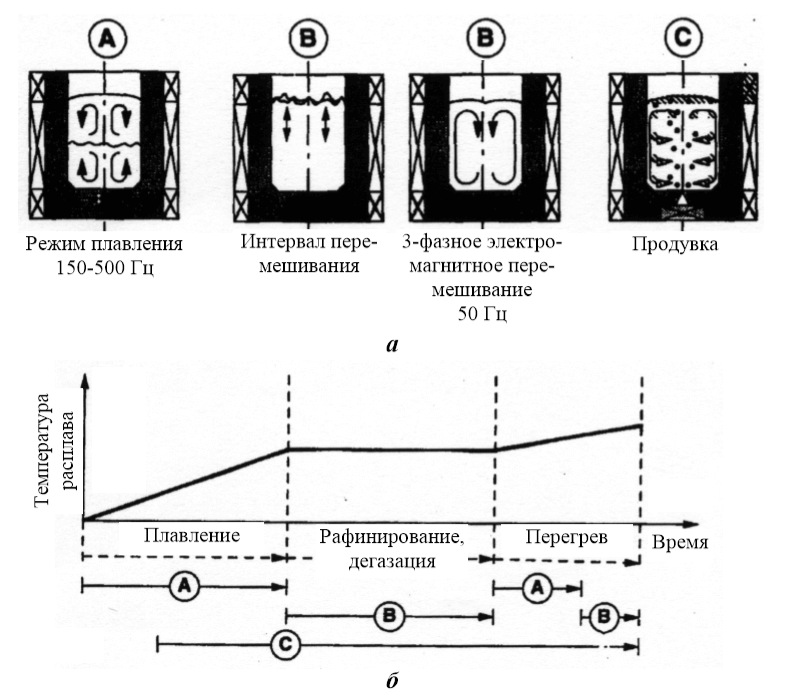
Следует отметить, что гомогенизация расплава с использованием перемешивания расплава обеспечивает высокую однородность химического состава, температуры расплава, уменьшение времени дегазации.
Повышение чистоты расплава от частиц оксидов и удаление неметаллических включений обеспечивается в основном за счет:
- «мягкого» подъема инертных газов сквозь расплав;
- очищения расплава в тигле;
- очищения расплава при протекании по горячему желобу с противошлаковыми барьерами и дополнительным керамическим фильтром с размером ячейки 1–2 мм.
Типы традиционных камерных индукционных печей
В течение последних лет наибольшее распространение в мировом литейном производстве получили индукционные тигельные печи средней частоты камерного типа. Они представляют собой универсальные печные агрегаты, которые способны не только просто переплавлять металл при загрузке от 1 кг до 30 т, но с помощью которых могут решаться специальные технологические и металлургические задачи.
Специализированные металлургические процессы представляют собой физико-химические процессы, происходящие на границе фаз между металлом и шлаком или вводимыми в металл легирующими веществами, а также реакции между металлом и материалом футеровки, или реакции, происходящие в металлической ванне между веществами различной плотности и с различными физикохимическими свойствами. Для управления поверхностными реакциями необходимо правильно и точно управлять нагревом и потоками металла в ванне. При этом саму печь следует рассматривать не только как плавильный агрегат, но и как магнитогидродинамическое устройство, которое управляет интенсивностью движения потоков металла в различных зонах ванны.
Современные плавильные печи камерного типа работают на средних частотах (от 250 до 500 Гц), что позволяет контролировать перемешивание расплава при высоких плотностях мощности (около 1000 кВт/т).
Характерные особенности традиционной индукционной печи ВИП камерного типа следующие:
- объем камеры печи и, соответственно, площадь внутренней поверхности имеют значительную величину;
- опрокидывание тигля и разливка в формы происходят внутри большой камеры печи;
- гидравлические и водоохлаждаемые гибкие силовые кабели находятся внутри вакуумной камеры;
- большая поверхность уплотнений и, соответственно, существует потенциальная возможность натекания;
- требуется большая скорость откачки вакуумных насосов.
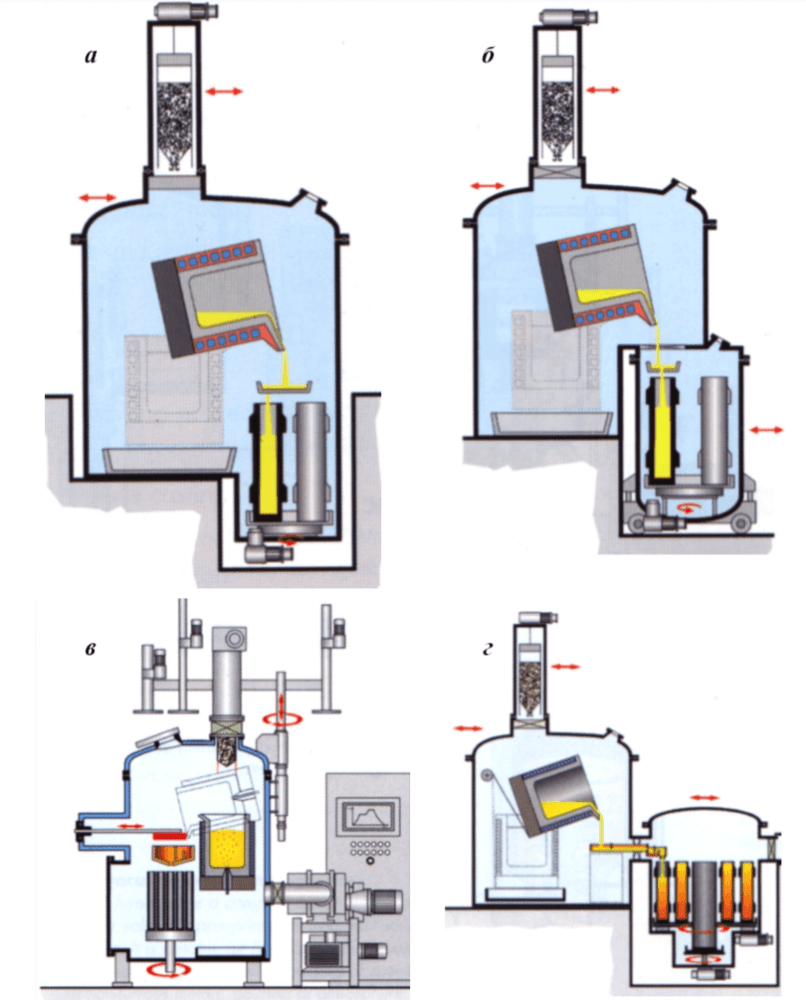
В настоящее время применяются следующие варианты конструкций промышленных вакуумных индукционных печей камерного типа:
- ВИП однокамерная (VIM) (рис. 3.2,а). Типичная загрузка 0,5–15 т; система одиночной камеры с вертикальной плавильной камерой;
- ВИП-ПК с передвижной камерой (VIM-MC movable mold chamber) (рис. 3.2,б). Типичная загрузка 0,5–15 т; двухкамерная система с отдельной передвижной камерой-шлюзом для изложниц;
- ВИП-ДП с донной продувкой (VIM-BP bottom purging) (рис. 3.2,в). Печь с целью обработки расплава газами оснащена предварительно подогреваемым тандишем и тиглем для донной продувки газом;
- ВИП-ЛС с лотковой системой (VIM-LS launder system) (рис. 3.2,г). Двухкамерная система с одной камерой и поворотным столом для коротких и длинных слитков. Сменный подогреваемый лоток для разлива расплава;
- ВИДИСТ – вакуумная индукционная дистилляция (VIDIST – vacuum induction distillation) (схема процесса – рис. 3.3,а). В цветной металлургии испарение легколетучих элементов из расплава используется для дистилляции металлов;
- ВИД – вакуумная индукционная дегазация (VID – vacuum induction degassing) (схема процесса – рис. 3.3,б). Вакуумная индукционная дегазация с малым объемом камеры печи применима для цехов стального литья и литейных заводов. Используется для плавления и дегазации специальных сталей и сплавов с разливкой в ковш или литейные формы. Емкость печей от 1 до 15 т;
- ВИП-ДД с двух дверной компоновкой (VIM-DD double-door arrangement). Типичная загрузка 5–30 т, двухкамерная система с горизонтальной плавильной камерой и двумя сменными индукционными печами;
- ВИП-ГПК с горизонтальной передвижной камерой (VIM-HMC horizontal mold chamber). Типичная загрузка 0,5–10 т; двух- или многокамерная система с боковой дверцей и сменной печью. Гидравлическое наклонное устройство и кабели электропитания расположены снаружи.
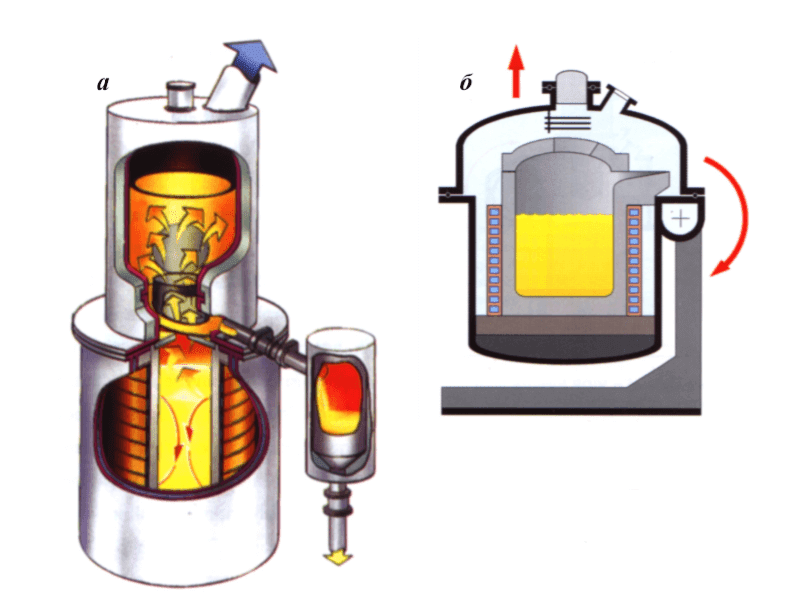
Современная промышленная индукционная плавка
Преимущество современной промышленной вауумной плавки с использованием печей типа VIDP (Vacuum Induction Degassing and Pouring Furnaces) состоит в следующем.
- Компактная конструкция с минимально возможным объемом корпуса обеспечивает повышение эффективности благодаря меньшему потреблению инертного газа при заполнении, более экономичной системе вакуума и значительным снижением высоты цеха и занимаемой площади.
- Оптимальный контроль за атмосферой над ванной расплавленного металла посредством минимизации или удаления нежелательных газов при утечках из гидравлической и водяной систем, десорбции с поверхности корпуса, дегазации тигля и т.д.
- Все этапы от загрузки сырья до разливки проходят в вакууме или в атмосфере защитного газа; разделительные клапаны между камерой загрузки, плавильной камерой, камерами разливочного желоба и изложницы обеспечивают гибкое управление.
- Разливочный желоб позволяет достичь намного большей чистоты конечной продукции благодаря соответствующему расположению шлаковых затворов и керамических фильтров.
- Передвижная (сменная) часть печи с тиглем позволяет сократить время при новой загрузке, ремонте и обслуживании; расположенные снаружи механизмы наклона, разъемы для подключения подводов для снабжения энергией и рабочими средами облегчают доступ и уменьшают затраты на ремонт.
Вакуумные индукционные печи для дегазации и литья (VIDP-печи)
Вакуумные индукционные печи типа VIDP представляют новое поколение печей для получения металлов и сплавов наивысшей чистоты по классической технологии вакуумного индукционного плавления. В конструкции печи применена концепция закрытых вакуумных печей с наклонным разливочным желобом. В настоящее время печи данного типа практически полностью вытеснили вакуумные индукционные печи с массой садки от 1 до 30 т печи, построенные по камерному типу.
Новейшие разработки в области создания оборудования для электромагнитного перемешивания, продувки инертным газом, непрерывного литья характеризуют сегодняшний уровень техники, применяемой при вакуумной индукционной плавке. Промышленные горизонтальные системы VIDP непрерывного литья применяются, в частности, для выплавки слитков жаропрочных сплавов ∅ 40–200 мм.
Установка VIDP состоит из плавильной камеры, устройства для загрузки, разливочного желоба, разливочной камеры, вакуумных насосов, источника электропитания, а также дополнительных устройств для подачи сред и обслуживания.
Основные этапы процесса промышленной вакуумной индукционной плавки с использованием VIDP-печи.
Вакуумирование/Продувка. Система вакуумирования включает в зависимости от требования к процессу несколько механических насосов, или комбинацию из механических и паромасляных насосов. Вакуумирование камер плавления и разлива, а также шлюзовой камеры может происходить независимо. Устройство для заполнения инертным газом позволяет осуществить быструю продувку плавильной, а также разливочной камер для осуществления процесса или быстрого повышения давления в случае сбоя, например при вскипании расплава.
Загрузка. Тигель может загружаться компонентами сплава в виде шихты как на воздухе, так и под вакуумом.
Плавление. Расплавление происходит по принципу индуктивного нагрева. Плавильным сосудом является расположенный внутри цилиндрического индуктора тигель из графита или керамики. Применяются предварительно изготовленные монолитные тигли, тигли из сегментов или тигли, изготовленные путем спекания набивной массы непосредственно в печи.
Измерение температуры. Температура измеряется при помощи термоэлемента, который погружается в расплав посредством подъемного загрузочного устройства, возможен также замер температуры с помощью пирометра.
Взятие пробы. Для взятия пробы расплава на подъемном устройстве загрузочной корзины закрепляется специальная изложница. Процесс происходит аналогично замеру температуры.
Легирование. Процесс легирования осуществляется по методике обычной загрузки в вакууме; для легирования, как правило, используют загрузочные корзины небольшого объема.
Удаление шлака из тигля. Образующееся при плавке в вакууме небольшое количество шлака может быть удалено путем погружения холодной пластины. Следует также учитывать, что при последующей разливке с использованием разливочного желоба производится дополнительное отделение частиц шлака.
Дегазация. Массоперенос газа из расплава через поверхность ванны расплавленного металла, представляющей собой границу между вакуумом (газовой фазой) и расплавом, а также через поверхность пузырьков газа, используемого при продувке расплава, приводит к дегазации расплава. Значительное улучшение перемешивания ванны во время фазы дегазации или рафинирования, дает специальное трехфазное устройство для перемешивания.
Гомогенизация. Для равномерного распределения легирующих материалов и для равномерного распределения температуры расплав эффективно перемешивается электромагнитным методом.
Разливка. Разливка происходит при помощи разливочного желоба, соединенного с разливочной емкостью. Способ разливки варьируется для литья слитков, электродов или мерных заготовок. Разливочный желоб может быть изготовлен отдельно или с подсоединяемой разливочной емкостью (тандишем).
Литье слитков, электродов, мерных заготовок. Размеры изложниц (литейных форм) определяют оптимальный объем разливочной камеры, который гарантирует быстрое вакуумирование.
Замена печи. Концепция закрытой вакуумной печи позволяет осуществить быструю (менее 1 ч) горячую замену части печи с индуктором и тиглем. При помощи нескольких сменных частей печи, возможно с тиглями разных размеров, установка оптимально приспосабливается к производственным требованиям, а ее производительность значительно повышается.
Управление и контроль. Параметры процесса и показатели состояния всех важных функций установки регистрируются. Наблюдение за расплавом и процессом литья происходит на отдельных мониторах посредством видеокамер, пригодных для работы в печи. Дополнительно предусмотрены смотровые стекла для непосредственного визуального наблюдения.
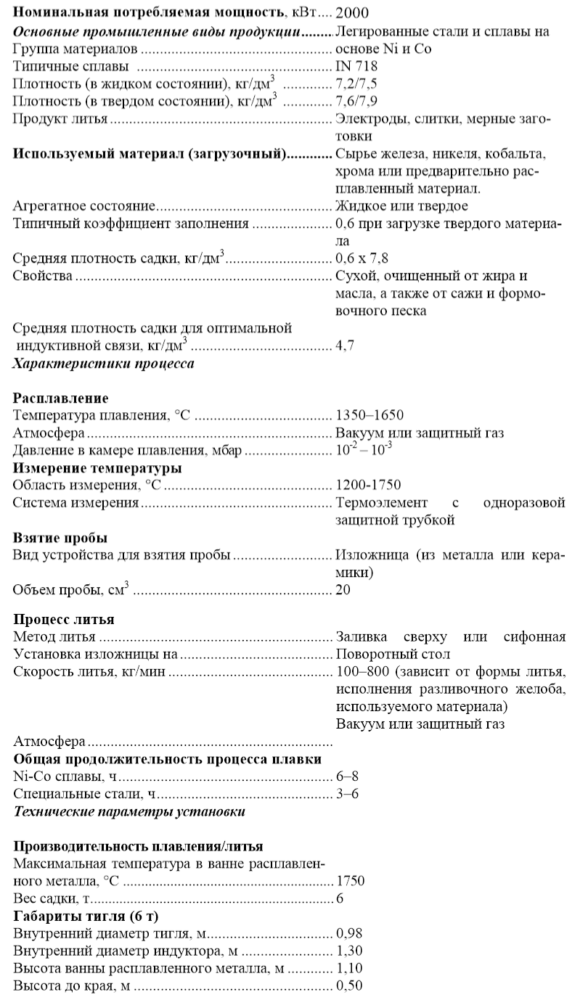
Схема действия VIDP-печи и операция выпуска расплава с использованием разливочного лотка приведены на рис. 4.1.
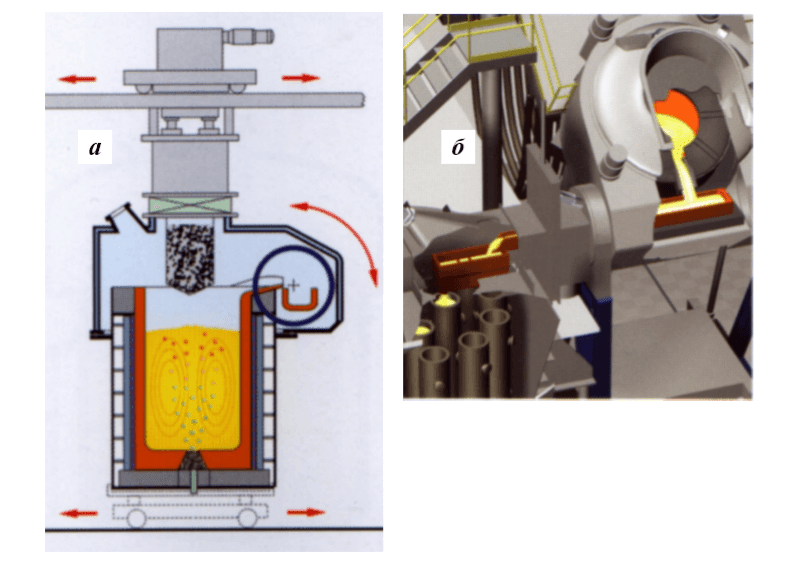
Система контроля состояния тигля. С помощью системы контроля состояния тигля определяются эрозия, инфильтрация, трещины в тигле и обеспечивается безопасная продолжительная работа тигля. Принцип действия системы основан на измерении сопротивления между расплавом и чувствительными электродами на индукторе. При повреждении тигля происходит замыкание расплава с оплеткой датчика и следует автоматическое отключение печи.
Электромагнитное перемешивающее устройство (3-фазное, частота 50 Гц). Электромагнитное перемешивание оптимизирует условия дегазации и гомогенность расплава и, соответственно, приводит к уменьшению времени обработки расплава и к повышению производительности печи. Дегазация, рафинирование и гомогенизация расплава осуществляются при 3-фазном электромагнитном перемешивании в условиях представленных фотоснимком на рис. 4.2.
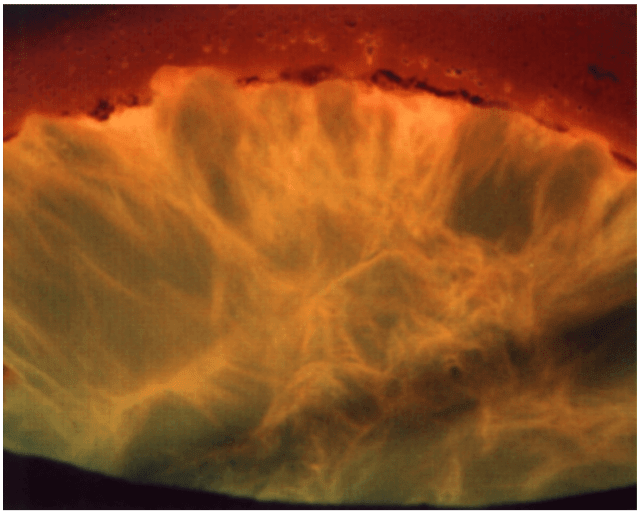
Вакуумная индукционная плавка в “холодном” тигле
В связи с тем, что металлы, отличающиеся высокой химической активностью в расплавленном состоянии, при плавлении в обычной вакуумной индукционной печи с керамическим тиглем интенсивно взаимодействуют с материалом тигля, а также, поскольку в случае тугоплавких металлов керамические тигли нельзя использовать, существовала проблема их получения методом вакуумной индукционной плавки.
Химически активные металлы, такие, как титан, цирконий, материалы для хранения водорода и сверхпроводящие материалы, магнитные и интерметаллические сплавы, высокотемпературные сплавы получают с высокими требованиями по чистоте и жестким контролем структуры. Применение метода индукционной плавки и литья в холодном тигле позволяет преодолеть основные ограничения традиционного метода индукционной плавки с керамическими тиглями.
Преимущества применения «холодного» медного тигля
Для преодоления проблемы применения керамических тиглей в плавильных устройствах вакуумных индукционных печей стали использовать так называемые «холодные» тигли, т. е. контейнеры, рабочая температура которых ниже температуры плавления переплавляемого материала. В результате разработки конструкции медного тигля и способа локального выделения тепла в садке (загружаемой шихте) удалось создать устойчивую ванну расплава, непосредственно соприкасающуюся с холодным тиглем, или отделенную от него слоем нерасплавившегося материала.
Основным элементом вакуумной индукционной печи, определяющим уникальные возможности плавки химически активных и тугоплавких металлов и сплавов, является «холодный» медный тигель, который позволяет:
- устранить какое-либо загрязнение выплавляемого сплава;
- осуществить электромагнитное перемешивание расплава, обеспечивающее химическую и термическую однородность расплава.
Тигель с холодной медной стенкой изготовляют из набора водоохлаждаемых медных сегментов, что позволяет электромагнитному полю индукции воздействовать и нагревать загружаемый в тигель шихтовой материал. Поле индукции производит сильное перемешивание расплава в течение всего времени плавки сплавов с высокой химической и термической однородностью расплава. Поскольку печи этого типа являются индукционными плавильными печами, они могут быть загружены предпочтительно скрапом возврата, токарной стружкой и губкой, а не дорогими расходуемыми слитками. Особенностью метода является возможность сочетания легирования и последующей разливки при одной температуре.
Внешний вид «холодного» тигля с расплавом в процессе вакуумной индукционной плавки приведен на рис. 5.1.
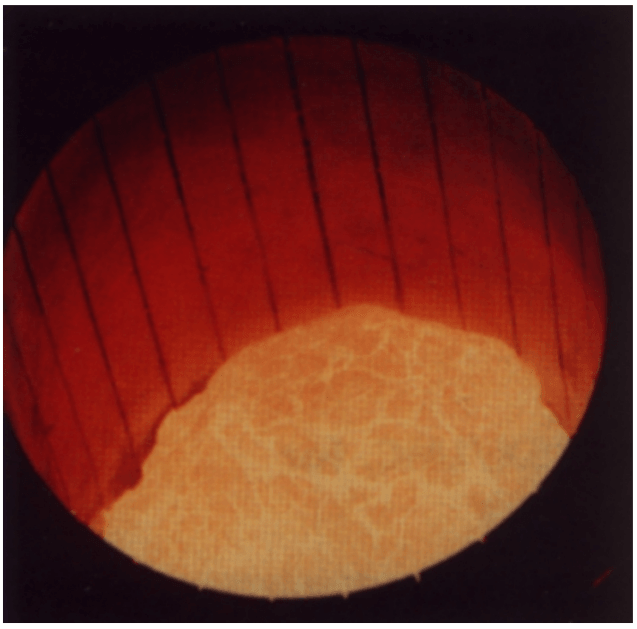
Печи этого типа, как правило, характеризуются сравнительно небольшим объемом расплава от нескольких кубических сантиметров до 30 л. Применяются обычно системы наклонного и донного разлива. В промышленном производстве реализуется возможность статического и центробежного литья, а также непрерывного литья специальных сплавов, которая обеспечивается рядом различных конструкций литейных установок вакуумной индукционной плавки.
Промышленное применение вакуумной индукционнной плавки в «холодном» тигле определяется в основном следующей продукцией:
- циркониевое литье для насосов и трубопроводов для химической промышленности буровых установок на шельфе;
- производство быстрозакаленных порошков активных металлов.
- конструкционные элементы и детали двигателей (титановое литье) аэрокосмической отрасли;
- точное литье для медицины, досуга, спорта.
Вакуумная индукционная плавка в производстве порошков быстрозакаленных сплавов
Порошковая металлургия один из наиболее распространенных методов получения изделий из разнообразных материалов во всех отраслях промышленности. Типы материалов, которые могут быть получены этим методом, охватывают широкий спектр: от быстрозакаленных припоев для электронной промышленности и сплавов на основе никеля, кобальта, железа для авиационной промышленности, для хранения водорода, магнитных сплавов до таких химически активных металлов и сплавов, как Ti для производства распыляемых мишеней.
Промышленное производство порошков восстановлением оксидов или распылением расплава струей воды ограничено такими критериями качества, как химическая чистота, отсутствие оксидных фаз, геометрия частиц, и др.
Метод распыления инертным газом в сочетании с вакуумным плавлением в настоящее время является передовой технологией производства высококачественных быстрозакаленных порошков, поскольку удовлетворяет таким особым критериям качества, как:
- гомогенность структуры;
- высокоскоростное охлаждения расплава;
- высокая чистота;
- сферическая форма.
В настоящее время создано оборудование и разработаны методы для промышленного производства быстрозакаленных порошков суперсплавов, высокочистых материалов, и химически активных металлов.
Метод индукционного плавления электрода и газового распыления расплава (VIGA-процесс)
VIGA-процесс (Vacuum Induction-Melting Gas Atomization) осуществляется с использованием вакуумного индукционного плавления и распыления расплава инертным газом.
На этапе вакуумного индукционного плавления по традиционной технологии металл рафинируется и обезгаживается. Полученный расплав подается через предварительно нагретую тандишсистему в зону распыления, где струя расплавленного металла диспергируется под воздействием инертного газа высокого давления. Высокодисперсные капли расплава затвердевают при свободном полете в камере, расположенной снизу распыляющей форсунки, что определяет сферическую форму частиц порошка. Далее порошок в инертной атмосфере подается на циклон, где осуществляется его фракционирование и сбор в герметичные контейнеры.
Схема метода получения порошков быстрозакаленных сплавов с применением вакуумной индукционной плавки и последующего газового распыления расплава (VIGA-процесс) приведена на рис. 6.1. Возможны два варианта метода, отличающиеся тем, что в первом случае расплав подается в зону распыления через промежуточную емкость (тандиш) наклоном тигля, а во втором – путем донной разливки.
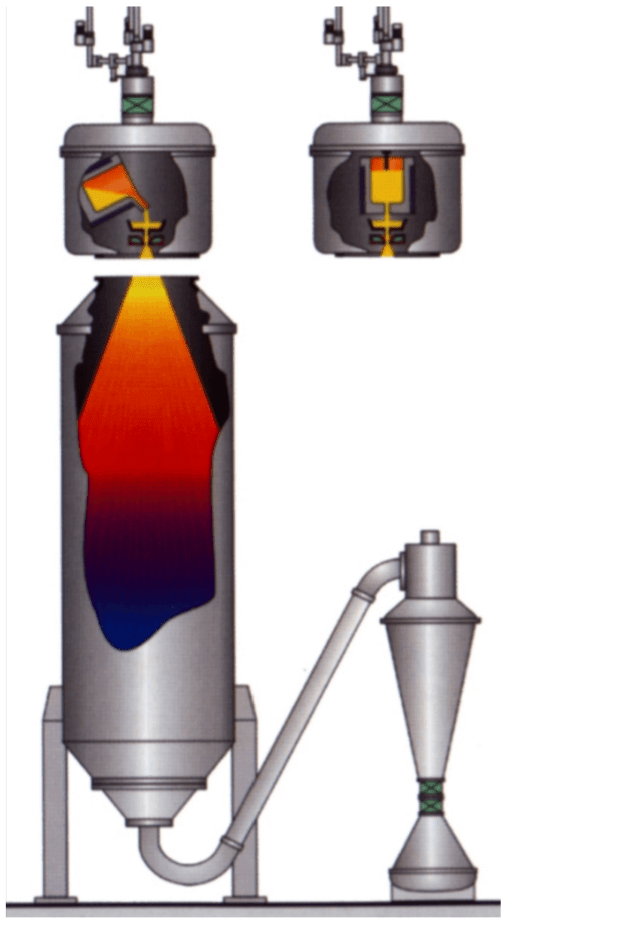
Изготовление изделий из быстрозакаленных порошков обычно осуществляется по ПМ ГИП-технологии.
В связи с тем, что сферические порошки характеризуются хорошей формуемостью и с достаточно высокой насыпной плотностью заполняют формы весьма сложной геометрии, обычно применяется метод заполнения капсул и последующего прессования. Следует отметить, что обычно быстрозакаленные порошки, например никелевых суперсплавов, отличаются высокой твердостью и компактирование их возможно в условиях горячего изостатического прессования.
Вакуумная индукционная “бескерамическая” плавка в производстве порошков быстрозакаленных сплавов
При плавлении по традиционной технологии вакуумной индукционной плавки, осуществляемой в вакуумной индукционной печи с керамическим тиглем, химически активные металлы и сплавы, такие, как Ti, Zr, TiAl, FeGd, интенсивно взаимодействуют с материалом тигля, а для плавки тугоплавких металлов, таких, как Nb, Та и др., керамические тигли непригодны. Особенно активно взаимодействие протекает при увеличении площади контакта расплава с материалом тигля, например при распылении расплава.
Для преодоления «керамической» проблемы при производстве быстрозакаленных сплавов на основе химически активных и тугоплавких металлов необходимо оборудование для плавления и система распыления, исключающие контакт расплава с керамикой. Сравнительно недавно были разработаны такие устройства, которые позволили плавить и распылять химически активные, тугоплавкие металлы и сплавы без использования керамических материалов.
Исключительно чистые порошки быстрозакаленных сплавов востребованы при производстве изделий ракетно-космической, авиационной промышленности, для MIM-технологии и др.
Характерной особенностью таких быстрозакаленных порошков являются уникальные механические и физико-химические свойства, обусловленные эффектом быстрой закалки.
В настоящее время разработан метод, обеспечивающий бестигельное индукционное оплавление электрода распыляемого сплава (EIGA-процесс), а также методы на основе использования водоохлаждаемого «холодного» медного тигля с применением плазменного нагрева (PIGA-процесс), электрошлакового плавления (ESRCIG-процесс) и индукционного нагрева (VIGA-CC-процесс), обеспечивающие возможность плавления химически активных и тугоплавких металлов и сплавов без контакта с керамикой.
Отсутствие керамических материалов обеспечивает высокую чистоту и качество металла. Распыление расплава в случае применения процессов PIGA, ESR-CIG, VIGA-CC осуществляется с помощью CIG-устройств (Cold wall Induction Guiding), представляющих собой индуктивно подогреваемые сопловые системы, которые направляют расплавленный металл непосредственно в зону газового распыления, исключая контакт с керамикой.
Высокочистые порошки получают при распылении расплава, например аргоном, гелием, азотом в высокочистой атмосфере.
Рассматриваемые методы могут обеспечивать более высокую дисперсность микрослитков – гранул, чем метод центробежного распыления вращающегося электрода (PREP).
Преимущества рассматриваемой технологии получения быстрозакаленных порошков заключаются также в оперативной гибкости, высокой эффективности сепарации и очистки с использованием циклонной системы, легкости осмотра, очистки и ремонта оборудования.
Метод бестигельного оплавления электрода и газового распыления расплава (EIGA-процесс)
EIGA-процесс ( Electrode Induction-Melting Gas Atomization) осуществляется с использованием цилиндрической заготовкиэлектрода (литого или спеченного) в качестве расходуемого материала на установках типа EIGA 50/100. Оплавление торца электрода при его медленном вращении происходит в результате индукционного нагрева в индукторе конической формы. Струя расплавленного металла направляется в распылительную форсунку, где она распыляется высокоскоростной струей инертного газа.
Квазинепрерывный процесс получения быстрозакаленных порошков может быть осуществлен за счет использования загрузки нескольких расходуемых стержней.
Схема метода бестигельного индукционного оплавления расходуемого электрода и последующего газового распыления расплава (EIGA-процесс) приведена на рис. 7.1,а.
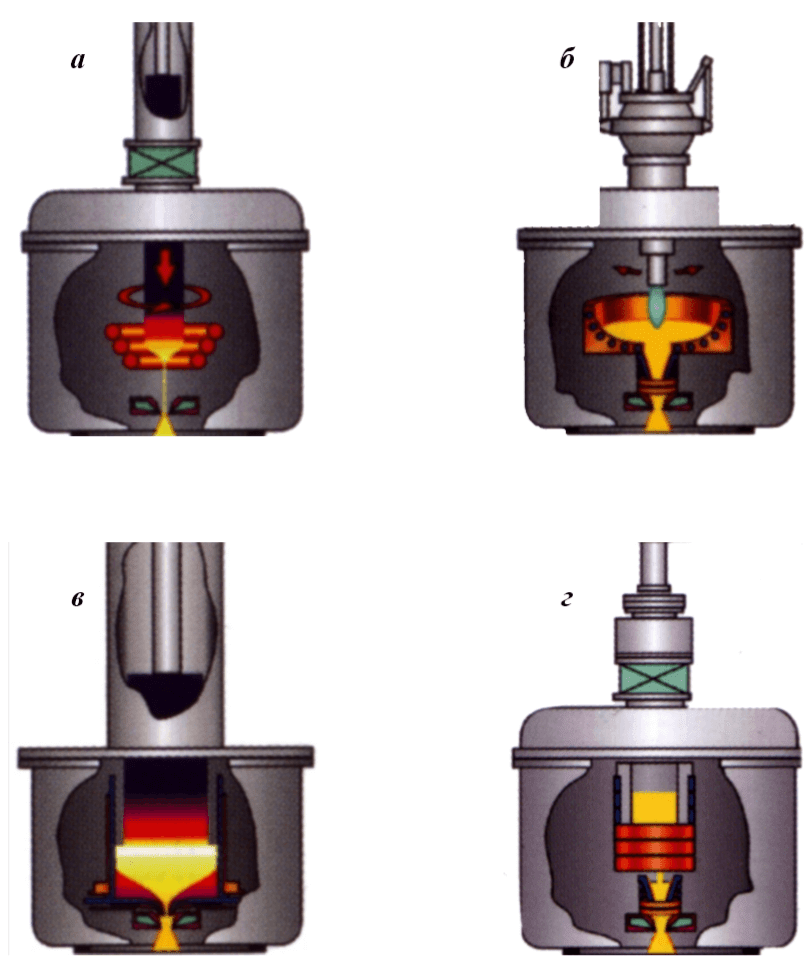
Некоторые характеристики порошков, полученных этим методом на установке EIGA 50, в частности внешний вид и распределение по размерам, приведены на рис. 7.2.

Следует обратить внимание на рис. 7.2 в первую очередь на чистую свободную от загрязнений сферическую поверхность быстрозакаленных частиц порошка и весьма малый их размер при высокой химической активности и высоких температурах плавления сплавов циркония, титана, TiAl и ниобия.
Методы бескерамического оплавления электрода (PIGA-, ESR-CIG-, VIGA-CC-процессы)
Метод плавления в медном водоохлаждаемом тигле и последующего распыления расплава струей инертного газа.
PIGA-процесс (Plasma Melting Induction Guiding Gas Atomization) получения порошков быстрозакаленных сплавов на основе химически активных и тугоплавких металлов так же, как и EIGAпроцесс, осуществляется без контакта расплава с керамикой.
Схема метода плавления в медном водоохлаждаемом тигле и последующего распыления расплава струей инертного газа (PIGA-процесс) приведена на рис. 7.1,б.
Оплавление металла происходит в верхней части медного водоохлаждаемого тигля в результате плазменного нагрева. В нижней части тигля расплавленный металл с помощью CIG-устройства (Cold wall Induction Guiding), представляющего собой индуктивно подогреваемую сопловую систему с «холодными» стенками, направляется непосредственно в зону газового распыления без контакта с керамикой.
Метод электрошлакового плавления в медном водоохлаждаемом тигле и газового распыления расплава.
ESR-CIG-процесс (Electro-Slag Remelting – Cold wall Induction Guiding) сочетает рафинирующий электрошлаковый переплав с преимуществами CIG-системы распыления без применения керамических тиглей.
Метод используется при получении порошков быстрозакаленных сплавов на основе химически активных и тугоплавких металлов, в частности никелевых суперсплавов и высококачественных сталей.
Сущность метода определяется следующими основными процессами. Исходный электрод оплавляется в верхней части медного водоохлаждаемого тигля при контакте с расплавленным в результате резистивного нагрева шлаком. Образующиеся капли расплава проходят через слой рафинирующего шлака и заполняют медный водоохлаждаемый тигель. Полученный рафинированный расплав с помощью индуктивно подогреваемой сопловой системы с «холодными стенками (CIG-устройство) направляется непосредственно в зону распыления высокоэнергетической струей инертного газа без контакта с керамикой.
Схема метода электрошлакового плавления в медном водоохлаждаемом тигле и последующего газового распыления расплава (ESR-CIG-процесс) приведена на рис. 7.1,в.
Метод вакуумного индукционного плавления в «холодном» медномтигле и последующего газового распыления.
VIGA-CC-процесс (Vacuum Induction Melting Gas Atomization based on Cold Wall Crucible Technology) применяется для получения быстрозакаленных гранул сплавов на основе химически активных металлов и сплавов типа TiAl или Ti.
При получении слитков сплавов на основе Ti или TiAl обычно применяется метод вакуумного индукционного плавления в «холодном» медном водоохлаждаемом тигле.
Схема способа получения порошков быстрозакаленных сплавов методом вакуумного индукционного плавления в «холодном» медном тигле и последующего газового распыления расплава (VIGACC-процесс) приведена на рис. 7.1,г.
VIGA-CC-процесс сочетает донную разливку расплава, полученного вакуумным индукционным плавлением в «холодном» медном тигле в условиях применения рафинирования методом донной продувки, с бескерамической CIG-системой подачи расплава в зону газового распыления.
Бестигельное индукционное плавление химически активных и тугоплавких металлов и сплавов, применение бескерамических методов плавления и последующее распыление расплава высокоскоростной струей инертного газа с формированием порошков быстрозакаленных сплавов, представляющих собой наноматериалы, открывают широкие перспективы для разработки новых материалов с уникальными свойствами.
Следует отметить, что применение метода индукционной плавки с последующим высокоскоростным охлаждением расплава при его спиннинговании или экстракции расплава, как правило, позволяет достичь еще более высоких скоростей охлаждения расплава и получить быстрозакаленные сплавы в аморфном состоянии.
Проведение кристаллизации аморфных материалов в твердом состоянии при последующей их термический обработке является перспективным способом формирования нанокомпозитных структур.
Выводы
При получении металлов и сплавов одной из важнейших операций является выплавка слитков. Качество литого металла – его макро- и микроструктура, однородность состава, наличие дефектов в значительной степени определяют уровень служебных и технологических свойств и, следовательно, возможность применения необходимых способов дальнейшей обработки при изготовлении изделий.
Вакуумная индукционная плавка занимает одно из ведущих мест в широком спектре различных способов плавки. Отличительными особенностями ВИП являются:
- высокая степень однородности состава;
- высокая степень однородности температуры расплава;
- высокая эффективность дегазации и рафинирования;
- возможность выплавки прецизионных по составу сплавов;
- гомогенность структуры.
Современная тенденция развития традиционной металлургии характеризуется сочетанием ВИП с другими способами переплава металла в виде дуплекс- и триплекс-процессов (ВИП+ВДП, ВИП+ЭШП и др.) с целью повышения уровня технологических и служебных свойств литого металла.
Разработка способа регулируемого трехфазного электромагнитного перемешивания позволяет повысить гомогенность расплава по сравнению с обычным электромагнитным перемешиванием при индукционной плавке.
Возможность бестигельной вакуумной индукционной плавки, при которой плавление металла осуществляется во взвешенном состоянии без контакта со стенками тигля, эффективно используется при плавке химически активных металлов и сплавов.
Перспективный бескерамический метод ВИП с использованием «холодного» тигля основан на применении медного водоохлаждаемого тигля особой конструкции, которая позволяет осуществить индукционный нагрев шихты, загружаемой в тигель. Метод вакуумной индукционной плавки с «холодным» тиглем позволяет получать слитки химически активных металлов, взаимодействующих при плавлении с материалом тигля, а также тугоплавких металлов, для которых использование традиционных керамических тиглей невозможно.
Основными технологическими операциями при проведении вакуумной индукционной плавки являются дегазация, раскисление, рафинирование, фильтрование и тепловая (термовременная или термоскоростная) обработка расплава.
Физико-химические процессы при дегазации, протекающей по гомогенному или гетерогенному механизму выделения газа, определяются влиянием на растворимость газа в расплаве температуры расплава, наличия инородных (нерастворимых) включений и дефектов в их структуре. Использование дополнительного трехфазного электромагнитного перемешивания позволяет интенсифицировать дегазацию расплава по сравнению с обычным электромагнитным перемешиванием при индукционной плавке.
Продувка расплава высокочистым инертным газом (или газом, чистым по данной газовой примеси) является важным способом дегазации от таких основных вредных газовых примесей, как водород, азот. Более интенсивное протекание процесса перехода газа из жидкой фазы в газовую (дегазация) по сравнению с выдержкой «спокойного» расплава происходит за счет эффекта значительного увеличения поверхности раздела жидкой и газовой фаз.
Дегазация расплава от вредной примеси кислорода в металлургии рассматривается отдельно, как весьма важный процесс раскисления расплава, физико-химические основе которого определяются в первую очередь термохимией взаимодействия кислорода с элементами-раскислителями.
Рафинирование расплава, представляющее собой очистку расплава от растворимых и нерастворимых металлических и неметаллических примесей, является одной из важных задач металлургии. Оно осуществляется способами, основанными на физикохимических процессах:
- взаимодействия удаляемых примесей с кислородом, хлором и другими газами при продувке;
- взаимодействия примесей со шлаком и флюсами;
- взаимодействия с газовой фазой при плавке в вакууме, а также на температурной зависимости растворимости при использовании термической обработки расплава.
Актуальным направлением повышения качества расплава, его чистоты от примесей является фильтрование. Физико-химические процессы при фильтровании весьма сложны и в основном определяются явлением адсорбции примесей и эффектом смачивания на развитой поверхности пористого материала фильтра, имеющего обычно поры размером около одного миллиметра, в результате действия которых осуществляется глубокая очистка расплава, в том числе включений микронных размеров.
Применение бестигельного индукционного оплавления слиткаэлектрода, а также бескерамических методов плавления и последующих операций высокоскоростного охлаждения расплава, в частности распыления расплава с формированием порошков быстрозакаленных сплавов, размерный параметр структуры которых достигает наноуровня, открывает широкие возможности для разработки новых материалов с уникальными свойствами – наноматериалов. Широкое применение вакуумной индукционной плавки имеет место при получении быстрозакаленных сплавов в аморфном состоянии путем спиннингования расплава или при экстракции тонкой пленки расплава на быстровращающемся медном диске. Последующая термическая обработки, характеризующаяся протеканием кристаллизации аморфного материала в твердом состоянии, обеспечивает получение нанокомпозитов.